Plain Bearings
There are two broad types of bearings used in machinery today: plain and rolling element bearings. This article targets the special lubrication requirements of plain bearings, also known as sleeve bearings and journal bearings.
The plain bearing consists of a shaft, also called a journal, and a supporting component, which may be a shell around the shaft called a sleeve, a half shell that the shaft fits into, two half shells (top and bottom parts) or a multipart shell.
Plain bearings are used for high radial loads (perpendicular to the axis of the shaft) and low to high speeds. Typical applications include turbines, large milling systems, engine cranks, compressors, gearboxes, shaft bearing supports, etc.
Every sleeve bearing has some common design characteristics as shown in Figure 2.
The components that are separated by the oil film in a plain bearing are the bearing liner and the shaft. The shaft is composed of high-quality, wear-resistant, structurally strong steel. The bearing liner may be made of a single layer or multiple layers, depending on the design features of the equipment (Figure 3).
Lubrication Regime
Under normal operating conditions, the lubrication regime will be a hydrodynamic full-fluid film. A hydrodynamic film occurs when there is sufficient lubricant between the lubricated surfaces at the point of loading to form a fluid wedge that separates the sliding surfaces. In this state, the lubricated components do not touch each another, reducing friction and wear.
This condition is represented by the equation ZN/P, where Z = viscosity, N = speed (rpm) and P = load. This equation is represented by Figure 4. The curve on this graph is called the Stribeck Curve. It is the classical representation of the relationship between speed, load and friction.
Mixed film conditions occur when a loss of the film resulting in momentary contact between the two surfaces is apparent. This can occur in response to momentary variations in loading, called shock-loading, that can collapse the film, resulting in physical contact of opposing asperities.
Another condition that can occur is boundary film lubrication. This is when the film that separates the surfaces undergoes significant loss resulting in a high load of metal-to-metal contact. This happens any time the relative motion of component surfaces are slow and no oil film is formed.
Lubrication Needs of a Plain Bearing
Operating under proper speed, surface area, viscosity and oil volume, a plain bearing can support very heavy loads. The balance between these conditions is important. If the load or the speed changes, the lubricant viscosity must be adjusted to compensate for the change. There is no simple formula that is used to calculate the viscosity requirements for oil lubricated plain bearings, but the ZN/P formula demonstrates the results of complex calculations used to arrive at the proper clearance.
Criteria to consider once you have identified the proper viscosity grade include oxidation stability, corrosion inhibition, wear protection, water and air separation properties, etc. Because plain bearings can be used in a variety of applications, there is no single set of criteria that should be used. Selection depends on the equipment design and operating conditions.
Plain bearings are normally oil lubricated, but may be lubricated with grease for slow-speed equipment, particularly if they are subject to frequent starts and stops or the bearings may be physically difficult to reach.
The type and amount of grease depends on continuous replenishment of the body of grease that is held within the dynamic clearances (empty spaces while the bearing is turning) in order to maintain effective lubricant condition and hydrodynamic lift. Equipment with poor sealing characteristics may require a heavier body of lubricant and more frequent replenishment cycles.
Under manual (intermittent) relubrication, the volume and the frequency are influenced by operating conditions, grease quality and available time for the task. Grease selection begins with consideration of the oil to be used. Heavy oils are used to formulate greases used to manually lubricate plain bearings in high-duty service.
After the proper viscosity oil has been selected, then the soap thickener, oxidation and rust characteristics, worked consistency properties, pumpability (for automatic systems) and load-bearing (EP/AW) properties are considered. For long intervals and very heavy loading, solid additives such as molybdenum disulfide or graphite may be incorporated. The solid additives would serve to mechanically prevent metal contact in mixed film and boundary lubrication conditions.
The grease should be pumped into the bearing in front of the load zone and at the location of the grease grooves used for lubricant distribution (Figures 5 and 6).
![]() |
Figure 6
|
Wear and Failure Modes in Plain Bearings
There are several factors that can wipe or damage a plain bearing surface. Abrasive wear is one of the most common. If the wear is caused by a hard particle rubbing between the lubricated surfaces, it is called three-body wear. Wear caused by an asperity on one surface cutting the other surface is called two-body abrasion.
Wear can also result from insufficient volume of lubricant (starvation leading to boundary conditions), overheated lubricant (viscosity at operating temperature cannot support the load causing frictional heat and additional oil thinning), rough surfaces (asperities on the journal cause rubbing), imbalance (improper loading of the support element causing shock loading), journal eccentricity (egg-shaped journal causing rubbing on the high spots), and metal fatigue from improper metallurgy. Journal bearing wear can be effectively monitored by oil and ferrographic analysis.
The telltale indicators that may point to high wear conditions include high metallic particle counts (two levels above norm), darkened metal surfaces, blued metal surfaces and wear metals formed into spirals or platelets. As oils age and become contaminated with moisture or acidic oxidation compounds, we can see evidence of corrosion and metallic oxidation on stationary surfaces in the reservoir.
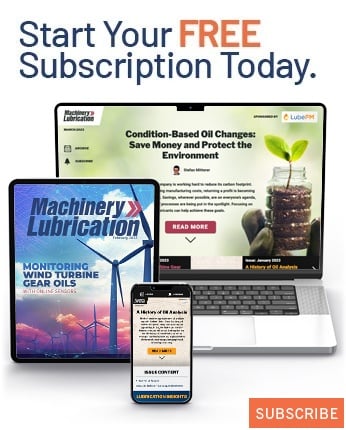