You are probably familiar with a lot of the different ways contaminants can find their way into your machinery. For example, one of the most common ways that contaminants enter your lubricant is through poor headspace management. Having an open vent or a factory vent plug on the machine doesn’t really do much for contaminant prevention. Yes, those vent plugs allow the machinery to “breathe,” but who knows what type of harmful particles that machine is actually sucking in. Those vent plugs and J tubes might as well just be a wide-open port. Another common ingression point that we are all aware of is water. Water contamination can happen through poor headspace management, blown seals, improper seals or by utilizing a lubricant that isn’t compatible with the seal. Water ingression can come from condensation, rain or even the industrial process that the machine is involved in; these are issues we know about. What I want to focus on, though, is uncommon ingression sources. What sources allow contaminants that we don’t think about or aren’t so obvious?
New Oil
It starts with the reception of new lubricants. Each facility should implement and utilize a quality assurance/quality control procedure for receiving new lubricants. Is it the correct oil? Cross-contamination is still contamination; for example, if you mix two gear oils that are going into a worm gearbox, but one has EP additives, well, you can say bye-bye to the yellow metals in that gearbox.
The next question you need to ask is, “How dirty or contaminated is the new oil coming in?” If you have ever taken Noria’s Machinery Lubrication Level I training, you should know that new oil is NOT clean oil. We pound this into your head during training. So, as far as uncommon contaminant ingression sources, new oil is one that is often overlooked. It should become standard practice to sample new oil coming in and to clean it before putting that lubricant into service. I always advise “filter in and filter out,” meaning to filter new oil coming into your storage tank and filter that same oil as it comes out of the storage tank and into a container to fill a machine. If it is going straight from the oil drum to the machine, then make sure to utilize a filter cart to clean that oil before it enters the machine, which brings me to my next uncommon ingression source: improper lubricant handling practices.
Lubrication Handling Practices
As a traveling consultant, I visit just about every type of manufacturing industry across the board, from food to fuel, roofing to flooring and everything in between. If I had to make a blanket statement about something every plant could do to improve its contamination prevention practices, my advice would be to improve your handling practices. The most common factor we see that leads to contaminant ingression is mishandling lubricants as they are being put into service. By this, I mean utilizing reusable funnels, dirty top-up containers, dirty fill nozzles in bulk storage, dirty lube rooms, galvanized top-up containers, non-dedicated equipment and having no dryness or cleanliness targets (this list doesn't end here, I could quite literally go on all day long). Utilize the ISO 4406 Standard and set some cleanliness targets for each lubricant, especially the oils that go into critical equipment. My point is, from the time your facility receives that new lubricant until that lubricant gets put into service, the process of handling that lubricant should be as squeaky clean as you can possibly make it. I mean, truly take ownership of your lubricants for maximum machinery reliability and machine life extension. Be a stickler about the process so that, come game day, your lubricant performs as optimally as possible.
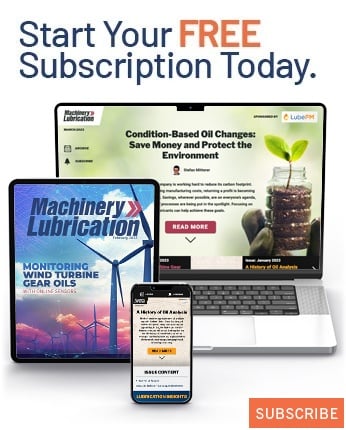