"Is there any way to clean our oil up to two ISO codes other than with loop filtering?"
Best practices recommend that lubricants are filtered when they are transferred from one container to another or to a machine. This practice can improve lubricant cleanliness with just a single pass. The filter must have a high beta ratio (greater than 200) at the right micron size to achieve the expected cleanliness level. Of course, the use of a high-efficiency filter will require the proper lubricant flow rate and pressure according to the viscosity and volume to be filtered.
Installing a temporary online filtration system or “kidney loop” to clean the lubricant in a machine or container is a low-cost option to remove solid contaminants. Since the filtered lubricant returns to the same sump from which it was obtained, it is mixed with non-filtered lubricant. The new sump cleanliness is the result of the mixed concentrations. For this reason, the lubricant must pass through the filter several times. The number of passes will depend on the existing and desired cleanliness level. The lubricant volume will play a factor as well. In the field, it is common to have a lubricant pass through the filter seven times to clean it, but this is just an estimate.
Other alternatives can also be employed to clean the oil, including modern centrifugal technologies. These can be very effective in removing solid contaminants and improving ISO cleanliness codes. They are used for industrial engine oils and frequently applied as a bypass system for the main filtration and lubrication circuit.
Most centrifuge designs utilize the pressure of the fluid going through the system to spin the rotor at speeds high enough to separate contaminant particles from the fluid. In engine applications, the oil is directed to the centrifuge in a bypass loop, which uses from 5 to 15 percent of the pump’s flow, depending on the application. This pressurized flow travels through the centrifuge rotor. As it exits the rotor, the oil goes through two small nozzles. The reaction force created by the exiting fluid creates the torque necessary to overcome any friction, and the rotor begins to spin. Typical speeds between 5,000 and 8,000 revolutions per minute can be achieved in most applications.
Other methods such as gravity settling or magnetic filters may not be as effective in removing smaller particles or different materials.
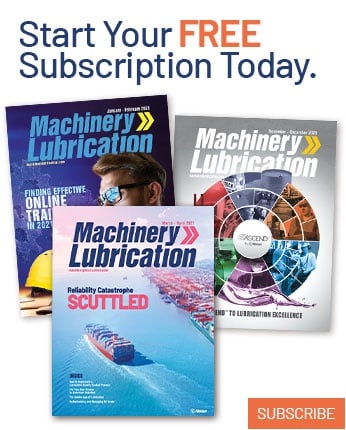