"Which type of cooling lubricant should I use for my machining process?"
Machining metals can cause a significant amount of stress and strain on both the material being formed and the tool tasked with the machining. To extend the life of the tool and achieve a better finished product, cutting fluids are commonly used. These fluids are important to the tool's overall life cycle as well as how the machining process performs its intended function.
A machining center may be involved in many operations, with each stressing the lubricant, material and tool in a different way. Some of these operations like extruding can be very stressful, while others such as turning are generally easier on the machine. One variable that cannot be overlooked is the type of metal being worked or formed.
Similar to most lubricants, metalworking fluids may be formulated with a variety of base oils and additives. These must be married to the operation and the material being machined for optimum results. Unlike traditional lubricants, metalworking fluids tend to have more oil-and-water solutions that combine the lubricating properties of the oil with the cooling capacity of water.
Other base oil options include straight oils, semi-synthetics and full synthetic lubricants. Each of these types is unique and can be blended with an assortment of additives to enhance, suppress or add properties to the base oil.
One issue with additives that are unique to metalworking fluids is the unintended surface interactions with the material being machined. A good example is the use of extreme-pressure additives with active sulfur. These types of additives have been known to stain materials made of a yellow-metal alloy. This could cause the material being machined to be rejected based on the required surface finish. However, these additives can help the tooling process remove material while reducing the damage incurred to the machine tool. Therefore, it is important to select the right additives for the metalworking fluid from the start to get the most return on your investment.
Other additives may also be needed, particularly for those utilizing a water-and-oil solution. To ensure proper amounts of oil and water are delivered to the machining process, the fluid must remain in emulsion. A high percentage of water in the mixture can promote bacterial or micro-organism growth. Preservatives can help maintain an environment that is not conducive to this type of contamination.
As you can see, there are numerous options when it comes to cooling fluids for machining. Many of the same rules apply as with traditional lubricants. They must be selected based on the correct base oil and additives, all while keeping in mind the type of metal being machined and any potential side effects of the fluid on the material.
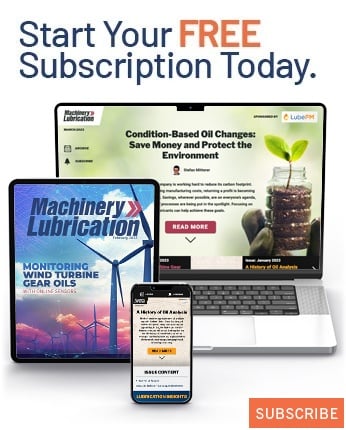