As part of its annual Lube Room Challenge, Machinery Lubrication recently asked its readers to submit exceptional lube rooms that incorporate best-practice features. A number of readers met the challenge and were proud to show how their lubricant storage and handling methods have been transformed. The following entries illustrate how a properly designed lube room marks an important step in the journey toward lubrication excellence.
Anheuser-Busch InBev
When a companywide initiative was launched to roll out a Six Sigma 5-S process at each of Anheuser-Busch InBev’s 32 plants in North America, it became obvious to the St. Louis brewery just how much more efficient and effective it could be if it kept pushing toward a world-class lubrication room. At the time, the plant’s lube room was too small and unorganized with numerous redundant lubricants.
Oils of the same viscosity and greases of the same grade from multiple suppliers took up more room than necessary. There was inadequate space for staff lockers and community cabinets for common lubricants and supplies. There were also no areas of 5-S responsibility for cleaning and organizing the shop. The proper procedures for dispensing lubricants had not yet been employed to maintain quality standards.
The lube room was soon relocated to an area that could provide the necessary floor space to improve the process. All secondary oil containers are now color-coded and tagged to minimize application errors when oils are dispensed.
This process has also been extended from oil containers to grease guns and grease application points. Color-coded plastic washers have been installed under grease Zerks to correlate to the matching color-coded grease gun and grease. All oil drums and totes have high-quality desiccant breathers instead of being vented into the atmosphere.
The 5-S policy has since been utilized to require everything be labeled and organized with part numbers and minimum/maximum quantities. There are now PMs for inspecting and repairing automatic lubrication systems. Technicians are trained to inspect, troubleshoot and repair these systems to ensure that adequate lubricants are reaching critical lube points while preventing overlubrication and leakage. Technicians also are trained to design and install the automatic lubrication systems.
The St. Louis brewery essentially single-sourced a lubricant vendor, which helped to remove redundant oils and greases from the storeroom. This consolidation allowed the area used to store lubricants to be reduced. It also minimized the opportunity for mixing lubricants. As a precautionary measure, all new oils coming into the facility are analyzed and filtered to assure cleanliness standards.
The magnitude of this initiative required personnel to work as a team to create and maintain the lubricant storage area. By standardizing lubrication procedures, consolidating to one primary supplier, maintaining automatic lubrication systems and repairing leaks as they occurred, the plant was able to save money as well as reduce usage and waste.
For example, in the last 11 years, grease usage has dropped by 83 percent, while oil usage has decreased by 82 percent. This has had a significant impact on the brewery’s processes and costs as well as the environment. These efforts have created more than enough savings for the shop to purchase the necessary tools and equipment to improve its lubrication processes and procedures.
As a result of these improvements, the plant has managed to error-proof its lubrication process. By filtering oil and using sealed containers, the cleanliness and quality of all lubricants have improved. The shop is now organized and maintained to the highest cleanliness standards. The mean time to repair for lubrication issues has been lowered considerably by having the right tools, equipment and training to do the job safely and in a timely manner.
The mean time between failures has increased significantly by reducing lubrication-related failures to near zero.
The Anheuser-Busch InBev team members are proud of the progress they have made and plan to keep working hard to maintain the standards that have been set. They also are motivated to continue making changes and improvements until they reach the ultimate goal of zero lubrication- related failures.
Camso Loadstar
When contaminated oil and lubricant degradation resulted in high oil consumption and frequent machine failures at the Camso Loadstar plants in Sri Lanka, the tire manufacturing company approached Noria Corporation for help. During the development of its lubrication program, Camso Loadstar quickly became aware of its poor lubricant storage and handling practices.
Once the loopholes in the lubrication program were identified, a specialized team was created to transform the current program to world-class standards. Several key initiatives were planned, including renovating the lube room, dedicating filter carts and sealable and reusable (S&R) containers for each lubricant, implementing a lubricant identification system, and providing for spill containment.
The company also invested in modern firefighting equipment, desiccant breathers, explosion-proof lighting, a dust-filtered ventilation system and a semi-automatic drum handler. Camso Loadstar’s reliability manager also attended the Reliable Plant Conference & Exhibition to learn more about best practices in lubrication and reliability.
The company soon began to see benefits in terms of cleaner oil, improved machine reliability and reduced lubricant consumption. Modernization of the lube room coupled with implementation of best practices resulted in a 20 percent reduction in oil consumption for the 2016-2017 fiscal year.
Huber Engineered Woods
The Huber Engineered Woods facility in Broken Bow, Oklahoma, is the largest oriented strand board plant in the world. While the plant’s lubrication program was considered good, it wasn’t world class. Improvements had to be made to the lube room. These included adding a new lubricant storage unit, climate controls, storage racks and labeling.
After the initiative was approved, the necessary equipment was purchased and installed. The floor was also cleaned and painted.
The new lube room is now clean, organized and climate-controlled. There is a place for everything, and everything is in its place. The new storage unit allows fluids to be filtered not only upon arrival but also before they are transferred to the equipment.
