The typical industrial lubrication program lacks order, structure, continuity and respect, even though the ideas and practices have been around for 100 years. Billions of dollars are spent annually to replace lubricated machinery components that have worn out due to the inability of the lubricant and the lubrication process to perform the required task.1

In addition to that expenditure, millions are spent analyzing lubricants at in-plant and commercial laboratories for the purpose of identifying evidence of failed lubrication.
Further, this is one area of plant operations that can yield a powerful return on a meager investment. Case in point: a typical maintenance budget in a capital-intensive operation (steel, paper, rubber, automotive, etc.) can be approximately divided into two parts: labor (+/- 55 percent) and materials (+/- 45 percent). Each part can be further split.
The labor component can be divided roughly into standard (35 percent) and overtime (10 percent) labor. The materials portion can be divided roughly into three sections. For the sake of argument, we will line item lubricants (2 percent), miscellaneous materials (13 percent) and MRO supplies (40 percent).
From this it can be seen that the cost of the lubricant is one of the smallest line items in a typical budget, at 1 to 3 percent; yet the manner in which this budget is applied has an immediate and potentially significant impact on the balance of the maintenance budget (overtime and OEM lubricated component purchases).
Any improvement in this sliver of the budget ($100K to $300K in a $10 million budget) could produce a leveraged savings from one of the largest single categories in the budget, that being overtime and material costs($2.5 million in a $10 million budget).
It is not hard to conceive of a $100K investment in lubrication program improvements yielding $400K in maintenance cost reductions in overtime labor and replacement parts. It is not unusual to achieve improvements with this degree of relative impact.
Aside from large, broad-based forces that push formalized business strategies - such as just-in-time delivery (JIT) and manufacturing-to-order (MTO), ISO 9000 certification and global competition - there is plenty of justification to formalize and standardize excellence in lubrication.
What is preventing this process from becoming a center of excellence in a manufacturing environment? I propose that it is a combination of the following:
1. Lack of understanding the importance of excellence in lubrication practices.
2. Lack of understanding how to achieve lubrication excellence.
3. Lack of reinforcement from senior management, including supporting the expense of taking the time to develop procedures and train personnel so that practices can be achieved.
The Role of Management
Senior management needs to be sold on the benefits of lubrication excellence. This is accomplished by showing, in clear and concise terms, how their investment in this process will create value, improve productivity, reduce cost and move the company toward their strategic and financial goals.
As practitioners of plant tribology, it is important to learn how to present a case in a language that senior management will understand so that everyone can see the same potential for gain. Net present value, cash flow, return-on-investment and payback period are financial forecasting methods that need to be fully understood in order to justify new ideas for improvement.
The Role of Knowledge
It has been said that the industrial world rides on a cushion of oil equal to about 10 micrometers in thickness, about the diameter of a blood cell.2
If this is true, then our livelihood in a very real sense rides on a film of oil that is invisible to the naked eye. To protect that livelihood, our perspective needs to be recalibrated so it can be seen, and then we need to learn to protect this very thin film. This is accomplished only through training and personal study in the field of focus.
The more that is known about the dynamic clearance between two mechanical surfaces, the better the foundation for building effective procedures and habits around protecting that oil film.
What is an effective lubrication procedure? A procedure is a step-by-step guideline that directs the user through a task. Therefore, a lubrication procedure would guide the user through a specific lubrication task.
There are many types of tasks, such as: manual bearing lubrication, gearbox filling, gearbox checking, gearbox top-off, gearbox cleaning, kidney loop filtration, sample collection, etc. Each of these tasks will have some degree of uniqueness, as well as a lot of overlap with other similar lubrication tasks.
When preparing a lubrication procedure, consider the following:
1. Strategy - how does the procedure support the broader maintenance strategy?
2. Purpose - what needs to be accomplished?
3. Procedure - how is the task accomplished, including the many details that determine safety, efficiency and effectiveness?
Strategy
The lubrication program should not be an isolated island in the sea of maintenance practices. Lubrication practices should align concisely with the defined, supported goals of the larger maintenance operation.
With increasing demand for equipment availability (to support a make-to-order production schedule), many operations have adopted a Reliability Centered Maintenance (RCM) strategy. Through such a strategy, they’ve identified where and how to devote their energy to manage their equipment.
