Most used oil analysis labs offer a shopping list of tests from which the user is expected to select a test slate appropriate for his equipment. However, unless the correct oil analysis test slate is selected, vital early warning signals and opportunities for maintenance cost-reduction can be missed. Recommended test packages for different equipment should include both routine and exception testing for a two-dimensional approach to oil analysis.
One of the biggest mistakes made when someone new to oil analysis sets up a program is to expect too much from his or her oil analysis lab. That is not to say that a competent oil analysis lab cannot provide information vital to an effective condition-monitoring program, but rather there is a common misconception that the simple act of filling a sample bottle and shipping it to a lab guarantees a detailed report outlining which widget is failing, why it’s failing and how to prevent it from failing again.
The one item in this scenario that is often overlooked is: “What tests will the lab be performing, and are they sufficient to detect and diagnose the problem?”
Most commercial oil analysis labs provide prepaid sample bottles. The cost of the bottle usually covers a few basic tests such as elemental analysis, viscosity and a screening test for water. While these tests are a necessary first step, and in many cases provide vital information, they should be considered just that - a first step. So what additional tests should be added to these fundamentals tests to provide a complete package or test slate for each component type?
Some labs attempt to address this issue by offering packages, which include both basic and additional tests based on equipment types, and may offer programs such as a hydraulic package or a gear package.
While this one-dimensional approach has some merit and provides a simple, convenient approach to ensuring that more bases are covered, there are still problems with this strategy. The oil analysis industry is price-sensitive, and adding too many tests increases costs, perhaps excluding a lab from being price competitive. Too few tests, however, might result in the failure to detect and diagnose a problem. Selecting a proper test slate is a careful balancing act between frugality and common sense.
The 2-D Approach to Oil Analysis
The 2-D approach to oil analysis is summarized in Figure 1.
Figure 1. The 2-D Approach to Oil Analysis
An initial series of routine tests, which are designed to give early warnings of potential problems, are selected. These routine tests may include standard oil analysis tests or other diagnostic tools such as vibration analysis, thermography, visual inspection or audible or olfactory perception.
However, once a problem is detected, the first question that must be asked is “what is the root cause of the problem?” Then, “how can it be corrected?” This is where the second dimension of oil analysis comes into play. If the routine test slate does not answer these questions, the test scope must be expanded until the root cause is determined - the 2-D approach to oil analysis.
Routine Testing - The First Dimension
The best approach to setting up a routine analysis program is to review each piece of equipment on its own merits and decide which tests, alarms and sampling frequencies are required. This often requires a comprehensive onsite lube survey. Such a survey enables the test slate to be custom designed to match the unique operating environment, application and duty of service.
In order to determine this, it is often useful to conduct a lubricant failure modes effects and criticality analysis (FMECA) to identify the most common problems likely to be encountered based on history.1 Once this is complete, selecting the appropriate test slate, alarms and sampling frequencies is relatively straightforward and will provide the earliest possible warning and maximum diagnostic capability without breaking the bank.
Take for example an industrial hydraulic system that is exposed to a relatively clean, dry environment, but has a history of servo valve failures caused by varnish build-up as a result of relatively high operating temperatures. It does not make sense to include an expensive Karl Fischer moisture test as routine for this hydraulic system, which may never have suffered a water-related failure.
A better choice would be an acid number test to warn of oil oxidation and to allow for condition-based oil changes before varnishing occurs. It is this balance that is vital in selecting an effective but fiscally sound routine test slate.
Exception Testing - The Second Dimension
Although the routine test slate should be selected to provide the maximum opportunity for early detection of a problem, it is unlikely it will give the complete story in all cases. For example, an industrial gearbox may have a history of failure due to fatigue spalling, requiring an effective program to monitor the onset of such a problem.
The best way to determine if spalling is indeed starting to occur is to look for wear particles using analytical ferrography. However, it doesn’t make sense to conduct monthly analytical ferrography at $50 to $100 per sample, only to be told on each occasion that the ferrogram shows normal rubbing wear, until failure starts to occur.
A more sensible approach is to use other less expensive screening tools such as elemental iron and ferrous density to look for early signs of gear failure, and use complete ferrographic analysis as an exception test to help diagnose the problem’s root cause.
Machine Specific Test Slates
As one would expect, the routine and exception test that should be selected will depend on component type, which is the rationale behind the component-specific packages offered by many labs. For example, the type of problems that are likely to befall a diesel engine, are not likely to be the same as those typically experienced by an industrial hydraulic system or gearbox.
These differences should be reflected in the test slate for each type of component and will come out during the FMECA analysis, which should be conducted prior to setting up the test program. As a guide, common routine and exception tests that should be included in any component-specific package for different classes of equipment are provided in Table 1 and discussed below.
Diesel Engines
Diesel engines are complex in design with hundreds of moving parts. The most common problems are likely to be associated with lubricant degradation (oil shear down, oil oxidation, etc.) or contamination.
