Anyone in the maintenance field who has repaired a pump or gearbox knows the one component that always seems to get replaced during a rebuild is the lip seal. It usually is damaged when being extracted or during disassembly. Perhaps the lip seal is the reason the piece of equipment was pulled from service due to leakage. Regardless, the fact remains that lip seals are vital machine components. They keep oil or grease in and help keep contaminants out. Lip seals seem to be on almost every piece of plant equipment, so why not take the time to learn how to correctly select and install them.
70% | of lubrication professionals say their plant uses lip seals to control contaminant ingression, based on a recent survey at MachineryLubrication.com |
Purpose of Lip Seals
The primary purpose of a lip seal is to exclude contaminants while retaining lubricants. By nature, lip seals function by maintaining friction. They can be used in a variety of applications from slow-moving equipment to high-speed rotation and in temperatures from below freezing to more than 500 degrees F.
To be effective, a lip seal must maintain proper contact with its rotating counterpart. This will be influenced by proper selection, installation and care of the seal once it is installed. I’ve often seen a new lip seal start to leak as soon as it was put into service. This typically is due to improper installation. Other seals will leak initially but then stop leaking once the seal material has seated to the shaft.
Selecting a Lip Seal
Maintaining functional lip seals begins with the selection process. When choosing a material, you must consider the operating temperature, the lubricant in use and the application. The most common lip seal material is nitrile (Buna-N). This material functions well at temperatures of minus 40 degrees F up to 275 degrees F. Nitrile lip seals cover most applications in industry from new equipment to replacement seals. They have excellent resistance to petroleum oils, water and hydraulic oils, but what really sets these seals apart is their low cost.
Another affordable option is Viton. Its temperature range is minus 40 degrees F to 400 degrees F, depending on the specific compound. Viton seals provide good resistance to petroleum oils and can be employed with gasoline and transmission fluid.
Other seal materials that can be used with petroleum oils include Aflas, Simiriz, carboxilated nitrile, fluorosilicone, highly saturated nitrile (HSN), polyurethane, polyacrylate, FEP and silicone. All of these materials have specific applications and precise temperature ranges. Be sure to take into account the process and environment before selecting a seal material or making a switch, as the correct material can prevent a costly failure.
Lip Seal Construction
Once the seal material has been selected, the next step is to consider the seal’s construction. In the past, a simple lip seal consisted of a leather strap on a wheel axle. Today’s lip seals have multiple parts that affect how the seal performs. There are various contacting patterns as well as non-spring and spring-loaded seals. A non-spring seal generally will be less expensive and be able to retain viscous materials like grease at slow shaft speeds. Typical applications include conveyors, vehicle wheels and greased components. Spring-loaded seals are typically used with oils and can be found on a wide range of equipment.
Lip Seal Installation Checklist
- The elastomer is not damaged (no nicks, scratches, cuts, etc.)
- The case is not damaged (no nicks, cuts, dents, etc.)
- The garter spring is properly placed (if used)
- Wipe the seal and shaft of any debris
- The assembly lube is compatible with the lubricant in operation
- The case is of the proper specification
- The elastomer is of the proper specification
- The lip seal is pointing in the correct direction
- The shaft is free of defects (no nicks, scratches, grooves, etc.)
- The bore is free of defects (no nicks, debris, roundness, etc.)
- There is adequate ventilation of equipment when stored or in operation
- Proper installation tools are used to avoid damaging seals
- Equal pressure is applied during installation to ensure the seal is not cocked
Installation
After the seal material and construction have been chosen, the lip seal must be installed correctly for it to perform. There are a number of products on the market dedicated to this single task. Most look like a socket set that will position the seal squarely into its bore. These tools can work well if selected carefully, but most off-the-shelf versions aren’t as effective, especially when a shaft is already installed.
For these instances, I prefer to use a pipe that is large enough to slip over the shaft and makes good contact with the lip seal’s outer shell. If you can find something that catches the outer casing, you can prevent damaging the inner metal ring that attaches to the lip seal material. Just be sure to set the seal in straight and at the correct depth. Failure to properly set the seal perpendicular to the shaft can cause immediate leakage.
If you have a used shaft, it likely has developed a wear ring where the old lip seal was placed. You should never set the contact patch to a previous contact point. If this is unavoidable, there are products that you can slip over the shaft to help with the damaged surfaces. This is usually quicker and more cost effective than replacing a shaft. Keep in mind that the lip seal will need to be resized for the added sleeve.
