Let's face it: Machines in industry are largely made of iron and steel. Ferrous metals both encase these machines and bear the brunt of most friction, wear and corrosion. Often, the most critical machine components, parts and surfaces are those that possess the greatest intrinsic strength and wear resistance. In more than 90 percent of the cases, these mission-critical components have iron-based metallurgy. Common examples include cams/followers, gear teeth, shafts/journals, rolling elements and raceways of bearings, pistons and cylinders, mechanical couplings, chain drives, screw drives, and rotors.
As machines age and wear, metal is lost to the lubricating oil or grease. The rate of wear is directly proportional to the growing ferrous particle population in our lubricants and filters. These mobilized wear particles pose even greater risk in causing collateral damage elsewhere in the machine. Common examples include particle-induced abrasion, surface fatigue and motion impediment of sliding and rolling parts. So, too, it is well known that metallic particles are a principal root cause of lubricant aging and base oil oxidation.
With rare exception, ferrous particles caused by mechanical wear are also ferromagnetic, meaning these particles have inherent magnetic susceptibility. In some cases, this attribute is a drawback (e.g. the potential interference of solenoid actuators), but in most cases, it presents a distinct opportunity for efficient wear particle removal and detection. This is the central theme of my column in this issue.
Magnetic Susceptibility as a Contamination Control and Condition Monitoring Strategy
Particles will enter lubricants either from internal or environmental sources. Hence, the first goal of any contamination control program is to create a barrier to contaminant entry (called contaminant exclusion) wherever possible. Consider this: For every particle that is not released into the oil (or is rapidly removed), there may be five or 10 more that are not being generated, or allowed to be ingested, as a direct result. The concept of particles making or abetting the ingression of more particles is well known. When effective, this presents an important machine reliability opportunity to mitigate the destructive and self-propagating consequences of contamination.
There are numerous well-engineered magnet-based particle-removal devices on the market. Many of these products were discussed in an article authored by my son J. Bennett Fitch in the September 2005 issue of Machinery Lubrication (visit www.machinerylubrication.com to retrieve this article). Magnetic filters and separators have the ability to selectively remove ferrous particles at various degrees of efficiency based on such factors as particle size, metallurgical composition, flow rate, viscosity and magnetic strength (flux density).
When the magnetic separation and detection technology is properly selected and positioned in the machine application, the benefits can be extensive (see figure). These include:
Enhanced lubricant oxidation stability: Many lubricants are highly stressed due to exposures from pressurized oxygen, suspended moisture and heat. Ferrous particles are known oxidation catalysts which can figuratively "fan the fire". Their removal from the oil does just the opposite, resulting in an oxidation suppressant. In certain cases, this can permit less expensive lubricants (vs. synthetics, for instance) to be used in applications to achieve extended service life (longer oil drains).
Improved filter performance: When magnetic separators are used upstream of filters, there is the possibility of the system filter benefiting from longer service life and higher particle capture efficiency. This can result in reduced cost of filtration (parts and labor) and enhanced contamination control.
Particle removal in unfiltered fluids: Many machinery lube oils cannot be filtered for a variety of reasons. These include lubed-for-life applications and non-circulating systems (those without a pump and forced oil flow). Examples include splash-fed gearing, bath-lubricated bearings and oil ring applications. In other cases, the type of lubricant is not particularly filterable, such as very high viscosity oils and oils that contain solid or semi-solid additives. While these fluids cannot be filtered, they can usually benefit from magnetic separators as a practical alternative.
Controlling particles during filter bypass: Many filters operate in partial or full bypass for extended periods of time. There is a range of reasons why this occurs, including cold-start conditions, premature filter plugging and load-induced flow surges from hydraulic actuators. There are numerous oil filter applications where no filter bypass indicator or gauge is in use to provide an alarm. For instance, the vast majority of oil filters on diesel, gasoline and natural gas engines have no bypass indicator. Yet, in these same applications, there are numerous causes of premature filter blockage (coolant leak, for instance). In such cases, magnetic particle separators can provide some enhanced particle removal during filter bypass.
Wear particle detection and identification: Sadly, most people are oblivious to the condition monitoring potential of magnetic particle separators and collectors. Oil analysts are well aware of the limitations of relying entirely on oil samples to flag incipient and impending machine failure. Systems that utilize low-micron full-flow filters can strip out more than 99 percent of the wear debris generated by bearings and gears, for instance. The remaining wear particles are often very small and low in concentration, not representing the true debris-generating conditions of the machine. Machines that have high fluid volume or high fluid turnover (i.e., the number of times per hour the fluid passes through the filter) can represent real challenges for wear debris detection and analysis with conventional oil analysis from samples. Conversely, magnetic particle collection devices placed upstream of filters can enable quick inspection and retrieval of virgin particles (freshly formed and not reworked by the machine) for analysis.
One Part of an Overall Solution
By itself, magnetic devices are not a cure-all for contamination control problems and fault detection needs. However, when used in combination with other prudent maintenance practices and technologies, an overall enhanced level of machine reliability at a lower cost can be achieved. Years of experience from the user community have provided ample evidence and motivation to deploy magnetic separators and detectors wherever possible.
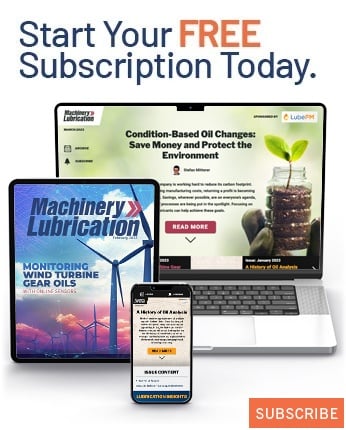