RCM is a process used to determine what must be done to ensure that any physical asset continues to do what its users want it to do in its present operating context.3
Within this strategy, decide which machines can run-to-failure. Other machines, perhaps similar, must be managed to assure maximum availability. To maximize a limited lubrication resource, the lubrication procedures for a particular machine should fit the broader strategy for that machine.
For example, a gearbox on a conveyor may be designated run-to-failure with an anticipated five-year life span, while an identical gearbox on a similar conveyor may be designated as process critical with the difference between the two units being the material conveyed.
Should both units be treated the same? Probably not. Depending on the number of run-to-failure units on hand, it may be best to develop a procedure to select a lifecycle fill strategy (lubed for life) that incorporates the use of a high-performance lubricant in a sealed application with no planned routine service.
Conversely, while the reliability expectation is higher for the other unit, consider using a product that does not offer the extended lifecycle benefits if the intention is to closely monitor the unit for signs of distress.
As we step into the procedure development process, we need to confirm that the practice for each system aligns well with the stated maintenance goal for that system. This will lead to greater lubrication efficiency and effectiveness at a reduced total cost (such as plant maintenance optimization).4
Purpose
Keeping this strategy in mind, the purpose is to state what is to be accomplished for the lubrication procedure. While there is no single approach to defining the purpose and the individual tasks for the procedure, certain specifics must be included to remove ambiguity and assure compliance. The purpose should include at a minimum:
1. The name of the item to be addressed (example: A/N 10043CD conveyor drive).
2. The objective of the work (semiannual coupling inspection and relubrication).
3. Identification of the individual to perform the task (Lubrication Technician, MLT Level I Certified).
4. Operational and safety conditions (example: equipment must be locked out before work can be accomplished).
5. The amount of time allocated to the task.
The details should identify what is to be done, where it is to be done, who will do the work, tools and materials needed, special issues surrounding the work (safety, operational) and how much time is allotted to the task. In the process of devising and writing procedures, expect to find major similarities between like components grouped by maintenance strategy. A template can be created with a significant amount of generic information or structure to facilitate the process without diluting the results.
Procedure
While keeping the strategy in mind, the procedure needs to support five principles, or tenets, historically referred to as the five Rs of lubrication. The five Rs are:
1. The right product,
2. The right place,
3. The right amount,
4. The right time,
5. The right attitude.
Digging for details is a must for the first four Rs. Sometimes the details are within easy grasp. Sometimes guidelines are developed as progress is made and when the team has a better understanding of what is needed. More likely than not, if we want world-class procedures, we have to develop them in-house, perhaps with the aid of a consultant or specialist. Let’s look at the questions that should be asked for each of these five categories.
Right Product
This pertains to the selection of the lubricant for an application. The OEM should be the starting point for product selection by viscosity grade and boundary film formation properties (AW, EP, solids) for both oil and grease products.
The OEM has probably considered the speed and load required of the operating components and has calculated a minimum viscosity for that condition. However, because the OEM cannot hope to understand your specific operating conditions, factor in actual conditions and modify the OEM baseline recommendation to fit accordingly.
For instance, is the gearbox rated for one speed but operated at another speed? Is the gearbox in an elevated ambient temperature location, or is there significant process temperature transferred throughout the shaft to the gear case? Is there risk of manufacturing or process contamination entering the lubrication compartment before or during installation?
Is the unit accessible? Does the unit have heat control mechanism (heat exchanger, fan)? What lubricant products are readily available to help meet the OEM mechanical and environmental conditions that exist? Can the company accept a specialty lube product for this single application?
The answers to each of these questions must have a bearing on the lube product that is finally selected. One point of interest: it is your equipment, your lubricant and your maintenance strategy. You make the decision that fits your budget and goals. Collect input from various resources (such as the local distributor, OEM, lubricant manufacturer or subject-matter expert) but use internal resources - the company team - to make the final educated decision.
Right Place
This decision is predetermined by plant and equipment design process for the vast majority of applications. Nonetheless, confirm that the details are correct. OEM guidelines are just that: guidelines. Every single lubrication application point must be uncovered, photographed, tagged and reinforced.
This requires having people at the equipment, looking at the drive train or process flow. Often lube lines disappear under a slab of sheet metal, as can be seen from the example in Figure 2.
![]() |
Figure 2. Disappearing Lube Lines
|
Get input from those who install and repair the components behind that slab to know if the right product is going in and that it is going where it is supposed to go.
