We’ve all seen them. Perhaps some of us daily. Many take on a certain beauty, almost like a natural cave formation or a work of art. Most have organic characteristics like mosses or algae.
Dust cakes need airborne dust and oil to feed their growth. Some get their oil from escaping headspace mist, while others extract oil themselves from adjacent grease by a slow, sucking action (capillary forces) within the cake. Leaking oil from machine case joints and seams can lead to enveloping dust cakes too. The available supply of oil and dust determines the growth rate and the wrath they can impart.
No one enjoys removing and cleaning this muck, which is often why dust cakes continue to grow. We see them but we don’t see them, like a dirty smudge on a carpet. After a while, they get subconsciously blocked from our view and concern. Of course, such blindness feeds a lethargic and dismissive culture that is contrary to any serious reliability effort.
If dust cakes are a common sight in your plant, that may indicate that a more robust lubrication program is needed. A good place to start to turn things around is to understand the real danger of doing nothing or deferring corrective actions. After all, there is a devil within these dust cakes.
Figure 1. Backstop breather has caked-on dirt down the elbow and along the case. This is usually due to oil mist that has migrated out of the headspace and collected on nearby surfaces. Airborne particles adhere and build up on the oil-damp surface forming layers of heavy, caky grime. Too much oil mist results in the need for frequent top-ups (oil and labor costs) and fluctuating oil level control. In many cases breathers function much better and last longer if they are positioned higher with a pipe extension. Ref. Kevin Albert
So Why Do We Care?
Answering this question is the theme of my column. It’s time to give dust cakes serious attention. Of course, work environments differ, and for many industries this problem is nonexistent. For others, it’s like a bad rash that keeps coming back, especially in plants where machines are outside and in contact with dry blowing air. For some, like cement plants, the cause of the dust comes from work materials and stock.
What follows are the potential consequences of leaving dust cakes unresolved.
Figure 2. Notice how far oil from purged
grease travels along the base and case wall.
Impaired Sound and Vision
Operators and inspectors need to be able to see the machine and its components-all of it. Dust cakes can mask the line-of-sight and dampen audible clues of machine condition. Someone should always be thinking, “What is underneath that layer of cakey-grimey mass that we need to see?” Here are some examples of what your dust cakes could be hiding:
- Seals: All seals will fail eventually. Early detection of issues with seals and packings is necessary to avoid expensive bearing failures due to lubricant starvation and dirt ingression.
- Sight Glasses: Level gauges, BS&W bowls, inline sights, etc. all need to be seen and examined clearly for oil condition and level.
- Shaft Movement: Abnormal shaft and coupling movement must be detected early.
- Frame or Bolt Movement: Fasteners such as jack bolts, anchors, studs, etc. need to be easily examined for movement and looseness.
- Instruments and Gauges: These have no practical use if they can’t be frequently and clearly inspected. If dial faces are obstructed by dust cakes, readings aren’t taken.
- Oiler Sumps: Total-loss oiler sumps, bottles and reservoirs need to be inspected to determine adequate reserve lubricant supply.
- Inspection Windows: These are used for different purposes including checking part movement, oil ring rotation, lubricant nozzle spray, etc. Dust cakes restrict their view.
- Breathers: Restricted view of color-indicating desiccant from hydration never makes sense.
-
Guards: Mesh guards on belts, chains and couplings must be clean to inspect tension and alignment of moving parts.
Figure 3. Dust cake buildup near
leak area on gear case and base. Notice
sight glass and oil fill port. Ref. Torki Ibrahim
Impaired Heat Transfer
Heat is a fundamental enemy of machine reliability, both the cause and effect of so many failures. Dust cakes form a thermal insulating blanket around the machine surface that impedes the ability for internal heat to escape and to be known. This causes the heat to build within the machine which can lead to an assortment of runaway problems. Many relate to the infamous Arrhenius Rate Rule (for every 10C increase in temperature, life is cut in half).
- Reduced Oil and Grease Life: Arrhenius Rate Rule (ARR) related to base oil and additive life.
- Short Seal Life: Heat degrades seals more rapidly, causing them to harden, glaze, crack, crumble and loose elasticity.
- Higher Rate of Corrosion: Most forms of corrosion are temperature sensitive.
- Shorter Filter Life (thermal fatigue): Many types of filters experience thermal fatigue leading to cracks and rupture.
- Shorter Motor Life: A 10C increase in temperature cuts electric motor life in half.
- Viscosity Starvation: Abnormally high lubricant temperature thins the oil (less viscous) which can cause higher rubbing, galling and abrasive wear.
-
Inhibited Film Strength: Heat can prematurely deplete important additives such as antiwear and antiscuff additives.
Figure 4. Large gearbox (4 reduction stages)
used in a steel mill. Leakage around
oil pump went unnoticed, ignored or
just deferred for later repair.
