Root cause analysis (RCA), when properly applied, can mean the difference between constant, repeated failures and successful implementation of a world-class maintenance improvement program.
All of your data sources have a part to play and must play this part well. When it comes to mechanical reliability, the data is everywhere, but there remains a source of data that tends to lag behind as a source of useful data: oil condition monitoring (OCM) results.
The Problem
There are several problems when trying to use OCM data with root cause analysis, but there are three glaring issues that need to be considered. The first issue with using OCM data for RCA is that it is rooted in trending. OCM results, in many cases, are only relevant to the previous result that was obtained from the same test on the same component.
Because of this trending aspect, there is difficulty in extracting useful results without a previous sample. With all the tests you may need in RCA, routine OCM testing is simply not feasible in all cases.
Along with the potential for missing previous data, the overall trending aspect must be taken into account. When you have a stable trend, this is based on a relatively consistent sampling practice that is capable of getting useful, accurate data. When you disrupt any of these components, you disrupt the trending, and nothing will disrupt the trend like failure.
Generally, you will have a change in sample location, a change in operating state or a dramatic shift in what problems the component was facing as the failure progressed. Any one of these will easily disrupt your trend, but all three at once is often the situation you will face.
Lastly, you must consider OCM as a technology in general. OCM results, in many cases, start out as an arcane source of knowledge, with the actual nuts and bolts of “what is going wrong” resting with those who have the experience needed to look at a pile of lab results and wring out the answer.
Because of the reliance on a secondary review, it takes more time and effort to get additional data from your OCM results. Most labs that work within OCM will happily assist in any form possible, but this remains a concern.
When you combine these items together, you are left with a difficult source of data from which to extract something useful for your RCA. However, there are ways to get useful data. You just have to know where to look and what (and what not) to expect.
The Goals
With oil analysis, getting useful results is a complex process and is simply not always as feasible as it should be, so you need to start with a goal. Consider your options for where you are collecting data and review them for what you need to know regarding their ability to find out that information.
OCM testing may provide alloy, contaminant or degradation byproduct information, but that is a fairly specialized process that not all OCM labs can handle because it isn’t what they usually do. OCM data may be able to get degradation components for you.
If you are asking for something you don’t normally request from your OCM lab, be sure to contact them before sending off the sample to discuss what you are looking for and if they have the capability to perform the testing. If they don’t, it is entirely possible they will have some insight into who may be able to help and what issue you may be facing.
The Sample
You should start with the quality of the sample from which you are trying to get results and realize the limitations. OCM results depend a great deal on comparing the last result to the current result. Consistency in collecting the sample is king. The less your current sample is obtained from the previous sample method, the less consistency you will have.
Generally, most people’s first instinct is not to pull an oil sample when a component fails. If the oil is still in the system, determine how long it has been since the failure occurred. The longer a fluid has sat in the sump, the more likely it is that you have significant stratification and settling of debris as well as further degradation of the fluid and any existing debris.
This aspect must be kept in mind when you take the sample. Because of the settling of debris and fluid, you may wish to capture two (or more) separate samples – one in what would have been an active zone, as well as a bottom sample, and possibly intermediate samples between those if you have access to them.
If there is a filter housing, you may have useful debris not only in the filter but also in the oil remaining in the housing, so that is another place you might collect oil for testing.
The Testing
When deciding which testing to perform, several factors should be taken into account. The biggest issue often is considering what can be tested for compared to the testing available. The sample volume isn’t always large enough to accommodate the testing you want, so that should be reviewed with the lab.
Typically, a good place to start is to have a routine test slate run to compare with the information you already know about the system. Even if you don’t have a year of history or if this is the first time you have performed oil analysis on the system, information about what the results should look like can help you glean plenty about what has occurred to get it to the current state.
Once you have the base information from typical testing, determine what else you may need to know and what options there are to get you there. A common test to review is a microscopic analysis.
While this will not help in every case, knowing what happened to the metal in the system or what solid and soft contaminants are present can be useful. Microscopic analysts normally have exposure to a wide array of situations and have extensive training in fluid and mechanical component investigations.
Final Processing
In a failure analysis, you are often dealing with unique sample issues. The sample jar may or may not be standard, the debris may need special handling, or it may not be an oil sample at all. Many OCM labs are not set up to handle unique sample receiving because they are geared more toward high-volume, rapid processing.
Be sure to contact lab personnel prior to sending the sample and coordinate with them for delivery and receipt. The experts you may need access to commonly have samples sent directly to them all day long, and the sample-receiving staff may not know that your sample is a unique situation for which normal processing may not work correctly.
Consider the available expertise with the type of issue you are facing. Not every laboratory has a refrigeration compressor expert or a soft-metal bearing expert on hand to review your issue. If they do, you want to work with them or at least have them review your issue to see if they can offer insight. Having access to personnel with previous knowledge about what can potentially go wrong with your type of component can make or break your investigation.
Achieving Your Goals
OCM labs frequently have access to a vast amount of expertise and abilities, but it can be a challenge to get the information you need. However, careful coordination, review and collaboration can yield a vast amount of information to support your RCA goals. Talking to your lab to discuss your situation and goals and staying in contact during the process will ensure you get the best possible rewards.
This article was previously published in the Machinery Lubrication 2018 Conference Proceedings.
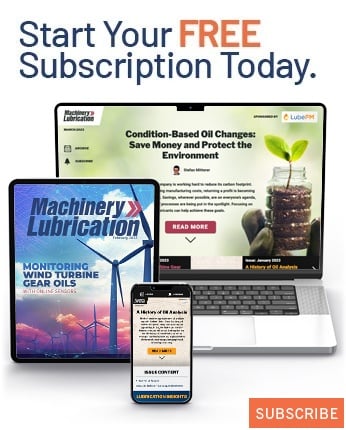