What lubricates more efficiently, oil or grease? More than 95 percent of all components are lubricated with oil, not because it lubricates better but because it has a wider variety of properties.
Grease generally is used only if oils cannot be utilized because sealing the lubrication point is problematic or expensive. Typically, grease is applied on rolling bearings, with nearly 80 percent of these bearings lubricated with grease.
During analysis, oils and grease behave similarly. Although both contain important information, it is more difficult to interpret the results for grease. The following methods represent the most important ways to analyze lubricating grease.
Atomic Emission Spectroscopy
Atomic emission spectroscopy (AES) by the Rotrode method can be used to provide information about wear, impurities, thickeners and additive levels in a grease sample. Increased iron and chromium values may indicate that a rolling bearing has been subject to wear, while copper, lead and tin show corrosion or abrasive wear from bearing cages.
Possible impurities such as silicon (dust), calcium (lime) or hard-water deposits help to identify the causes of wear. Deviations between fresh and used grease in terms of the content and composition of the additive package or the thickener reveal that another grease is being used.
Particle Quantifier Index
The particle quantifier (PQ) index specializes in determining magnetizable iron particles. Unlike AES, which cannot easily detect iron particles greater than 5 microns, the PQ index records all the wear particles that are magnetizable regardless of their size. The height of the PQ index is then measured in conjunction with the AES iron content.
How FTIR works
An extreme PQ index (more than 500) indicates that acute wear has taken place regardless of the AES iron values. Often there has been pitting or material fatigue. A high PQ level (more than 200) with a low AES iron value (less than 100) signifies that acute wear is occurring and causing relatively large wear particles.
An increased PQ index (more than 100) in combination with a correspondingly high AES iron value is a sign of typical material fatigue during which “normal” wear occurs. A low PQ index (less than 50) accompanied by a high AES iron value (more than 100) is always a sign of corrosion and rust formation. Rust is barely magnetizable, so it produces a low PQ index.
Fourier Transform Infrared Spectroscopy
The principle of Fourier transform infrared (FTIR) spectroscopy is based on there being molecules present in a lubricant that absorb infrared light to different degrees because of their chemical structure. Changes to the used lubricant can be compared to the fresh grease reference spectrum and then depicted, calculated and interpreted as typical “peaks” for certain wave numbers.
In addition to identity controls, oxidation can also be proven with FTIR spectroscopy, for instance. As they age, molecular compounds alter and absorb more infrared light than fresh grease. Through the process of Fourier transformation, these values can be read and the molecular vibrations represented in an FTIR diagram.
Depending on the molecular compounds, the peaks develop as corresponding wave numbers. Synthetic lubricants frequently contain ester-based components. Because of the oxygen molecules contained within them, they absorb infrared light in almost the same wavelength range as the double oxygen bonds that arise through oxidation. This is why oxidative changes to a synthetic oil cannot be calculated accurately using FTIR alone. The RULER test is needed for this.
Through comparison with the deposited fresh grease spectra, the process provides quick and reliable information on whether greases have been mixed together or a completely different type of grease has been used. The process can also determine whether the grease contains a base oil that is synthetic or mineral oil based.
For base oils that are mineral oil based, FTIR establishes whether oxidation has taken place because of a lack of relubrication or because of damage caused by high temperatures. If the grease contains high-pressure additives, additive deterioration may be detected. A fresh grease comparison can also prove whether there is too much water.
Karl Fischer Titration
Too much water in grease may cause corrosion and bearing damage. In places with high relative movement, cavitation can occur. If too much water is present or water penetrates continuously, relubrication must be performed more frequently. If the grease cannot withstand water, it may become soft or watery, and the quality will decrease.
Karl Fischer titrator (Ref. Hanna Instruments)
Just as with oil, the amount of water in a grease sample is calculated using the Karl Fischer (KF) method. It requires that water is “driven out” of the sample. With oil, the water from the sealed sample is steamed away by heating it to temperatures of up to 140 degrees C. However, it is much more difficult to boil water out of grease.
In this case, the water must be extracted slowly at a temperature of 120 degrees C. The water is channeled into a titration vessel using a hollow needle and nitrogen. An electrochemical reaction then takes place with a special KF solution. Once the transition point of the titration curve has been reached, the exact water content can be stated in parts per million.
If a grease contains too much water, it is important to find the origin and eliminate it. The Karl Fischer method provides quantitative information about water content. The elements investigated by atomic emission spectroscopy help to distinguish between condensate and tap water.
If the used grease sample is unlike the fresh grease sample and is polluted with sodium, calcium, potassium or magnesium, this points to “hard” water, which may have penetrated the grease during high-pressure cleaning. If these minerals are not present, it may be “soft” rain or condensed water.
If water was not removed effectively during the production of the grease, it may be found in the fresh grease sample. An analysis of fresh and used grease will clarify this matter.
