An example of a plate type of bowl
Oil reclamation offers a number of economic benefits. For instance, if oil that is discarded and replaced could be cleaned and put back into operation, tens or hundreds of thousands of dollars could be saved every year. This type of cleaning process frequently involves a centrifuge.
Centrifuges work on the principle of high gravity. In short, anything that is heavier than the fluid will be forced out, regardless of size. With these devices, even small differences in specific gravity are amplified to such a degree that submicron particles quickly settle out.
Centrifuges can break emulsions and remove particulate, including graphite, but they will not eliminate particles held in suspension by Van der Waals forces.
Types of Centrifuges
There is no shortage of centrifuge designs. The variations generally are based on the type of contamination involved. For particulate cleaning and light water removal, a bowl type of centrifuge is a good option. When there is heavy water contamination, a tube type of centrifuge is more appropriate.
For oils that have both water and particle contamination, a more complex centrifuge may be needed to remove and dump solids while separating the water. Unfortunately, the more complex the centrifuge, the higher the cost.
A bowl centrifuge spins the oil, with particulate settling out against an inside wall of the bowl. A layer of water forms on top of the hard particles, followed by a layer of water/oil emulsion and then a layer of oil that progressively becomes cleaner toward the center of the bowl. The clean oil will spill over the bowl’s top edge and drain from the centrifuge.
There are also a few variations on the solid bowl design. For high solids and gentle acceleration, an open bowl containing no vanes or plates is used. Frequently, this is a biological type of bowl that does not rupture cell walls. However, some applications may require minimum shearing because of delicate polymers contained in the fluid. A high solids biological type of open bowl may be used in these situations.
A high solids bowl will also be open with no plates but may have vanes to provide more acceleration to the fluid, forcing it deep into the bowl. No plate is used to make removal of the solids easier.
For difficult cleaning jobs, a plate is added to the high solids bowl to force fluid to the outer wall so maximum G-force can be exerted. The area for solids collection is reduced by the plate. This type of bowl should be cleaned before the solids block off the plate opening next to the bowl wall. Plate centrifuges are also a little more work to clean and operate.
Iron piping is preferred for P-traps.
Bowl centrifuges must be cycled to dump water and sludge. The upper limit for these types of centrifuges is 5 percent water. Higher percentages of water will require excessive cycling. More than one pass may be necessary if the cycle is not well-timed before the bowl overflows with water.
A tube centrifuge has continuous discharge of both light and heavy fluids. It also separates particulate but will quickly fill up with solid matter when the percentage is much more than 0.5 percent. This type of centrifuge must be disassembled to remove particulate and is more labor-intensive when the fluid contains a high percentage of particulate.
Often called oil-water separators, tube centrifuges operate around 15,000 to 20,000 Gs and can break difficult emulsions. The separation factor is controlled by both the flow rate and annular rings that distribute flow over light and heavy output ports.
To ensure the fluid is spinning the entire length of the tube, removable vanes are added to the tube bowl. This bowl contains many parts that must be assembled in the exact location where the bowl is balanced. Keep in mind that a 1-gram imbalance becomes 20 kilograms when spinning at 20,000 Gs, so do not operate an imbalanced centrifuge.
A P-trap is used to block vapors.
Factors in Centrifugal Cleaning
The main factors governing centrifugal cleaning are the size of the particles, the particles’ specific gravity, the fluid’s viscosity, the centrifuge’s power or G-force and the residence time in the centrifuge. Of course, you have little control over the specific gravity of the particles. Some applications may utilize a flocking agent to make the particles larger, but generally this is avoided.
The three factors you can control are the oil’s viscosity, the centrifuge’s G-force and the residence time in the centrifuge.
The centrifuge’s power relates to its relative centrifugal force (RCF), which is the amount of acceleration applied. This will depend on the revolutions per minute (RPM) and radius of the rotor. However, the centrifuge’s RPM will tell you nothing of value regarding the device’s cleaning power. Variable-speed centrifuges allow you to adjust the G-force as required for the application.
Fine, light particles may require a high G-force to separate, but heavy particles can separate at a lower G-force. Test runs should be made during the design of a new cleaning process to ensure particles are not packing so tightly that they are difficult to remove. Also, don’t forget that material weighs several thousand times more in a spinning centrifuge bowl.
The oil’s viscosity determines how easily particles will separate from the fluid. Consider that a handful of dry sand will quickly sink to the bottom of a bucket of water, but the same sand will move very slowly to the bottom of a bucket of molasses. Likewise, thin fluids clean more easily than thick fluids. Gasoline and diesel clean quickly and easily, while heavy oils require thinning.
Heat and solvents are two commonly used methods to reduce viscosity. Generally, oils are heated to just below the boiling point of water. This thins the oil so particles and water separate quickly. At this temperature, much water flashes off as steam and is ventilated from the centrifuge. The remaining moisture is separated as a layer of water in the centrifuge bowl.
Higher temperatures are avoided, as they can cause spurting and spitting of the oil as the water boils. Some applications may use a solvent to reduce the oil’s viscosity. The solvent is removed by distillation or may remain in the oil if it will be used as a fuel.
If the P-trap is too high, oil flow
will be forced to the sludge port.
Steam and Vapor Ventilation
A centrifuge may be self-ventilating or require a vacuum to remove steam. A self-ventilating centrifuge uses a “P-trap” on the clean oil output to block vapors. This forces steam and vapors to the sludge drain where they may be condensed or ventilated.
