"Can you offer any advice on selecting desiccant breathers for gearboxes? Which factor plays more of a role in breather selection: the sump headspace above the oil level, ambient conditions like high humidity or a dusty environment, the machine type (mobile unit or fixed installation), the type of oil and its application, or the oil’s cleanliness requirement?"
Desiccant breathers are great accessories for lubricant contamination control in machines that would otherwise be breathing dirty, wet air.
These devices allow for the air being ingressed by the machine to be cleaned of particulate matter and also dried to help control the amount of water in the oil. This becomes very important in critical machinery as well as those that are in harsh environments where the oil may become contaminated and break down quickly.
These breathers have a particulate filter phase and a moisture absorption phase. Both of these phases are essential not only for the health of the lubricant but also for the health of the machinery. Solid particulate contaminants can lead to machinery failure mechanisms such as three-body abrasive wear. Moisture contamination can result in adhesive failure mechanisms and increase the rate at which lubricants break down.
Oil by nature is hygroscopic, which means it will absorb moisture readily from any source, including from humidity in the air. By utilizing a desiccant breather, you can reduce the amount of moisture in the air that is entering the system.
The headspace is important to keep in mind, as it can help determine the amount of “breathing” that will occur inside the machine. Therefore, it is imperative to understand how much the headspace can fluctuate. For instance, the headspace in a splash-lubricated gearbox will fluctuate less than that of a hydraulic system reservoir where there are large volumetric changes within the sump. This volumetric flow rate must be within the breather’s capabilities, or it may cause a vacuum or pressurization condition inside the component.
The environment in which the machine operates should be considered as well. For severe environments, such as those with water spray and large amounts of dirt, select a desiccant breather that can handle the expected amounts of contamination. You may also be able to position the breather to better protection by adding a length of pipe or porting the breather to put it out of the way of water spray or steam. For the most severe environments, you might choose a breather with a check valve or quick exhaust manifold to help prolong the desiccant’s life.
The cleanliness level required by the machine must also be taken into account when determining the desired desiccant quality. Of course, the more critical machines should receive the most attention.
Considering all of these variables will provide the most effective way to select a desiccant breather. While a number of options are available, getting the most value out of your breather comes down to understanding or controlling variables associated with breather life.
These three primary variables have the biggest impact:
- Frequency and volume of air intake
- Amount of silica gel in the breather
- Humidity of the work environment
Remember, it is far better to provide more protection than needed rather than to skimp on quality in order to save money. But ultimately, you want to be sure you are getting the full value from your breather spend. Again, the support of a good supplier is key.Talk to your supplier about the specifics of your application and lubricant storage. Some may be able to suggest more holistic solutions that bring in oil filtration or other tools to help you get the most value possible from your breather spend.
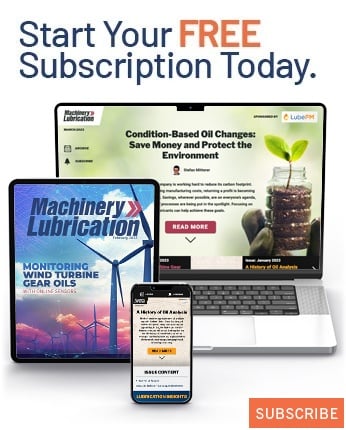