Bleeding Test
The sponge-like structure of the thickener or soap used in grease holds the base oil firm and allows it to transfer slowly to the lubrication point. However, if the oil flows too quickly and uncontrollably from the thickener, the grease “bleeds” away. If the remaining thickener contains too little oil for the lubrication tasks, the remaining grease dries out. If the residual oil content of a grease falls too quickly, either the grease is unsuitable or must be reapplied more frequently or in larger quantities.
Determining the residual oil content provides the necessary information to decide which is the case. This test shows the percentage of base oil that the soap structure has lost over the course of six hours at a temperature of 60 degrees C. The residual oil content of used grease should then be compared with the fresh grease sample.
If the values are between 5 and 25 percent, and the difference between the used and fresh grease is plus or minus 15 percent or less, the grease can still be used without changing the relubrication intervals.
If the used grease loses considerably more oil than the fresh oil, the thickener is no longer able to maintain the base oil in its sponge-like structure. If significantly less oil is released from the used grease, it has already begun to dry out. The bearing surface is “hungry” for lubrication and must be lubricated again.
Residual oil content levels that are too low may be the result of too much time in use and insufficient relubrication; strong vibrations, loads or rotation speeds; mixing of greases that have been saponified differently; impurities caused by water, acids or lyes; inadequate temperature resistance; or oxidation and aging (acetifying) of the base oil.
Measuring grease consistency with a cone penetrometer
Penetration Test
While viscosity describes the ability of a lubricating oil or hydraulic fluid to flow, consistency refers to the extent to which a lubricating oil is stiff. However, the consistency of a grease is not directly linked to the viscosity of its base oil or the kind of thickener used.
The National Lubricating Grease Institute (NLGI) divides lubricating greases into classification groups based on their consistency. Along with the base oil’s type and viscosity, the consistency category to which it belongs provides another important value to classify the firmness of the grease. The consistency shows whether the grease is feedable or has become too firm as a result of bleeding.
Consistency is measured using a standardized cone. Grease is spread into a small pot. The tip of the cone touches the grease. The penetration depth is reached in 5 seconds and measured in 0.1 millimeters. This produces the grease penetration number used to determine the NLGI class. The softer the grease, the deeper the cone penetrates. This indicates a high penetration number and a low NLGI class.
Comparing fresh and used grease penetration allows certain conclusions to be drawn. For example, if the used grease has become softer and therefore has a higher penetration number than the fresh grease, it may have mixed with another grease or been contaminated by water or another liquid. The grease may also have been mechanically sheared and loaded.
A significant drop in the penetration number indicates that the grease may have been bled by excessively strong vibrations or that high temperatures may have resulted in oil separation. High levels of pressure in the central lubrication system may have also disturbed the balance between the base oil and the thickener.
The National Lubricating Grease Institute (NLGI)
divides greases into classification
groups based on their consistency.
Sulfate Ash
Investigating sulfate ash is a process used to identify inorganic levels in organic samples. This is achieved by heating the sample to temperatures of 775 degrees C. At this temperature, the organic elements in the samples “combust.”
All that remains are ashes consisting of metallic oxides (soap, additives, etc.) and impurities. By smoking this with concentrated sulfuric acid, the oxides in the ashes are transformed into sulfates. The weight of the remains is then recorded.
If the proportion of sulfate ashes in the used grease has increased in comparison to the fresh grease, this is a clear indication of impurities and/or wear. If the metal values established by AES are consulted at this stage, the cause of the weight increase can be clarified. High levels of iron and chromium point to wear, while increased proportions of silicon and calcium hint at impurities.
The weight of the sulfate ash is affected by metallic abrasion from bearing wear, hard impurities such as silicon (dust), levels of solid lubricants like molybdenum disulfide, metal organic extreme-pressure additives, and other metal soaps and inorganic thickeners from other greases with which they have mixed.
Shear Stress, Visible Viscosity
A rheometer is used to measure a grease’s visible viscosity at different temperatures. For this purpose, a small amount of grease is placed on a temperature-controlled plate. The plate-based testing cone, which develops a gap between the upper and the lower plates, moves onto the film of grease. The force between the plates and the cone is measured as dynamic viscosity, which for grease is also called “shear viscosity.”
The stability after the shearing, which assesses characteristics such as a grease’s deformability, can be described in terms of apparent viscosity. The rheometer provides the shear viscosity at the beginning and end of the testing procedure and displays the shear viscosity decrease in terms of percentage.
By using the index and comparing with different fresh greases or through trend analyses, you can determine the lower temperature limit at which the grease can be used, whether the grease is suitable for high rotation speeds and whether it is acceptable for specific types of bearings.
