Overwhelming evidence suggests that poor machinery lubrication spells trouble. So why do most organizations lack clearly defined written procedures for performing basic lubrication tasks?
I routinely ask my consulting clients and seminar students if they have lubrication procedures. They sheepishly admit that they don’t.
They often look embarrassed to have to admit it, but I believe these folks represent the cream of the crop. If they are attending Noria classes on lubrication, or are having their program audited, they must have good intentions.
While visiting a client recently, I asked a sophomoric lubrication technician to describe the guidance he received when he took on the role (such as training, procedures, etc.). He said that when he started two years ago, he was shown the way to the lube room and instructed to get to work.
When I asked how he determined if he was doing a good job, he said that if a machine failed and he got yelled at, he knew he needed to do something different. I suspect that this scenario is more common in industry than we would like to think.
I have outlined four reasons why lubrication procedures are important, and four elements of a good lubrication procedure. I hope these outlines inspire you to act, and light the way forward.
Four Reasons Lubrication Procedures are Important
1. Work Scope
Procedures clearly scope the work an individual is expected to perform. They ensure work is done the way management or engineering requires. If management wants 12 shots of grease pumped into the bearing, allowing 15 seconds to elapse between shots, this desire can be clearly documented in the
procedures.
2. Consistency
In the absence of procedures, five technicians are apt to perform the same task five different ways. In the absence of a procedure, each individual has the freedom to “personalize” the task at hand. Inconsistency produces undesirable results. Documented procedures bring uniformity into the lubrication task while keeping everyone on the same page.
3. Best Practices
A procedure creates the framework for standardizing best practice. It serves as the container in which to pour the experience and expertise of employees, outside consultants, vendors and others into a single document. This convergence process also enables the team to align the procedure to the goals of the organization. Just enough “best practice” for one machine may be too much for another, depending upon the relative importance of the two machines to plant operations, even if the two machines are identical in design.
4. Training
Arguably, the most important role of lubrication procedures is that they form the basis for training lube techs. Basic training about lubrication, lubricants, oil analysis, etc., is designed to provide the foundation that enables the individual to think like a lube tech. Certification is another important part of the training process because it confirms that the individual possesses the skills to perform the job functions.
This is called technology training. While it is important, technology training fails to convey specific task-based instructions for completing a lubrication-related work order. A set of procedures serves as a natural curriculum for task-based training. It also serves as the basis for evaluating an individual’s ability to carry out the assigned tasks. Combining basic technology training and third-party certification with task-level training and skill-verification creates a powerful combination and a valuable employee.
What Makes a Good Lubrication Procedure?
1. Emphasize Best Practice
As previously mentioned, procedures enable the incorporation of best practice. However, this is not automatic. A concerted effort must be made to build best practice into the procedure. Access the experience and knowledge of your own maintenance team, and bring in outside support as required to ensure that your procedures are up-to-date and aligned with your business goals.
2. Communicate Clearly
Use clear, easy-to-understand language when creating procedures. Also, use digital photographs to reduce the procedure’s dependence upon words. For intricate tasks, a digital video is an excellent way to communicate tasks that are difficult to describe with words. I like procedures that include a top-view of the plant, along with easy-to-spot landmarks, ones which reveal the location of the machine. Getting to the right machine is the first step.
Use sketches or photos to identify the physical location of the lube point too. Lube points are occasionally missed because their location is unknown to the tech. Identify required tools and materials for completing the job, to improve work planning and assembling a tool kit. Also, don’t forget to identify general safety practices and any specific hazards associated with performing a particular lubrication task.
3. Electronic
Get your lubrication procedures in an electronic form, preferably on your company-wide intranet, or onto an Internet account for those of you moving toward Web-based application support. When the procedures are electronic, they can be updated globally, attached to work orders and linked to like machines in your CMMS system.
Digital photographs and video images can easily be attached to a document. Documenting your procedures electronically makes sense. It is more efficient and effective than the old paper and three-ring binder method.
4. Continuous Improvement
There is a downside to procedures. Without management, they can anchor the organization to the past, inhibiting the inclusion of new technology and best practices. Be sure your program includes a periodic review and improvement process to update and upgrade lubrication procedures.
Keeping your procedures in an electronic form simplifies continuous improvement because updates don’t require tedious activities to physically replace pages in your lubrication manual. Changes can be documented and communicated in one memorandum, while updating the procedures themselves requires only the touch of a button.
In sports, winning teams execute the basics well and have coaches who teach the basics. Knowing the playbook is fundamental to the success of the team. Does your team have a machinery lubrication playbook that you can point to with pride? If the answer is no, you have a great opportunity to eliminate a major cause of failure and waste.
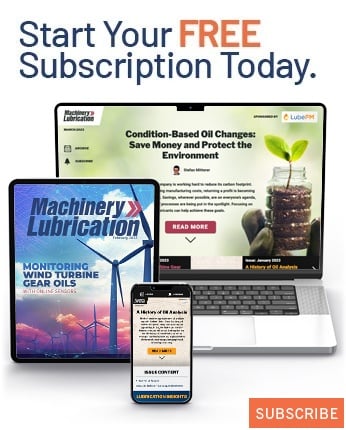