When installing lip seals, make certain the job is done correctly. I’ve seen guys install seals with a punch so they wouldn’t have to take the extra time to locate the right tool. One wrong thump from a hammer can tear sealing material, puncture the seal casing or push the seal through the housing.
Always take time when installing lip seals, and lubricate the shaft and seal adequately to prevent tearing or sticking. Also, verify that the lip seal is the correct size. There must be an interference fit in the bore and on the shaft. Not having the proper size can result in the seal rotating on the shaft or becoming dislodged from the equipment.
Lip Seal Inspection Checklist
- Check for cracked or deteriorated elastomer
- Check for case damage
- Check to see if the breather is plugged
- Check equipment for excessive temperatures
- Check for oil leaks around the lip seal
Maintaining Lip Seals
To help your lip seals stay as healthy as possible, you must keep your oil clean, cool and dry. Any contamination in the oil will get into the contact patch and deteriorate the shaft and elastomer. Likewise, the hotter the oil becomes, the more wear and tear will be exerted on the seal. Lip seals should also be kept as clean as possible. Painting over a seal or having dirt built up around it can create excessive heat and quickly degrade the elastomer.
Failure Causes
If you’ve ever pulled out a lip seal and seen a groove cut into your shaft, this is probably due to particle contamination. Without good breathers, all the dust and dirt that gets into your equipment can destroy not only your bearings and gears but also your shafts and lip seals. Of course, it is always better to exclude contaminants than to try to remove them. Too tight of a fit between the lip seal and the shaft can also create a groove.
Excessive temperature is the leading cause of seal failures. As temperatures rise, the lubricating film becomes thinner, resulting in dry running conditions. Elevated temperatures can also lead to the elastomer cracking or blistering. Nitrile seal life decreases by a factor of two for every increase in temperature of 57 degrees F.
The oil level can be another factor in a lip seal’s lifespan if it is too low. In this situation, the seal will eventually become hard and not be able to follow the shaft, resulting in leakage.
Cold temperatures can cause seal embrittlement. Selecting the proper lubricant and seal material can help in these colder environments.
Seals may also fail due to shaft runout. This can be caused by misalignment, shaft imbalance and manufacturing inaccuracies, to name a few. Different elastomers will tolerate varying amounts of runout. Adding a garter spring will help with any runout that can be measured.
Excessive pressure is another potential cause of lip seal failure. If you’ve ever walked past a pump or gearbox and noticed oil leaking out the seal, the sump has somehow overpressurized and leaked to the point of least resistance. This can be attributed to clogged breathers or non-vented sumps. Applications with higher pressures should employ a special seal design.
How to Inspect a Lip Seal
Among the things to look for when inspecting lip seals include deteriorated or cracked elastomer. This is a telltale sign that heat is an issue. Also, verify that the lip seal is still in place. I’ve seen a few pumps that had the wrong seal installed. Upon startup, the vibration and movement caused the seal to come out of the bore and spin on the shaft.
Any oil leaks around the seal should be a red flag to investigate further. Worn seals can cause leakage, plugged breathers or damaged bearings that allow radial motion.
When analyzing any lip seal failure, look at the seal, shaft and bore. While inspecting the shaft, you typically will see a contact or wear zone where the lip seal was riding. This will appear as a black scuffmark where the elastomer has transferred to the shaft.
Remember, in order to keep your lip seals in good operating order, you must maintain the sump. Cover all seals before painting, keep the oil at the proper level, make sure oil coolers are functioning correctly, and select the right seal design and material. If you are proactive in your approach to rebuilding and installing equipment, you can give your lip seals and machinery a fighting chance at survival.
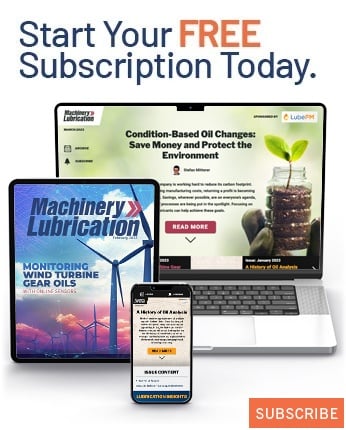