Two years ago, the management team at Nissan saw the need to create a group that would lead the transition of its maintenance teams to a world-class level. At that time, Chad Crane, a reliability supervisor, was selected to join this team.
Joe Welgan, Crane’s manager, sent him for machinery lubrication training, which would be followed by the Machine Lubrication Technician (MLT) Level I exam administered by the International Council for Machinery Lubrication (ICML). While Crane was successful in earning his MLT I certification, the training he obtained was a real eye-opener.
“At the time, I thought I was fairly knowledgeable in the field of lubrication, but quickly realized that I had a lot to learn,” Crane says. “Upon my return, I knew we had a lot of opportunity to improve.”
Nissan’s plant in Smyrna, Tenn., has a footprint of just more than 5.4 million square feet. Crane had only worked in the stamping plant. As a first step, he began riding around with the lubrication technicians as they went about their daily duties.
“I was working side by side with them, learning what they knew and what obstacles they faced each day,” he recalls.
Crane started looking into the plant’s contamination levels as shown in test results from its onsite lab. He sat down with experts in the lubrication field, and together they formed a list of what changes needed to be made. They determined what would make the biggest impact on improving uptime and cutting costs.
Once the items were identified, management was briefed and the decision was made that the recommended changes would be implemented in the stamping plant first before rolling them out to the rest of the facility. The stamping plant was chosen as the pilot because it had the potential for the greatest financial return.
Training and Education
The initial focus at the Nissan plant was on education and training. During the evaluation process, Crane realized that very few technicians had formal training in the lubrication field, so an outside instructor was brought in to provide MLT I training and certification testing. Additional training opportunities, including supplier-sponsored and online training, were also incorporated.
Preventing Lubricant Cross-Contamination
The next step was to address cross-contamination of lubricants, which had been identified as the root cause in past failures. Considering these failures and the challenges the influx of new technicians posed, it was apparent an identification process was needed for proper lubricant selection.
With its new systems in place, the Nissan plant has achieved
a 53-percent reduction in breakdown frequency and
a 54-percent reduction in downtime.
The Nissan team developed a list of all lubricants used in the facility. They worked with their lubricant supplier and vendors to consolidate the list to as few lubricants as possible without jeopardizing the life of the equipment. This process provided several benefits including cost savings, storage space and fewer opportunities for mistakes.
Once the list was finalized, an adhesive tag was placed at every lubrication point to identify which lubricant should be used for each piece of equipment. The team chose a lube code that would supply all the information about the specific lubricant without being brand specific.
This eliminated the need to change out all the tags if there was a supplier change. Each lubricant was assigned its own specific color and shape. Written identification was included to account for color blindness.
Controlling Particle Contamination
The next phase was to address particle contamination. Armed with the knowledge that new oil is not necessarily clean oil, the Nissan team implemented the use of filter carts when filling reservoirs with new oil.
Old breathers were also removed and replaced with a setup that allows quick-connects to be used to hook up filter carts and desiccant breathers. This helped eliminate the chance of contaminants entering the system through the breather port.
The use of sealed top-off containers
with colored tops helps to control particle
contamination and offers another line of
security when identifying the proper
lubricant to be used at the plant.
Another significant step in controlling particle contamination involved the use of top-off containers. The Nissan plant has thousands of small reservoirs and gearboxes that require small top-off containers for refilling.
Sealed containers with colored tops were selected, with colors from the labels matched to offer another line of security when identifying the proper lubricant to be used. Care also had to be taken to not introduce contaminants when filling these containers.
Bulk storage issues were considered as well. Nissan purchased a system that allows oil to be filtered when it is transferred from barrels to large containers. These containers are equipped with a desiccant breather. There is also a clean staging area in which the top-off containers can be filled while minimizing particle contamination exposure.
After a thorough investigation, a kidney-loop system (left) was determined
to be the most cost-effective way to control particle contamination at the plant.
Nissan also purchased a bulk storage system (right) that allows oil to be
filtered when it is transferred from barrels to large containers.
The stamping plant has a unique open-lube system that exposes much of the equipment’s vital parts to particle contamination. After thorough investigation, it was decided that the most cost-effective way to control particle contamination was to use kidney-loop filtration. Due to the large capital investment this represented, the most critical lines were identified to be the recipients of this first wave of systems.
With these systems in place, particle contamination was reduced between 93 to 97 percent, with a resulting downtime reduction of 54 percent. Only 18 months into its five-year plan, Nissan’s program was still in its infancy. However, achieving this type of reduction in downtime ensured management support for implementing the contamination control and improved lubrication practices strategy on all presses with this design.
A New Style of Preventive Maintenance
Grease guns at the stamping plant
have been standardized, and only
two types are now used.
At this early stage in the program, Nissan’s team had already tackled several of its biggest problems and had seen considerable improvement in both uptime and employee morale.
