A world-class lubrication and lubricant analysis program requires individuals with world-class skills. While it is true to say that those directly responsible for lubrication must be properly trained, other individuals in the organization also require knowledge, or at least awareness of the program’s goals, primary benefits and fundamental tenets. In order for the organization as a whole to succeed in lubrication excellence, it is vital that a lubrication and lubricant analysis skill development program is put in place and tailored to meet the needs of all the individuals who affect, or are affected by poor lubrication.
Lubrication Training
Almost everyone in a plant needs some lubrication awareness training. The lubrication topics selected and the degree to which they should be covered depends upon the individual’s job. For example, it doesn’t make sense to put the plant manager through a detailed training program on the use of a grease gun. That is simply not a skill the plant manager is going to put to good use. While this is a good example that is generally applicable, each plant or company needs to develop its own specific lubrication training objectives based on its different staff categories.
The skill inventory and training program will vary from organization to organization. As an illustration, consider a plant with the following lubrication related job descriptions:
Reliability and PdM Analyst
This skilled individual is responsible for assuring reliability of the plant and is the primary technical resource to the plant on maintenance and reliability issues. His or her role is to run onsite oil analysis tests, assimilate and evaluate data from both onsite and off-site oil sample analysis and to interface with the other reliability team members from the vibration and thermography groups. To provide this support, the analyst requires a thorough understanding of all the lubrication and oil analysis functional skill areas.
To achieve the desired level of knowledge for this position, this individual typically needs several weeks of training on the basics of lubrication and lubricant analysis. He may also require extensive training on various procedures for which he will be responsible (sampling for example). In addition, extensive specialized training is required on the correct use, maintenance and calibration of onsite test equipment. This individual also requires frequent training to keep knowledge and skills up-to-date and should be actively involved with appropriate conferences and meetings to hone skills, make contacts and benchmark best practices.
Lubrication Technicians
Skilled lubrication technicians are primarily responsible for lubricating the machines. They manage the store room, grease bearings, top-up machines, perform oil changes, make or support decisions to upgrade or change a lubricant specification or reengineer or upgrade lubricant application hardware. They work with lubricant suppliers and lubrication consultants daily to keep things going smoothly. They also manage contamination control efforts by maintaining breathers and filters, using filter carts and other periodic decontamination technologies, etc. Lube techs work closely with mechanics to troubleshoot machine problems that might be lubrication related. Lube techs require a thorough understanding of lube storage and handling, lubrication fundamentals and contamination control.
Lube technicians require several weeks of training to develop a sturdy knowledge base. Additional time is required to train the individual on various procedures with which he will be working. It is not sufficient to rely solely on hands-on training from experienced technicians because a small procedural mistake, often made as a perceived time-saving exercise, can perpetuate and grow into a major flaw in lubrication best practice.
Just like the reliability technician, these individuals will also require frequent booster shots to keep their skills fine-tuned and current.
Mechanics
Mechanics are most intimately familiar with the internal workings and condition of the plant’s machinery. They need sufficient technical knowledge about lubrication fundamentals to spot and accurately diagnose lubrication-induced abnormalities and opportunities to reduce wear through changes in the lubricant type, delivery mechanism or maintenance. If they fail to provide feedback about the effectiveness of the lubrication process, the same problems will recur. They also need to understand the importance of maintaining or restoring cleanliness during repair, and be proficient in procedures for doing so. Because the mechanics are sometimes asked to perform oil changes, they must be trained on those procedures.
Operators
Operators see more of the equipment than anyone in the plant and are typically required to walk-down the equipment every shift. This is a great opportunity to collect simple, inspection-based lubrication information. Beyond the level gauges, the operators should regularly inspect for filter and desiccant condition, evidence of water contamination, foaming and air entrainment, leaks, darkening of the oil, sludge, smoke or fumes exuded from vents, and a host of other easy-to-observe conditions. Operators should be set up with a clipboard, or preferably a digital personal assistant (PDA), that allows them to input inspection information using questions to which they can simply answer yes, no or not applicable. This information must be fed back to the lube technician and reliability analyst so that appropriate corrective action can be taken. The operators must also be trained to perform these functions, with an occasional refresher course to bring their skills and knowledge back up-to-speed.
Managers and Supervisors
While they need only awareness training, management training is typically the most important training in the program, but the most commonly overlooked. Managers make resources available, provide visibility for the program, and must defend it when it comes under fire.
Managers require very little skill-oriented training (sampling procedures for example), but they need some technical knowledge about the various aspects of the program (such as why a representative sample is important to oil analysis effectiveness), and they should have a general knowledge about how good lubrication management creates value (like high particle count in the fluid increases wear - clean oil reduces costs). The emphasis for management is on the financial benefits the program provides, and on aspects of managing the lubrication team.
Managers and supervisors need up to one day of intensive awareness training, along with periodic information updates to keep them fresh and current with regard to new information. Conferences serve as a good knowledge maintenance mechanism for managers. At these events they can discuss lubrication program management issues with their peers, attend benchmarking sessions and become exposed to new products, technologies, services, procedures and best practices.
Based on these job functions and required knowledge and skill base, this plant should implement a planned training program based on the skills-based matrix shown in Figure 1.
Knowledge and Skill Certification
Having selected the appropriate training modules, the question that must be addressed is “How does management know that an individual can perform a particular job?” The answer to this is certification. Certification assures that an individual possesses the knowledge and skills to perform the required tasks.
Knowledge certification is fundamental to success, and is best performed by a third-party entity. A third-party entity is truly objective in that it has no stake in the success of the organization or the individual. Another advantage of third-party certification is its transferability. An organization can hire a person precertified, and individuals can take their certification with them. If no precertified individual is available for a position, certification within a certain time frame can be made a condition of employment.
Third-party certification relieves managers from the requirement of possessing expert knowledge on the topic in order to evaluate an individual’s capabilities. In today’s plants, managers are spread very thin. They can’t be experts on everything. As long as the managers know who the experts are, and where they can be found, they don’t have to be experts themselves. Third-party certifiers offer this ad hoc expertise to managers.
In the lubrication industry, the International Council for Machinery Lubrication (ICML), a nonprofit organization, serves in this capacity by offering multilevel skill certifications for the Machinery Lubrication Technician (MLT), Machinery Lubricant Analyst (MLA) and the Laboratory Lubricant Analyst (LLA). Figure 2 summarizes the skill evaluation objectives for each of ICML’s certifications at two levels.
Going back to the plant example, the required certification for each job function is outlined in Figure 3.
You can’t be world-class at anything if your team isn’t skilled and motivated. Developing machinery lubrication and lubricant analysis skills with occupation-oriented training to build know-ledge, skills and attitudes can go a long way toward ensuring that lubrication best practices are implemented and effective. By certifying individuals, the level of knowledge and skills attained is not only assured, but also a sense of pride and commitment begins to permeate throughout the organization. So get skilled-up, get certified and watch the dramatic transformation!
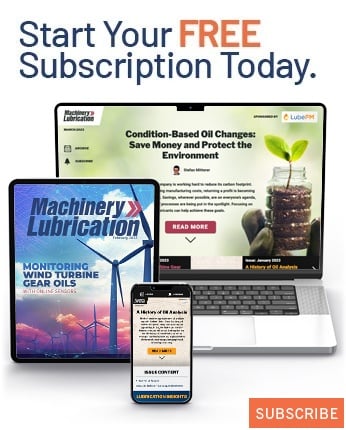