If you have ever worked in or around a paper facility, you might be familiar with the steam, smell, pulp, and water that seem to be everywhere. As you can imagine, contamination control is extremely important for the equipment's reliability. So, focusing on reliability and contamination control will have a direct impact on production. And if you weren't aware, the folks on the carpet are really interested in that production stuff.
So, what can we do to ensure that we get as much of that coveted production as possible? First, we need to understand what is getting into our machines and what it does to them.
Understanding Contamination Sources
In the bustling corridors of a paper mill, contaminants lurk around every corner, ready to wreak havoc on our lubricants and equipment. From airborne dust to moisture infiltration, these silent saboteurs can spell trouble for our machinery's longevity and efficiency. With a keen eye and strategic planning, we can identify these troublemakers and implement measures to keep them at bay. So, let's focus on some of the most common contaminants we face in paper production.
Moisture Management Strategies
Moisture is part of the process, so we can't eliminate it from the working environment, but we can try our best to prevent it from coming into contact with the internals of our equipment. Both reservoirs (gearboxes and hydraulics) and bearings are very susceptible to damage from moisture. Water gets into these locations, and it starts to rust the equipment, break down the lubricants, sacrifice the lubricating film, and can even lead to bacterial growth within our equipment. For reservoirs, mitigating water ingression doesn't have to be really difficult. We have to look at how the water gets in there, how to judge when water is in there, and how we get it out. I'll save the last part of that, getting it out, for a little later.
How do we keep it out? All of these reservoirs need to breathe in some way or another. OEMs give us these wonderful breathers and fill caps that do nothing. How about we look at the equipment's needs and the environment they are in and do something about it? Those fantastic breathers that these OEMs slap on there, why not replace them with something that actually works? How do we know what will work?
Let's look at how much our equipment needs to breathe, for starters.
Innovations in Equipment Breathing
If I have something that needs to breathe a lot, I will likely look at desiccant breathers. These things work great. They are tried and true. There are some drawbacks to them, though. They are consumable and need to be inspected regularly to ensure that they can still breathe for one, and we need to make sure that we change them out as soon as, or just before, the desiccant is spent. Now, there are some breathers better equipped than others, like some that have check valves (this way, the air traveling through the breather only gets dried and cleaned as it goes into the reservoir). Others might be equipped with washdown caps, which is fantastic for anything within a washdown area or where water spray is often nearby. Some might be outfitted with both of these features!
But what if I have a little pump or gearbox, you might ask? Well, those things don't typically require a large amount of breathing to work properly. So why don't we put something on those that might last longer? Expansion chambers are an excellent alternative for desiccant breathers in this case. They are a straightforward contraption (essentially two cups pushed up against one another and a diaphragm in between them. The diaphragm rises when the little pump or gearbox needs to breathe out. When it needs to breathe in, the diaphragm lowers. It turns that little piece of equipment into a closed system, keeping moisture and dirt out. Although these little things are great, they still need to be inspected. That diaphragm can rupture over time. This is, once again, where quality components are essential. I suggest looking for expansion chambers with a built-in indicator for if the diaphragm ruptures.

Enhancing Hydraulic Systems
Hydraulic quick connects are another great way of preventing moisture and dirt from getting into your equipment. These versatile devices are the linchpin of efficient lubrication management. By enabling a constantly closed system, they help to offer seamless execution of maintenance tasks and quick connects to streamline operational processes, too. Their intuitive design minimizes the risk of contamination during lubricant transfer, ensuring that oils maintain their optimal condition.
I know we have all seen and used hydraulic quick connects at some point, but to take your game to the next level with these, I recommend switching to color-coded quick connects. This makes it a no-brainer when it comes to putting lubricant into a piece of equipment. It helps to take the guesswork out of things and ensures that we don't have anyone accidentally cross-contaminating the oils. This can especially help out if the paper products being made require food-grade lubricants in some of the applications.
Real-Time Monitoring of Contaminants
So, how can we tell when contaminants have passed my other safeguards? Of course, there are laboratory and field tests, but we need to know ASAP when bad stuff is trying to do bad things inside our equipment. I am a massive fan of 3D bullseye sight glasses for anything that might have come with a 2D sight glass or even a level plug. Bullseye sight glasses provide invaluable insights into lubricant condition and contamination. These simple products empower maintenance professionals to confidently make informed decisions by visually assessing lubricant clarity, turbidity, and even "milkiness." A good columnar sight glass will be my go-to item if I have a larger reservoir that needs a good, clear indication of lubricant level and condition. These won't show some stuff really well, like foam in a reservoir (unless it is REALLY bad), but they are invaluable for any reservoir with an oil level that changes while it is in use.
Wouldn't seeing water in a system before you get an emulsion be nice? It might even pay off to have something like a little bowl attached to the bottom of a reservoir that could show you free water and even sediment, like wear metals. Well, so I have news for you! Bottom sediment and water bowls already exist, and they are fantastic. When positioned at the lowest point of equipment reservoirs, these unassuming vessels play a crucial role in contamination control. Since they live on the bottom of a sump, they will catch water when it gets into your system. It also catches the heavy wear metals and even offers a place to drain moisture with a little petcock valve. Regular maintenance and periodic draining of accumulated debris ensure that lubricants remain free from impurities, safeguarding equipment from premature wear and damage.
The Critical Importance of Filtration
So what do we do after discovering that we have all of this stuff in our equipment that we shouldn't have? Filtration. From offline kidney loop filters to in-line filtration units, filtration systems are the frontline defense against particulate contamination and moisture in lubrication systems. By actively removing debris and moisture from our oils, these mechanisms mitigate the risk of equipment failure due to contamination-related issues.
Incorporating advanced filtration technologies into maintenance routines ensures that lubricants remain pristine and conducive to optimal equipment performance. And we have so many filtration options to choose from. Many people opt for filter carts, which are an excellent investment because they are versatile. Filter carts can be used as portable parts washers for filtering equipment that is in use; we can even use them to filter new oils as they come on-site. However, something that I have seen over the years is people buying filter carts and thinking that they have solved all of their problems. That is NOT the case.
These things are just tools, and if we don't know how to use them correctly or even what our specific goals are, we are as lost as having a whisk in our toolbox just because "well, it's a tool." We have to set cleanliness goals, which is something to shoot for — and not just cleanliness; we need dryness goals as well. We have to start making informed decisions about how we plan on extending the life of our equipment. Only then can we devise a plan and implement it in a way that can make an impactful difference.
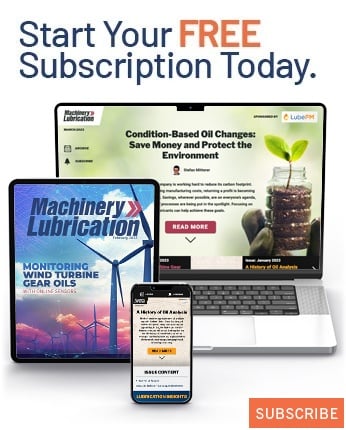