Machine breakdowns are among the biggest production issues manufacturers face. These breakdowns, which are often due to contaminated hydraulic fluid, are expensive, both in terms of repair costs and downtime. This may lead to the plant concluding that it needs to change its oil regularly. Of course, this is costly as well as environmentally unsustainable. It also is not always effective, as contaminants may enter the system again in a relatively short amount of time.
Frequently changing the hydraulic system filters to ensure contaminants are filtered out is a good solution, but this can be expensive and involve some machine downtime. Original equipment manufacturer (OEM) filters are not always adequate for the demands of the system and can often be buried well within the machinery, meaning the fabrication needs to be dismantled to access the filters.
However, bypass filtration units can offer efficient hydraulic fluid filtration with zero downtime for working machinery. These units can be fitted to almost any hydraulic system, even relatively old models that use obsolete parts. They work by extracting a small amount of oil from the reservoir and cleaning it through a number of filters. The decontaminated oil is then fed back into the system. This results in both the hydraulic fluid and the original filters within the system lasting much longer.
Clean Oil
With bypass filtration units, nearly 100 percent of water can be filtered out, and contamination particles can be reduced to 3 microns in a single pass. In fact, if run slowly enough with the fluid being passed through multiple times, these filtration systems can clean oil to any standard required.
Quick and Easy Filter Changes
A bypass filtration system can also be isolated from the rest of the machinery, allowing it to continue to work when the filters need to be changed. In addition, these filters are quick and inexpensive to change when compared to the cost of purchasing and fitting OEM filters or frequently changing the oil.
Fewer Breakdowns
A small British factory had its oil analyzed at NAS 12, which is extremely dirty. This level of contamination resulted in valve blockages, seal damage and machine breakdowns. Initially, when bypass filtration units were fitted, the filters had to be changed every few weeks. Gradually, as the oil became cleaner, filter changes became less frequent. Now the plant changes its filters every 12 weeks, and the oil has been analyzed at NAS 6. Better yet, the factory is experiencing no machine breakdowns caused by dirty hydraulic fluid.
In conclusion, bypass filtration systems can clean oil to any level required and increase the lifespan of the filters within the hydraulic system. This significantly reduces the occurrence of equipment failures, making the day-to-day operation of machinery smoother and more cost effective.
About the Author
Steven North is a design and project engineer at Apex Hydraulics, which has designed and manufactured bespoke hydraulics across a number of diverse industries as well as provided hydraulic repairs and servicing for more than 30 years.
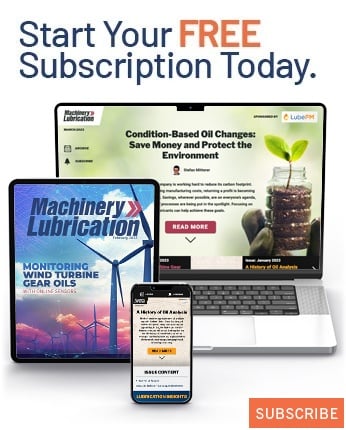