Oil analysis has been the backbone of reliability programs over the past century. From the earliest instruments used by laboratories to the more modern, miniaturized benchtop equipment, this technology has transformed the way and speed by which maintenance decisions are made. Among the latest advancements are in-line, real-time oil sensors, which promise to deliver true online monitoring capabilities.
Previous sensors generally were simple, single-point dielectric, conductivity or permittivity measurement devices used to detect oil oxidation but were not sensitive to other key parameters.
The newest sensors are capable of not only detecting degradation of the overall oil quality but also estimating the percentage of soot, base number, relative humidity, additive depletion, etc. These devices can identify most, if not all, events and project the remaining useful life of the oil while the asset is in operation.
Event Detection
Although these sensors cannot replace laboratory analysis results, they can provide the necessary insight to make preventive maintenance decisions before damage occurs. New sensor technologies utilize electrochemical impedance spectroscopy (EIS), which covers a broad spectrum of oil properties and enables sensitivity to most failure modes.
In Figure 1, an online oil-quality sensor was installed on a diesel engine operating in off-highway conditions. After an oil change, there was a break-in period, and the oil-quality reading peaked for that cycle. As the engine continued in operation, the sensor readings trended down as the oil quality degraded.
While in operation, the engine developed a coolant leak that would have gone undetected and severely damaged the equipment, forcing a full engine rebuild.
Upon a significant break in the oil-quality trendline and an increase in relative humidity detected by the sensor, an investigation discovered the coolant leak. The equipment was repaired, and the oil was changed and put back into service with minimal downtime.
Figure 1. Oil-quality readings
from an online sensor installed on a diesel engine
Oil Drain Optimization
Optimizing oil drains is another important benefit of oil-quality monitoring. Unlike previous generations, the newest sensors can track and trend most of the major indicators for condemning the oil. Figure 1 offers a good example of a normal trendline: The oil has a break-in period, peaks and then degrades over time.
This degradation of the trendline lets you predict when condemning limits will be crossed, allowing the oil’s remaining useful life to be forecasted. Being able to not only detect when oil changes are required but also to predict the oil’s lifespan is a major enabler for oil drain optimization.
In Figure 2, an operator installed an oil-quality sensor on a piece of mining equipment to monitor oil changes. Upon review, it was found that the oil changes were occurring on average at around 25 percent of the total remaining useful life. This left approximately 75 percent of the oil’s life unused. In most cases, the oil was changed before it had even been broken in.
By using the data provided by the online sensor, the operator was able to change the drain interval practices from being based on the number of in-service hours to being condition-based. This has led to a savings of nearly $40,000 per asset per year through decreased oil consumption while significantly reducing downtime and environmental waste in the process.
Figure 2. Readings from an oil-quality sensor used to monitor oil changes on a piece of mining equipment
Additional Improvements
New sensing technology is just now starting to reveal all the ways that it can help reliability programs. As the use of these sensors increases, more improvements can be expected, from optimizing top-offs and bleed-and-feed methods to advanced filtration, additive replenishment systems, etc. For now, these early wins are driving adoption at a significant rate by changing the way best-in-class reliability programs operate.
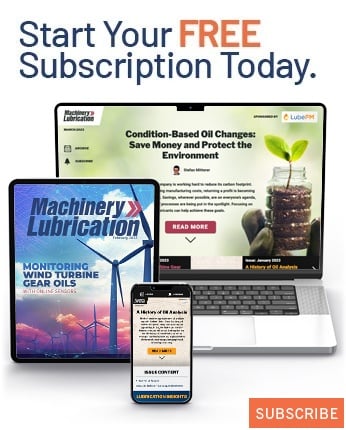