Dropping Point
As temperatures rise, greases behave differently than edible fats. They do not melt like butter or coconut oil when warmed but hardly change at all as the temperature rises because the thickener holds the base oil firm. Only when the thickener’s critical temperature has been reached does the soap structure dissolve.
To establish the dropping point, a grease sample is warmed in the testing device until liquid drops fall to the bottom of the test tube through an opening in a nipple. Gel- or powder-based greases, which are measured at temperatures of more than 300 degrees C, are considered as not having a dropping point.
Establishing a grease’s dropping point
There will not always be a correlation between a grease’s dropping point and its maximum operating temperature. Of course, the permissible temperature is always less than the dropping point value. Along with the thickener, the oil type will dictate a grease’s maximum operating temperature.
A lower dropping point of a used grease in comparison to a fresh grease may be caused by greases with different thickeners mixing together, the grease containing water or other foreign fluids, or the grease shearing into small particles under extreme loads.
Linear Sweep Voltammetry
Linear sweep voltammetry, which is also known as the RULER test, establishes the amount of amino and phenol oxidation inhibitors in a grease sample. Because lubricating greases are affected by factors such as time and temperature, they usually contain antioxidants along with extreme-pressure and anti-wear additives. These additives can break down. Therefore, the relubrication intervals and amounts must be adapted to the decreasing additive levels.
Infrared spectroscopy can identify the development of oxidation in mineral-oil-based greases but not for synthetic base oils. The RULER test is used for these types of greases. By comparing the curves of fresh and used greases, the remaining lifespan of a grease can be determined as well as the best time for the next relubrication.
Soxhlet Extraction
Since base oil viscosity is a key factor in calculating bearing lifespans, most grease manufacturers provide this essential information about the base oil. However, no regulations currently exist regarding this issue. Generally, high viscosity is considered better.
In order to demonstrate high viscosity, all of a fluid’s components including the oil, additives and viscosity index (VI) improvers must be mixed. The viscosity is stated based on this mixture. This viscosity value has little in common with the way viscosity is calculated for oil used in roller bearings because the grease no longer releases some parts of the thickener onto the bearing track.
A Soxhlet extractor can separate the liquid grease component from the thickener. Oil that is extracted in this process only contains liquid components. Polymer or adhesive supplements, VI improvers and even solid lubricants remain in the thickener.
After the oil-based components have been extracted from the soap, information can be provided about the grease’s oil and thickener levels. Separating the components into solids and oil makes it possible to carry out a detailed analysis of the base oil with respect to its viscosity, composition and proportion of additives.
Neutralization Number
Even greases can turn “sour.” Oxidation of the base oil, breakdown of anti-wear additives or entry of salted fluids will result in the development of acids in the grease. These acids can destroy alkaline thickeners, causing the grease to have a soup-like consistency and the base oil and soap residue to separate. The grease then will run off the bearing surface, and bearing failure may occur.
Various reactions can lead to the fat becoming acidic. When this happens, relubrication should take place at more regular intervals.
The neutralization number can help determine when a grease is not suitable for use and if the base oil or thickener should be improved.
Water Resistance
Although it is easier to seal lubrication points with grease than with oil, grease should be resistant to water. Hydrophobic grease will provide a seal against splash water. If a grease can emulsify water, there is a risk of corrosion and hydrogen embrittlement.
A simple test for water resistance involves placing a thin layer of grease on a strip of glass. If the layer of grease turns a cloudy, milky color or dissolves from the glass strip entirely, the grease will absorb moisture when stored in water. If water runs off the layer of grease, the grease can be considered water-resistant.
Copper Corrosion
For this test, a copper strip is covered with grease on all sides and placed in a specimen container with the same grease. The sealed sample container is stored for a certain amount of time in a warming bath. After the test period, the copper strip is removed, cleaned with solvent and carefully dried. The level of corrosion is established by using a color scale to compare the copper strip’s discoloration.
This technique is utilized to investigate a grease’s corrosive characteristics in the presence of copper, as the sulfur level alone does not provide enough information on the expected corrosion of metallic machine parts. The test can reveal whether the additives that are supposed to reduce the effect of sulfur compounds still work and how the grease will behave in terms of non-ferrous metal corrosion when used in bearing cages.
Of course, all of these methods will depend on the ability to obtain a representative grease sample. Without this essential element, qualified grease analysis and a reliable diagnosis will be impossible.
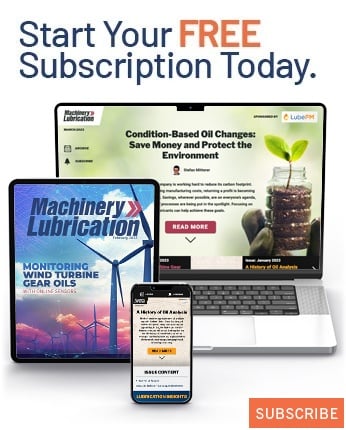