Venting Vapors
During centrifugal cleaning, vapors may be emitted. Depending on the composition of the oil, these vapors may contain water, methanol or other light hydrocarbons. Larger amounts of vapor are emitted with higher feedstock temperatures. Some centrifuges are designed to ventilate these vapors using a fan formed between the rotor bolts and the grooved lid.
The centrifuge typically can produce air flow of approximately 35 cubic feet per minute through the output ports before piping losses. Directing the flow to the waste port vents water vapor, hydrocarbons or alcohol vapors away from the cleaned oil. Flow is directed by installing a P-trap.
The liquid in the P-trap blocks the flow of vapors. This prevents vapors from collecting in the clean oil tank and condensing. The P-trap may be built from pipe fittings or be as simple as a low place in a hose. The P-trap must also be lower than the centrifuge.
However, a long line before the P-trap will allow vapors to condense in the piping before the P-trap. Secondary traps formed by a sagging hose block the flow of oil and cause the oil output to back up and flow into the sludge drain. Therefore, hoses must not kink. Using a 45-degree elbow on the output minimizes kinking when the clean oil tank is not located directly under the P-trap.
A P-trap with a spot that is too low can block oil flow.
Residence Time
All good things come in time, and clean oil is no exception. If oil is left in a tank for months or even years, eventually a layer of clean oil will form on top. A centrifuge speeds up this process. However, the oil must stay in the centrifuge long enough for the dirt to come out.
Oil that remains in a centrifuge for only a few seconds does not have sufficient time for good cleaning. The longer the oil remains in the centrifuge, the better the cleaning will be. Residence time is controlled by the feed rate.
You may find that a particular oil is cleaned well at 40 gallons per hour, but another oil can only be cleaned at 15 gallons per hour. Trial-and-error testing of the initial installation will quickly determine the best flow rate.
Centrifuge Bowl Cleaning
Knowing what is in your oil before you begin will allow you to estimate the proper draining or cleaning intervals for your centrifuge bowl. Lab analysis can be beneficial but not essential. Tests show that waste motor oil (WMO) typically contains between 3 to 5 percent solids.
When cleaning WMO, solid particles become concentrated next to the bowl wall, while clean oil floats to the center of the bowl, spilling over the top edge and moving out of the centrifuge through the clean oil output port. As the solid particles move to the bowl wall, some of the solid matter sticks to the sides of the bowl, but much of it is concentrated as a slurry of solid particles in the oil.
If you were to slowly feed the oil for a long period of time so all the particles moved to the wall, you could remove all the particles as solid matter stuck to the sides of the bowl. However, such a slow feed rate and the amount of time spent scraping solid matter from the centrifuge bowl would be too impractical and labor-intensive for actual production.
Much of the solid matter can be removed before the bowl fills up. Draining the slurry from the centrifuge before the bowl fills permits a higher feed rate without sludge spilling over into the cleaned oil. This greatly extends the runtime between bowl cleanings and also reduces or eliminates sludge spilling into the cleaned oil.
The amount of sludge concentrated in the centrifuge bowl will depend on the G-force and the feed rate. A higher G-force will equal a higher concentration of sludge. The feed rate must be low enough for the centrifuge to do its job and settle the sludge to the outer wall.
At some point, the bowl will fill with sludge and spill over into the cleaned oil. When this occurs, the centrifuge will be removing very little, if any, contaminants, as they spill over into the cleaned oil as fast as they are removed. To remedy this situation, either slow the feed rate so all particles move to the outer wall and only cleaned oil is discharged, or stop the centrifuge and drain the sludge before it spills over.
How often should the centrifuge be stopped and the bowl drained? An approximate starting point is determined by the bowl size. Operating any centrifuge longer than the bowl capacity is like trying to put 10 gallons of sludge in a 5-gallon bucket.
The runtime between drains will vary by the G-force, the oil’s viscosity and the percent of contamination. The volume between drains will remain about the same. Programmable centrifuge controllers can remove the burden of manually draining the sludge from the centrifuge, allowing automatic, one-pass cleaning.
Applications
While results will depend on how each centrifuge is used, some reports have shown 99.6 percent of particulate being removed from used engine oil. Fleet services have been able to clean their engine oil and blend it back with a percentage of new oil, reducing the cost of replacement oil by 70 percent. Hydraulic shops have also cleaned and reused oil that was contaminated during repairs.
One manufacturer of extruded aluminum parts in the auto industry had 5,000 gallons of oil which had become contaminated with graphite in the pressing process and needed to be replaced at $15 per gallon, plus the cost of disposal. Centrifuging the oil brought it back into service for a savings of $75,000. The manufacturer now maintains its oil with a pair of bowl centrifuges.
Another company has saved more than $250,000 annually by switching to centrifuging and reusing the synthetic oil in its natural gas compressors after previously discarding the oil at the change interval.
As you can see, a centrifuge can offer many advantages and provide an effective method of oil reclamation. Be sure to consider this option the next time you need to discard or replace your used oil.
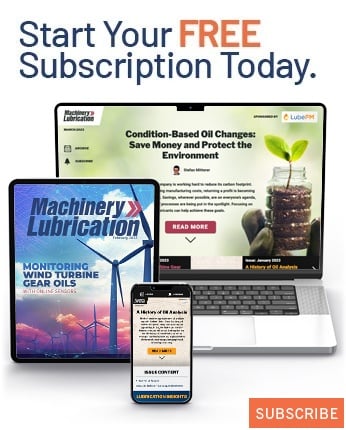