It has been proven that the No. 1 cause of machine failure is the degradation of component surfaces. These surfaces can degrade in a variety of ways, but the most destructive is via particle contamination. While you may already be aware that dirt is harder than most metals found in machines, do you know how much harder it is?
Before analyzing the differences in the hardness of materials, you must first understand how hardness is measured. A quick Internet search for hardness measurements likely would yield three general methods: Rockwell hardness, Vickers hardness and Mohs hardness. Although each of these tests is a little different, they all measure a material’s strength by indenting or scratching.
86% | of lubrication professionals say particle ingression has caused problems for their plant’s equipment, based on a recent survey at MachineryLubrication.com |
Rockwell Hardness
The Rockwell hardness test method has several scales that are based on the tester’s indenting tip. However, they all work similarly. A load is applied to the indenter, which then transfers the load to the material being tested. At the conclusion of the test, the indention depth is measured. Most metals are tested using the “C” scale, which employs a diamond tip to aid in the indenting process. The higher the number in the Rockwell scale, the harder the substance.
Vickers Hardness
Like the Rockwell scale, the Vickers hardness test uses a diamond tip and relies on indenting a surface to measure how hard it is. The higher the value, the harder the material. However, the measurement is a little different. While the Rockwell scale measures the indention depth, the Vickers test involves locating the indention and comparing it with the force required to achieve it. Once this ratio is determined, you are left with a measurement of the material’s hardness.
Particles of high compressive strength (hardness) and angularity (sharp edges) cause the greatest damage.
Mohs Hardness
The Mohs hardness scale is a much older method used primarily by jewelers and those who are concerned with minerals. It was based on a scale of 1 to 10, with diamond being at the top (the 10 value). Materials were tested against each other, and if one scratched the other, it would be given a higher value. For instance, gypsum can scratch talc; therefore, gypsum would have a higher Mohs value than talc. Since diamond scratches everything, it was given the highest value.
The Mohs scale is easy to interpret, but it lacks the certainty of the other tests. The difference between a 5 and a 6 on the Mohs scale cannot truly be determined, whereas the hardness differences on the Rockwell and Vickers scales are much more tangible.
Applications
Most bearings are created using a type of chrome steel. Although there are many variations of this material, the majority come in at approximately 60 on the Rockwell hardness scale (848 on the Vickers hardness scale).
In contrast, quartz has a Vickers hardness of approximately 1,200 (7 on the Mohs scale), which is roughly 1.5 times harder than chrome steel. Quartz was chosen for comparison because it is one of the most abundant minerals in soil (primarily sand).
Silica-dioxide crystals are commonly referred to as quartz and can be found in most soils. Soils can vary from region to region, with some more abrasive than others. For example, the soil around my house in Oklahoma is classified as clay loam.
This is a common soil type that has a blend of different levels of sand, clay, silt, etc. While other minerals in dirt can be abrasive, it is the silica that cuts the most. In areas with high concentrations of sand in the soil, it is important that machines susceptible to dirt ingression are outfitted with devices to prevent these particles from getting inside the equipment.
Hopefully, you now have a better understanding of just how much harder dirt is than bearing and gear surfaces. Considering that steel has a Mohs value of only 4.5, the old adage “tougher than nails” doesn’t sound quite as impressive and perhaps should be changed to “tougher than dirt.”
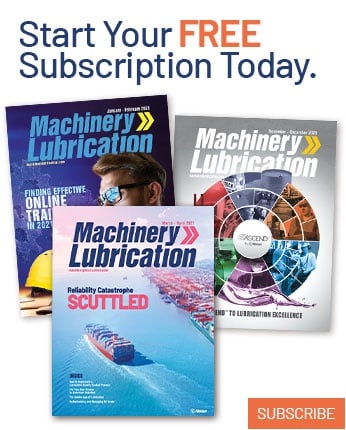