Little by little the gearbox drained
of oil resulting in a thick dust cake.
Oil pressure gauge was obstructed by the cake.
Ref. Ronald van Druten
Contaminant Ingestion
The closer contamination (dirt and water) get to ingression points, the bigger the problem. Dust cakes hold particles near critical interfaces at seals, joints, hatches, ports and other high-risk ingression zones.
- Grease Fittings: In many cases, caked-on dirt is so thick that grease nipples cannot be seen. The activity of cleaning the region prior to relubrication can cause particles to get pressed into the grease nipple port. Regreasing can then drive these particles into the core of the bearing where harm is waiting to be done.
- Fill Ports: Oil mist cakes around fill ports and hatches place particles in close proximity to the opening during routine servicing (top-ups, oil changes, sampling and inspections).
- Dirty Breather Media: Dust cakes packed around breathers interfere with air flow, in and out. Inhaled air across or through dirt can cause surge ingression of particles and lead to frequent need for breather replacement.
- Sump Sediment: Over time dust cakes that draw particles into the machine result in sediment buildup on the bottom of sumps, reservoirs and gear cases. Over time there can be more sediment in the sump than oil. The oil level gauge may show a full charge, but that is often not the case. Half the oil means half the oil’s service life.
- Short Filter Life: The job of the filter is to remove particles from oil. The more particles are permitted to ingress the harder the filter has to work to keep up with ingression. The result is shorter filter service life plus the added cost of labor to replace them.
Dust Cakes Extract Oil from Grease
A lesser-known problem associated with dust cakes is grease dry-out. Oil can be extracted from grease if there is either an absorbent path or a gravitational path. This is easily observed by placing a dollop of grease on absorbent cloth or paper. A portion of the base oil from the grease will be wicked out of the thickener. This hardens the grease, impairs mobility and reduces the oil content needed for lubrication.
Dust cakes around exposed grease zones on bearings, gearing, hinge-pins etc. will have a similar effect. It’s not much different than applying Oil-Dri (calcium bentonite) on an oily workshop floor or driveway. Fine dust cake particles that build up have high surface area. They slowly draw oil out of the grease in the machine. The more oil that is extracted, the more dust particles will collect, forming an increasingly thick cake. Resulting drier and harder grease inside the bearings, etc. will potentially have impaired lubricant flow, lubricant film strength, restricted part movement and obliterated oilways and glands.
Figure 5. Enveloping dust cake impairs ability
to take vibration readings, use heat gun
and visual inspection of all critical
component surfaces on this machine/pump
train. Ref. Tor Idhammar
Impaired Condition Monitoring
I’ve talked about the importance of having an unrestricted line of sight for visual inspection of all machine surfaces. Dust cakes also interfere with the ability to properly perform condition monitoring data-collection tasks. For instance, there needs to be visible spots and hookups for taking vibration and temperature readings. “I wonder where the last guy took the readings for good comparison?” Clean surfaces are also needed for ultrasound, thermal imaging, stroboscope checks and motion amplification. Proximity probes function best under clean conditions too.
Dust Cakes Hide Warnings and Other Important Data
Many machine surfaces and adjacent objects will contain posted signs or other warning labels that are intended to remind personnel of safety concerns in the area. If these are not kept clean, the dust cakes can build up, making their presence go completely unknown. Better to keep these signs legible and avoid an injury event than to find out that dust was the root cause after the fact. Even nameplates, lubricant labels and maintenance data plates that are posted on the machine will go unnoticed if covered by dust cakes. This can lead directly to impaired lubrication and maintenance activity performance.
Whack-a-Mole
Exterior contamination and dust cakes telegraph the wrong message to staff and encourage a culture counter to machine reliability. Many plants, by the very nature and/or location of their business, fight a seemingly unending battle with dust cakes, like a game of whack-a-mole. That said, turning a blind eye makes things so much worse and has a compounding effect. Having an honest understanding of the real costs and downtime associated with proactive (keeping machines clean) versus reactive (cycle of repeated repair and despair) is a good start.
Special thanks to Tor Idhammar (IDCON), Torki Ibrahim (Yanbu), Kevin Albert (SULP) and Ronald van Druten (IJSSEL) for images.
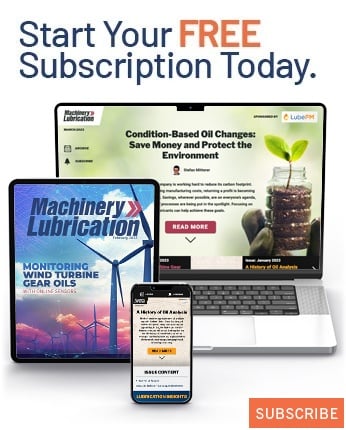