Name: Mike McLagan
Age: 45
Title: Plant Reliability Machinery Lubrication Technician
Years of Service: 19 years
Company: Peabody Energy’s North Antelope Rochelle Mine (NARM)
Location: Wright, Wyo.
Contamination control can be challenging for any coal mine. As the largest coal producer in North America, Peabody Energy’s North Antelope Rochelle Mine (NARM) in Wright, Wyo., has learned the importance of oil cleanliness. Lubrication technician Mike McLagan has worked for the company for 19 years and has seen the improvements that have been made to assure lubrication effectiveness with oil analysis and filter analysis. The results have been increased machine availability and reduced costs.
Q What types of training have you taken to get to your current position?
A A solid foundation for an effective lubrication program has been built with Noria skills training in the introduction to machinery lubrication and practical oil analysis courses. Advanced training in failure analysis and root cause analysis has also been completed.
Q What professional certifications have you attained?
A My certifications include Machine Lubricant Analyst (MLA) Level I and II through the International Council for Machinery Lubrication (ICML). I am also certified as a facilitator analyst and as a Wyoming surface coal foreman.
Q Are you planning to obtain additional training or achieve higher certifications?
A Upcoming certifications within the next 12 months include MLA Level III and Certified Lubrication Specialist (CLS).
Q What’s a normal work day like for you?
A My day begins with a safety/startup meeting. With information from this meeting, I will schedule oil changes according to available downtime. Then I check the oil and filter inventories in our lube building and restock accordingly. From there, I make my plant rounds to monitor and record the filter differential pressures, replace filters based on the information obtained from the differential pressures/oil analysis results, and check breathers and seals on the most critical gearboxes. I finish my day at our in-house oil analysis lab to review incoming oil and filter samples from the previous week. I also label and prepare current oil samples for shipment to the oil analysis lab in Spokane, Wash.
Q What is the amount and range of equipment that you help service through lubrication/oil analysis tasks?
A Our plant consists of 14 miles of conveyors transporting coal from our five crushing facilities to five silos, 45,000-ton slot storage and three train load-out stations. Keeping all of this conveyor belt moving requires several large gearboxes driven by 1,500-horsepower electric motors, 18 separate hydraulic systems, 11 large air compressors, 18 holdbacks and hundreds of individual bearings on automatic lubrication systems.
Q What lubrication-related projects are you currently working on?
A I am currently designing an air-driven kidney-loop system to filter and cool small reservoirs of oil (1 gallon or less) to prolong the service life of the holdbacks attached to our main conveyors.
Q What have been some of the biggest project successes in which you’ve played a part?
A By implementing a kidney-loop system on our large 90-gallon-reservoir gearboxes, we have been able to take our ISO codes from 24/23/17 to 17/13/11 in the gear oil we use. We also had our new lube building featured in Machinery Lubrication’s 2013 Lube Room Challenge.
Q What do you see as some of the more important trends taking place in the lubrication and oil analysis field?
A Companies are seeing the importance of having certified people in critical roles. Certified world-class analysts equal world-class reliability.
Q What has made your company decide to put more emphasis on machinery lubrication?
A A phenomenal amount of money is lost each year due to friction and wear, which can be offset through training in proper machinery lubrication and oil analysis as the guide to a world-class lubrication program.
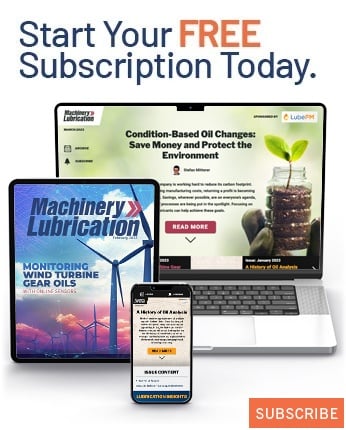