"Should we have different cleanliness targets for the hydraulic systems and industrial gearboxes at our plant?"
There are major differences between hydraulic systems and industrial gearboxes, so you definitely should establish separate cleanliness targets for their respective lubricants. Many factors should be involved in the determination of these targets, including the criticality of the gearboxes and hydraulic systems. Are they process critical?
Also, consider the environment in which these systems are working. Is it hot, cold, wet, dirty or clean? How often are the systems in operation? What is the percentage of runtime – 25, 50 or 100 percent? What load do they work under: heavy or light? What are the start/stop conditions? How long would you like your machinery to last?
All these elements play an important role. For instance, a gearbox operating under light loads 50 percent of the time in a very clean environment with a controlled temperature would be expected to have cleaner oil than the same type of gearbox working 24 hours a day, seven days a week on a coal crusher in a coal-fired power plant that is in the middle of the desert.
While both hydraulic systems and industrial gearboxes have sliding and rolling contact to contend with, their workings are quite different. Hydraulic systems have servo valves with very small clearances. As such, they are sensitive to fine particles and can succumb to silt lock easily if the system is not protected from these smaller particles.
Keep in mind that you can draw a direct correlation between the life of a machine and how clean you have maintained the oil in the system. Many studies have been performed to support this.
As can be seen in the chart below, hydraulic oil is required to be two ISO codes or four times cleaner than gear oil, regardless of the environment. How you achieve this cleanliness level is very specific to the system and its environment. Having good filtration and your equipment outfitted to combat the ingression of dirt and water will be essential, along with employing the correct breathers, regulating how oil changes are performed, using filtered oils with quick connects, and utilizing sealable and reusable transfer containers.
Remember, compared to the cost of removing dirt and water, it is much more cost-effective to keep contaminants out. Removing them will be a waste of manpower and resources.
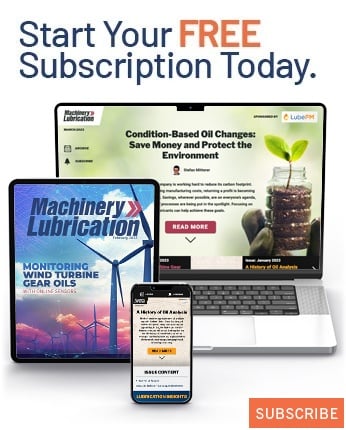