Likely contaminants include internal and external contaminants such as dirt, coolant from coolant leaks, fuel and excessive soot loading. For this reason, the test slate should focus on these problems because they are the most likely to occur. When excessive wear is observed and the cause cannot be attributed to lube degradation or contamination, or the root cause is uncertain, detailed wear debris analysis using ferrographic tests is recommended.
In certain situations, other tests such as base number or pore block particle counting may also be considered routine; for example, when extending oil drains or monitoring filtration performance.
Drive Train Components
Just like engines, drive train components are susceptible to lubrication degradation and contamination. The most likely contaminants include dirt ingestion and internally generated wear debris. Typically abnormal wear begins with the generation of small particles (less than 5 microns), making elemental analysis an effective wear monitoring tool, backed by ferrous density and/or complete ferrographic analysis for characterizing more severe wear.
Many drive train components, particularly transmissions, contain nonferrous white metals, so care should be taken when applying wear debris analysis tests which are biased toward ferromagnetic (iron and low-alloy steel) particles. For these components, ferrographic analysis using a filtergram as opposed to ferrogram may be better suited.
Lubrication degradation can be caused by both shearing and oil oxidation, requiring careful monitoring of both viscosity and acid number. Measuring the viscosity at both 40°C and 100°C will allow the viscosity at operating temperatures to be determined. This may be important for certain ATF fluids having kinematic viscosities at elevated operating temperatures close to the 4 cSt limit required to support a dynamic load.
Hydraulics
The overwhelming majority of hydraulic problems are caused by particle contamination, resulting in pump, cylinder and valve problems. For this reason, careful monitoring and control of particle contamination are required using routine automatic or microscopic particle counting. Other significant tests include viscosity and acid number to monitor lube condition and allow for condition-based oil changes, along with water testing for any system subjected to high moisture and/or humidity.
For such systems, crackle testing is usually adequate for water screening, because if care is taken, it has a lower detection limit of around 500 ppm. This should be backed-up, however, with a Karl Fischer test for quantitative analysis because high water content can result in premature oil degradation, additive depletion and operational problems, including vaporous pump cavitation.
Because most hydraulic systems contain large volumes of oil, spectrometric analysis is less effective in determining early signs of undue wear unless samples are taken directly downstream from the component that is wearing. For this reason, care should be taken when selecting hydraulic system sample locations, which may require multiple sample points for reliable analysis.
Paper Machine Oil
The prime motivation for sampling paper machine oil (PMO) is to monitor lube condition and contaminants. This is particularly true because most circulating paper machine systems contain several thousand gallons or more of oil, which is typically only changed every five to 10 years, and then based only on oil condition.
Condition-based tests should include rotating pressure vessel oxidation test (RPVOT) and acid number to monitor oil oxidation; demulsibility to determine how well the oil can shed water, a common contaminant in paper machine systems; and elemental analysis to track additive depletion, particularly detergent and rust inhibitor, which are susceptible to water washing.
Common contaminants include fibers, dirt and particularly water which can be damaging to all components but particularly to rolling element bearings. For this reason, it is vital to set fluid cleanliness levels for particles and water and monitor regularly. In these instances, Karl Fischer moisture testing should be considered routine for PMOs because most circulating systems are used to supply lube to large rolling element bearings where water levels should be kept in the 200 to 300 ppm range for optimum bearing life. This range is below the detection limit for water screen tests such as the crackle test and Fourier transform infrared (FTIR).3
Like hydraulic systems, wear debris analysis of primary samples is of limited use in circulating paper machine systems because of dilution effects. If a problem is suspected with a specific bearing or group of bearings (for example, those returning to a common header) secondary sampling and analysis including ferrographic analysis may be valuable to help determine the root cause of a problem.
However, given that most systems of this type contain several hundred bearings, routine monitoring of each bearing is economically unrealistic.
Industrial Gearboxes
Most common problems with industrial gears usually result from misalignment, overloading, lack of lubrication or incorrect lubricant. The focus of any condition- monitoring program should be on detecting the early signs of these or any other problems identified through the FMECA process. For mechanical problems, early detection of wear debris is vitally important, however, some problems, even during the early stages, generate large wear particles (greater than 5 microns), which are undetectable by spectrometric analysis.
For this reason, it is advisable to include not only elemental spectroscopy but also large particle assessment techniques such as particle counting or ferrous density as routine tests. These tests can be backed up by complete analytical ferrography for more exact root cause analysis information.
Most industrial gearboxes have relatively small sump capacities and thus do not necessarily need routine condition monitoring of acid number. However, elemental spectroscopy and viscosity data are vital in determining lubricant degradation and identifying the addition of wrong oil.
Unlike hydraulics and large heavily loaded rolling element bearings, contamination typically has less serious consequences, although particle counting, including percent ferrous using a pore lock particle counter, provides advanced warning not only of large wear particles but also ingested contaminants.
A high particle count and low percent ferrous typically indicate some kind of seal or breather problem, while a high particle count and high percent ferrous are usually indicative of either inadequate lubrication (due to lube starvation or an incorrect or degraded lubricant) or a misalignment. Water is less of an issue in many gearboxes and a crackle test is usually a successful screening technique.
