Throughout the years, there has been an unwavering emphasis on the importance of oil cleanliness in both mobile and stationary equipment. This notion took off at the turn of the century, a time when companies were beginning to take more ownership of machine reliability and asset performance. The paradigm shift led to a boom in technological advancements that have allowed us to better care for machines and even predict imminent failure. Though there are many elements of an effective reliability program today, a strategy to maintain oil cleanliness continues to lie at the foundation.
How Contamination Causes Equipment Failure
Oil is the lifeblood of machines, used for the purposes of lubrication, power transmission, surface protection, heat transfer and surface cleansing. However, as it performs these functions, oil characteristically collects contaminants that wear on machines and components and cause the oil to degrade faster.
Contaminants can be gaseous, fluid, semi-solid or solid, all of which can wreak havoc on machine components. 82% of mechanical wear is caused by particle contamination, and as little as one teaspoon of dirt in 55 gallons/208 liters of oil could equate to about a billion particles 4 microns and larger. This level of contamination can be rather dangerous. The viscosity thins, generating wear and preventing the oil from protecting the component parts. Additives in the oil can become depleted trying to manage the level of contaminants, leading to shortened oil life and shortened equipment life.
Damage caused by contamination often goes undetected in the early stages, as the effects slowly accumulate over time. For example, if a hydraulic system is affected by contamination, it can take as much as 20% loss in efficiency before an operator notices the problem, all while energy consumption increases and component wear accelerates.
Clean Oil for Improved Reliability
In most markets, an organization’s edge is derived from the ability to produce the highest quality product at the lowest cost. This is driven by consumer demand and implemented through machine reliability. As we know, reliability is about being able to depend on equipment to produce what it is scheduled to produce, when it is scheduled to produce it, for as long as it is scheduled to produce it with no interruptions.
Considering oil’s role in reliability, if there are fewer particles in the oil, there will be less abrasion, adhesion, and corrosion. If there is less abrasion, adhesion and corrosion, the equipment will last longer. If the equipment lasts longer, it will perform its designed function over a longer period of time and the equipment will be more reliable.
Looking at the big picture, clean oil decreases the lifetime operating expense on the equipment, which maximizes the lifetime usefulness, producing a greater return on investment. Improved reliability will put a company at the top of the ladder of preferred manufacturers or suppliers with the highest quality product at the lowest cost. In the end, this allows for a higher profit margin and an increase in the shareholders’ return.
Reducing Costs Along the Way
Clean oil saves costs in several ways including less downtime, less component replacements, less oil waste, and fewer man hours spent tending to machine failures. One of the most common lubrication mistakes that plants make every day is disregarding the costly impact of changing oil too frequently. When oil is kept clean, you can extend oil change intervals, minimize purchase of new oil, and reduce frequency of oil disposal (or you find a way to stop changing oil altogether). Many plants find that the resulting increase in reliability frees up maintenance budgets to tackle other issues.
Environmental Impact of Keeping Oil Clean
Businesses around the world carry an environmental responsibility to cut waste and reduce emissions. Not only is legislation being formed to enforce this responsibility, but both consumers and investors are actively considering strong sustainability credentials when deciding to associate with a company.
For manufacturing facilities, keeping oil clean allows you to use oil longer and cut down on the purchase of new oil, helping to meet evolving environmental regulations. Used oil is slow to degrade, a major source of contamination in waterways, and can even contain toxic chemicals and heavy metals. By implementing contamination control tactics, the volume of disposed oil is reduced, protecting our environment in a major way over the course of years.
Contamination Control Tactics
Now that you’re aware of how contaminants cause wear in machines and affect your maintenance budget, it’s important to translate that knowledge into action. It is surprisingly common for plants to go to great lengths in monitoring the condition of their equipment and their lubricants, but to do very little to address the problems that are uncovered. The bare minimum requirements for contamination control include the following.
New Oil Filtration
The first step in providing clean oil is to have a good filter in place to catch contaminants that reside in the oil when first delivered to the plants, whether in drums, pails or bulk deliveries. A filter system or cart must be employed at the first intrusion into the oil container and at each lubricant transfer thereafter.
Effective Headspace Control
If oil is circulating in a reservoir or churning around the inside of the housing, then air is sure to enter and replace the changing volume of oil as the air level changes. In that instance, the air must be filtered to remove all of the fine particulates that suspend continually in the atmosphere. This will help prevent atmospheric ingression of contaminants.
Effective Transfer and Periodic Filtration Capability
Quick-connects should be installed on transfer hoses to prevent contamination of the transfer hose from the immediate environment and to provide leak-free connections to tanks or reservoirs. Quick-connects also provide a means for off-line filtration should a contaminant level rise above the target set for the machine.
A New Way to Manage Cleanliness
Achieving cleanliness with the aforementioned tactics is almost always costly, yet the benefits gained are usually multiples of this cost. Just like we seek the optimum state of reliability, we should also seek the optimum state of cleanliness as a subset of reliability.
With that said, new technology is changing the way we view oil. SKF’s RecondOil provides a way to eliminate even the smallest contaminants with Double Separation Technology (DST). DST features a chemical/mechanical process that uses surface polarity to attract and remove contaminants from the oil. With this, there is no lower limit on the size of particles that can be removed from an oil, changing our perception of oil from a costly consumable to an asset that is maintained to last a lifetime.
Learn more about RecondOil at https://www.skf.com/group/services/recondoil
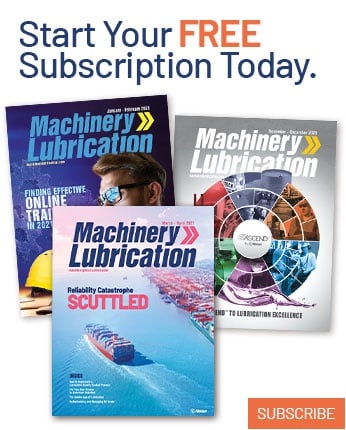