Moving on to focus on other important issues, the team evaluated the plant’s preventive maintenance (PM) and decided to introduce a new style of PM that would offer clear direction as to what was to be inspected, which lubricant to use and how much, as well as provide pictures for easy identification. The key was to engage all the technicians to assist in this process.
When PMs are generated and distributed, the technicians gather all the necessary information from the equipment and write it on the PM. They also add any additional information about the equipment that may not be listed and mark off anything that does not apply.
Calculations are then made to ensure that not only is the lubricant correct but also the quantities and application frequencies. This information along with the pictures are put into the new format and released the next time the PM is performed.
During the PM-optimizing process, Nissan discovered the majority of PMs stated the amount of grease in strokes. Because the plant had several types of grease guns, with each delivering different quantities per stroke, the risk of undergreasing or overgreasing was very high.
Now, all the grease guns have been standardized, and only two types are used. One is a clear-tube grease gun, which is utilized for motor grease and high-speed bearings. The other type is employed for all other applications. Both guns are clearly marked with the proper lubrication tag.
After learning that new oil is not
necessarily clean oil, the Nissan
team implemented the use of filter
carts when filling reservoirs
with new oil.
A grease meter is also used to calibrate each grease gun. How many cubic centimeters the gun distributes is marked on the pump. Each gun is given a specific three-digit number.
A spreadsheet then keeps track of each of the guns so they can be easily identified and routinely calibrated. This decision was made due to the cost of grease meters and the number of grease guns needed in the facility.
Onsite Analysis
Another crucial component of Nissan’s lubrication program is its onsite lab, which has proven its effectiveness in predicting failures and monitoring current equipment conditions. The lab has analyzed and optimized existing routes, and established a schedule for them to be performed on a monthly basis.
If a problem is discovered or a trend changes, the lab can adjust the equipment testing accordingly. This method has been successful in identifying problems and allowing the maintenance groups to plan repairs. With this process, the lab has freed up additional time, which is now used to evaluate new equipment that can be added to the routes.
Tracking Oil Usage
Other tools that have played a key role in improving the Nissan lubrication program include tracking oil usage, documenting procedures, dashboard development and taskforce meetings. Considering the amount of oil being purchased, it was evident that addressing this issue could provide a large cost savings.
In order to track oil usage, a database was created and data entered every time a reservoir was refilled. The type of oil used, amount, equipment number and date are all recorded. This information is then utilized to create charts highlighting the largest consumers and to focus repair efforts in that direction.
Standardization
Documentation of all processes and procedures was critical. Nissan discovered that with thousands of employees, standardization is key to process sustainability. This was essential to the long-term success of the effort, as many employees were promoted or moved to other functions after the successful program. Nissan also incorporated the use of decision trees, which aid technicians in making the right choices at the right time.
To help eliminate the chance of
contaminants entering the system
through the breather port, old
breathers were removed and
replaced with a setup that allows
quick-connects to be used to hook up
filter carts and desiccant breathers.
Another goal in the process was to create a manual that included all of these items. The challenge was making the manual widely accessible. The solution was to develop a dashboard, which is simply a page full of hyperlinks for technicians to access all the information they need. The dashboard not only enables new items to be added easily but also allows everyone to have immediate access to it.
The utilization of the dashboard played a significant role in the monthly lubrication taskforce meetings, which were designed to help communicate the status of the program. These meetings were expanded to include technicians and have proven to be invaluable for obtaining new ideas, expressing concerns with any changes, sharing information and, more importantly, building trust between the technicians and management.
Management Support
Having the support of technicians and management has been critical in Nissan’s success. Crane credits Welgan and his director, Brian Sullivan, for believing in him and supporting him throughout the implementation process. He also praises the efforts of technician Donald Myers.
“T.K. Brewer and I put him in a position to help promote the standardization of the program when we began to roll it out plant-wide,” Crane says of Myers. “Without his help, none of this would be where it is today.”
Nissan’s plant in Smyrna, Tenn., has a footprint of just more than 5.4 million square feet.
Although the program at Nissan is still very young, its strong roots in education, unquestionable management support for sustainability, standardization of procedures based on best practices, trending of critical metrics, use of information technology and commitment to continuous improvement have captured the attention of ICML.
The vendor-neutral organization recently presented its John R. Battle Award to the Nissan plant for excellence in the application of machinery lubrication.
“We are very excited and very proud to be selected as the recipients of this award,” Crane said. “When we started this journey, this was very much one of our goals, but we thought it would take us five years to get here. To accomplish this feat in just two years shows how strong of a team we have here.”
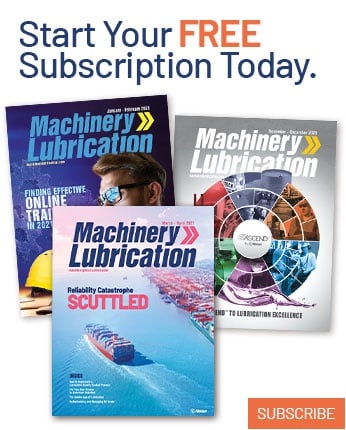