Motor and Pump Bearings
Most pump and motor bearings operate at high speeds and require oil that is clean and in good condition. The focus of a proactive oil analysis test slate should thus be monitoring lube condition and cleanliness. Like engines and drive train components, motor and pump bearings are generally small-capacity systems and are suitable for elemental analysis as the primary means of wear debris detection and analysis.
However, aside from misalignment (which is better monitored using vibration analysis), the main root cause of motor and pump failure is lube condition and contamination requiring careful monitoring of viscosity, additive condition, particle contamination and water content.
Steam Turbines
Steam turbines used in power generation typically have large oil volumes that must be carefully monitored for lube condition so oil changes can be scheduled during a planned outage. Even with a planned outage, the large volumes of oil used in steam turbines make the optimization of extended oil drains a high priority for any oil analysis program.
Therefore, it is vital that lube condition, including viscosity, acid number, RPVOT and additive depletion be carefully monitored. Tracking the depletion of antioxidant additives using instruments such as the RULERâ and RPVOT testing will provide the best options because they are designed to measure the oil’s remaining useful life.
Other keys to proactive steam turbine lube maintenance include monitoring factors that influence the rate of oil oxidation such as heat and water contamination, as well as particle contamination. It is advisable in steam turbine applications to conduct annual tests on all key lubricant properties.
Tests should include oxidation resistance, acid number, corrosivity, rust prevention, foam and air release characteristics and demulsibility according to ASTM D43784.
For steam turbines with EHC systems that use fire-resistant phosphate ester-based fluids, careful monitoring of water content using Karl Fischer moisture and acid number is advisable because these fluids are prone to hydrolytic breakdown. Testing for varnish potential is also advisable.
Gas Turbines
From an oil analysis standpoint, gas turbines are similar to steam turbines, except they have less exposure and hence less susceptibility to water contamination. The focus of any oil analysis test slate for a gas turbine should be similar to a steam turbine and should be directed toward monitoring lubricant health and contamination. The principal cause of oil degradation in a gas turbine is the high temperatures typically experienced in this type of equipment.
As with steam turbines, tests such as viscosity, acid number, RPVOT and antioxidant additive monitoring should be considered routine, as should the oil’s ability to resist corrosion, particularly rusting. ASTM D43784 is as applicable to gas turbines as it is to steam turbines and should be considered an annual requirement.
Compressors
The term compressors covers a broad range of components from reciprocating to rotary used to compress anything from air, process gases or gases in refrigeration units. Because of this, their design and oil analysis requirement vary considerably. For flood-lubricated screw-type compressors most commonly used for compressing air, mixing the gas with the lubricant requires careful monitoring of lube condition.
This includes viscosity and acid number, because intimately mixing the two under the typical high discharge temperatures of most compressors of this type makes oil oxidation a real possibility.
Although not excessively large in capacity, many compressors require expensive synthetic fluids such as ester or polyglycols to handle high temperatures and/or gas mixing compatibility issues. Because of this, tracking lube condition for condition-based oil changes should be a high priority.
Compressors can contain different types of oil-lubricated components including gears, plain and rolling element bearings and rotor contacts in flooded compressors. Therefore, fluid cleanliness is of paramount importance and must be carefully monitored using particle counting.
Compressors used to compress flammable liquids and gases (methanol compressors) may also require routine flash point testing to help determine contamination levels. As with most components, the root cause of excessive wear may be determined using advanced wear debris analysis tools such as ferrographic analysis.
The success of oil analysis is inextricably linked to the test slate selected for each piece of equipment. If the tests are not broad enough, or in some cases not sensitive enough to provide sufficient early warning signs of a problem, success is unlikely. However, detection is just the first stage.
The real value of oil analysis is to explain the root cause of specific lubrication related problems. To achieve this, it is vital that the oil analysis user step out of the realm of routine and into the world of exception to allow for effective, timely root cause analysis.
*RULER is a registered trademark of Fluitec International (www.fluitec.com)
References
- Troyer, D. (2000, May-June). How to Lube Up Your FMEA Process. Practicing Oil Analysis. pp. 43-52.
- Thibault, R. (2000). Converting to Condition Based Oil Changes. Practicing Oil Analysis 2000 Conference Proceedings. Tulsa, Okla.: Noria
- Eliot, S. (1999, January-February). Fighting Bearing Failures with Additive Chemistry. Practicing Oil Analysis. pp. 21-22.
- ASTM D4378-97. Standard Practice for In-service Monitoring of Mineral Turbine Oils for Steam and Gas Turbines.
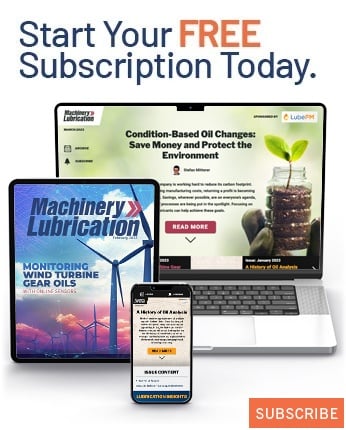