The new dispensing units have enhanced the ergonomics of oil transfers, while the color-coded tanks, transfer containers and fill points have helped to reduce cross-contamination. Each tank now features kidney loops, level gauges, desiccant breathers and fill pumps.
Better climate control has resulted in less grease separation. Oil cleanliness has increased, and everything is now labeled and easy to find. Because of the color-coded tanks and labeling of fill points, staff members who may be unfamiliar with machinery lubrication can easily find the correct fluid and install it into the equipment.
Suez Environment
Suez Environment is one of Egypt’s leading wastewater treatment companies. When the company began its journey to improve its lubrication program, oil drums were being stored outside and were exposed to the elements.
There was also limited storage for oil barrels and grease pails, so lubricants were stored in various areas of the plant. In addition, the lubricant-handling process was very labor-intensive.
Oil was dispensed without any caps, and the grease type was not identified on grease guns. Although the lubricant types and grades were separated, it was challenging to always keep them in the allocated space.
Prime Oil was brought in to provide best-practice training for maintenance and operations personnel. Many superintendents and managers also attended the classes. One of the training’s objectives was to upgrade the lubricant storage and handling area as well as to raise awareness about the importance of lubrication.
Following the training, new practices were implemented to optimize the operating conditions and enhance lubricant storage and handling.
An investment in a new oil storage and dispensing system helped to eliminate wasted space, time and labor. Inventory is now properly maintained, and employees have a much safer and more ergonomic working environment. Inefficient lubricant transfers are avoided with the new system, while cleaning up after spills, labor costs and absorbent purchases have decreased. The number of in-process drums and employee downtime have also been reduced.
New signage has helped to ensure that the first-in/first-out (FIFO) method is followed. Job aids and work instructions also guarantee that all employees use the same process.
The newly designed lube room is located inside a large shed with proper ventilation, lighting and facilities for cool, clean and dry storage of lubricants and containers. Transfer containers for storing and transporting various lubricant types and grades help to avoid the possibility of cross-contamination.
All previous grease guns were discarded, and a new gun was designated for each grease type. These are the only grease guns utilized in the plant. This allows personnel to identify which guns are currently in use. The grease guns are also calibrated and equipped with a tag, which includes the volume dispensed per pump and the date checked.
Yanbu Cement Co.
The Yanbu Cement Co. (YCC) was the first cement company in Saudi Arabia to have its lubrication program managed by an individual certified by the International Council for Machinery Lubrication. In 2017, YCC formed a stand-alone lubrication division with the primary focus of developing lubricant storage and handling. The plant had been utilizing 10 different lubricant storage areas, which contributed to higher consumption.
These storage areas also did not meet best practices, as they were in an open location with no filtration or breather system. Lubricant drums were stored in an open area and exposed to cement dust and high temperatures, which normally would rise to 131 degrees F during summer.
A single-handle pump was employed for different types of lubricants, which increased the risk of cross-contamination. The oil-transfer containers and funnels used for topping up and filling small gearboxes incorporated an open design. This led to the ingression of dust during the filling process.
Moving to best practices in lubricant storage and handling was accomplished in two phases. In the first phase, a room was renovated for lubricant storage. The most important benefits of this room included keeping all lubricant drums in a closed environment with no dust ingression and having three closed cabinets inside the room for storing oil-transfer containers, grease guns and other accessories.
The new color-coded oil-transfer containers were sealable and dedicated to one type of lubricant to prevent cross-contamination and to ensure that oil added to components would be clean.
The goal of the second phase was to attain lubrication excellence in terms of lubricant storage and handling. A centralized lubrication unit was key to these efforts. The 40-foot custom-designed container was outfitted with fire extinguishers, air-conditioning, air vent fans and racks. The unit has two compartments: a storage section and a dispensing station with 12 color-coded lines. Each line is equipped with pumps and filters.
To minimize cross-contamination, each line is assigned to one type of lubricant and color-coded to correspond to the color of the oil-transfer container. Racks were installed for the 10-liter transfer drums.
In addition, as part of this phase, Noria’s lubricant identification system (LIS) was applied with a minor modification to meet Yanbu Cement’s requirement for a color-blind category. The system consists of different categories to indicate the lubricant, product name, viscosity grade and base oil type.
Each lubricant type also has its own color and shape. For example, a red label with a heart is used to identify a 320 viscosity-grade mineral oil, while black with a clock shape is used to specify a 46 viscosity-grade hydraulic oil.
YCC’s future plans include purchasing kidney-loop filters and desiccant breathers to extend the life of the lubricants in its machines.
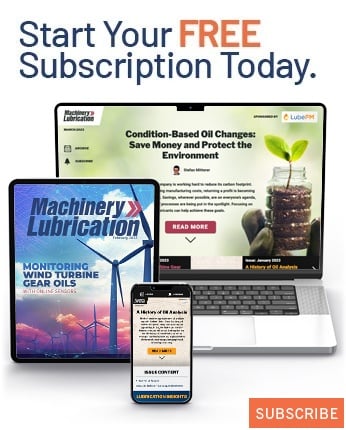