A cross-functional work team is key to running down all of these details. The operators live with the equipment on a day-to-day basis and generally understand what is missed and what is not.
Right Amount
Assessing oil volume requirements is generally straightforward. For instance, calculate the amount of oil that goes into an isolated, splash-lubricated, wet sump gear case. The level does not change much between stand-by and operating modes.
Circulating oil systems present a greater degree of difficulty because lubrication lines contain oil outside of the reservoir. For circulating systems, factor in the volume of lubricant in transit, and estimate an operating level as well as a stand-by level.
Once the reservoir is filled, the task is to maintain the right predefined level. Grease lubrication is more challenging. Manual grease relubrication is probably the single most out-of-control aspect of machinery lubrication, but it doesn’t have to be that way. The right amount can be calculated easily with a few measurements and quick formulas or charts from bearing suppliers.
After calculating the component requirement from the design criteria, add an environmental factor based on the actual installation, the lubricant properties and the time available for relubrication. Many factors interrelate to influence the volume and cycle. They must be considered in the context to produce a whole picture.
The Right Time
The timing of relubrication intervals is influenced by many of the same factors that influence relubrication quantities. Start with the OEM guideline and adjust to maximize the properties of the lubricant within the context of the application and environment. The environment will have a significant impact on grease relubrication intervals but less so on oil lubricated equipment. The most difficult part of this procedure is identifying the operating and design details.
The Right Attitude
Regardless of the level of efficiency and accuracy in defining the physical properties and requirements for optimum lubrication, the human element is the trump card. Well-defined but poorly followed practices are of marginal value. Likewise, highly motivated people without role definition will either find a way to define their role or will loose interest.
The right attitude boils down to a personal decision made by the lubrication technician, but it is greatly influenced by the senior management’s attitude toward the role. If a subliminal message of ‘oil is oil and grease is grease’ is reinforced by low wage scale, shallow job title, neglected training and refusal of access to resources to improve the process, then inferior motivation and inferior results are often present. Don’t underestimate the significance of this.
When all is said and done, after we have formed a maintenance strategy and chosen to standardize lubrication procedures and done all of the footwork and thinking necessary to make the best decision, and then boiled those decisions down into a coherent, common sense, concise procedure, the real work begins. It is not easy to achieve day-to-day consistency in what is arguably a hot, dirty and difficult work environment, but the rewards can be measurable, lasting and substantial.
A Dollar Saved . . .
The perpetual nature of the lubrication process offers both challenges and rewards. The benefits and drawbacks are cumulative. By refining the strategy, working through the details and devising high value procedures, we can position ourselves to add long-lasting value.
Every dollar saved through a new lubrication improvement is saved over and over again. This is called an annuity. This makes each dollar saved worth much more than the face value of the initial dollar saved.
The process is both orderly and detail oriented. Consider operational circumstances and then correctly identify the right product, the right place, the right amount, the right time, and then apply these excellent practices with the right attitude.
To achieve and maintain a competitive position in a hyper-competitive world, a company must work as a team to build value in each segment of the process. The development of world-class lubrication standards and practices is long overdue in many organizations.
It is hard but honorable work and should be done.
References
1. Rabinowicz, E. (1995). Friction and Wear of Materials, Second Edition. John Wiley & Sons, Inc.: New York, NY.
2. Troyer, D. Lubricant Condition Monitoring: A Proactive, Reliability Driven Approach. Diagnetics, Inc.: Tulsa, OK.
3. Moubray, J. (1997). Reliability Centered Maintenance. Second Edition. Industrial Press, Inc.: New York, NY, pg. 7.
4. Moubray, J. (1997). Reliability Centered Maintenance. Second Edition. Industrial Press, Inc.: New York, NY, section 11.3, pg. 218.
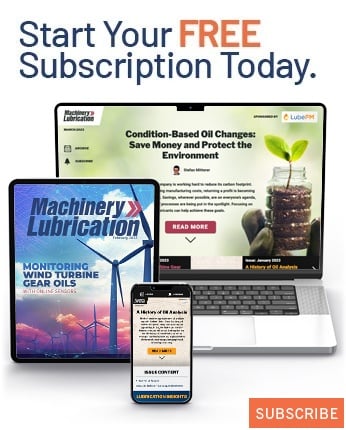