Many companies utilizing rotating equipment have either initiated, or plan to initiate, decarbonization strategies. This is a process that reduces and compensates the emissions of the carbon dioxide equivalent (CO₂e) down to “Net Zero”.
Lubricants are an essential component in rotating equipment, so we must determine the most optimal and sustainable ways of managing these fluids, which includes enhancing their performance.
Life Cycle Assessment (LCA) is a methodology for assessing the environmental impact associated with every stage of a product’s life cycle, and it is the accepted tool to analyze a product’s potential environmental impact. It is the optimal tool for measuring a lubrication program’s sustainability and comparing various products and strategies.
The process of performing an LCA is defined in ISO 14040 and takes a thorough inventory of all the materials and energy required to make a product, calculating a cumulative potential environmental impact. Part of this calculation involves assessing various midpoint indicators, such as:
- Stratospheric ozone depletion.
- Acidification.
- Eutrophication.
- Water scarcity.
- Toxicity potential.
For the purposes of this paper, we will focus on the global warming potential measured in CO₂e.
LCA is a useful tool for a variety of purposes. For example, how do you know if an electric vehicle will lower emissions compared to an internal combustion vehicle? What if the electric vehicle gets its power from a coal-burning power plant? Doesn’t mining lithium and manufacturing batteries produce a lot of emissions? There are a lot of complexities with these questions, and the answers would not be possible without performing a cradle-to-grave LCA.
Cradle-to-Gate Versus Cradle-to-Grave
When performing an LCA on a lubricant, one can look at the product’s various life stages. Cradle-to-gate represents the carbon impact of a product from its inception to the moment the product is ready for sale. This is the most common LCA performed on lubricants, as manufacturers do not have control over the use of the product once it is sold. Cradle-to-grave also covers the product’s use and how it is treated at its end of life.
The image below illustrates these stages and identifies the difference between cradle-to-gate and cradle-to-grave.
The CO₂e contribution of extracting, refining, and blending the crude oil (cradle-to-gate) makes up a smaller value of greenhouse gases compared to its end of life (cradle-to-grave).
Although antioxidants have approximately twice the carbon footprint of mineral oils, they contribute a relatively small amount to the overall total since they are used at a small percentage in the formulation. Depending on what part of the world the used oil is generated, the contribution of CO₂e at the end of life is defined by what percentage is incinerated or re-refined.
Different base oils may also contribute more CO₂e to the overall product. For example, polyalphaolefins (PAOs) have about twice the cradle-to-gate CO₂e footprint as mineral oils. However, the end of life of both products is the same, representing a larger percentage. The overall CO₂e contribution of a mineral turbine oil versus a PAO turbine oil is illustrated in Figure 2. Therefore, the effort to extend the life of in-service oils will have a significant impact on lowering the total carbon footprint of a lubricant.
It is also interesting to note that transportation plays a minor role in the overall carbon footprint. This is the case as long as lubricants are not being flown around the world.
Comparing Lubricant Sustainability
There are many factors that go into measuring the sustainability of a lubricant. Figure 3 illustrates the various factors and pathways for making a lubricant more sustainable.
Using a comparison like this, it is possible to compare the sustainability of various lubricants and lubrication practices. Keep in mind that each category can be converted to kg CO₂e, except for environmental performance, which is its own category. Biodegradability performance, bioaccumulation results, and the oil’s toxicity rating are important aspects of the oil’s sustainability, but because they are on different scales, they must be directly compared.
Based on this spectrum, the ultimate sustainable lubricant would be one that:
- Is plant-based (oleo-sourced).
- Is made from renewable energy.
- Is readily biodegradable.
- Is non-toxic.
- Doesn’t have bioaccumulation.
- Provides a long service life.
- Improves the energy efficiency of the system its lubricating.
- Is re-refined or reused in other applications at the end of the fluid’s life.
Also, for a sustainable lubricant to be practical, it needs to be fully compatible with the application, including materials of construction and contamination ingression. For example, an oleo-based ester may tick all the boxes but may shrink system seals and hydrolyze due to high water contamination, making it unsuitable for a specific application.
Lubricant Sustainability Case Studies
The following are two examples of comparing the sustainability of different lubricants using LCA. The examples illustrate that the product with the highest cradle-to-gate carbon footprint is not necessarily the one with the lowest carbon footprint once a cradle-to-grave analysis is performed.
Case Study 1: Avoiding a “Varnish Flush”
Maintaining a turbine oil with low varnish potential has many financial benefits for a power plant. In addition to increased availability and reliability, one may avoid having to do a “varnish flush” in between oil changes. Flushes are both energy and volume intensive, which accumulates to a sizeable carbon footprint.
For this case study, a solubility-enhancing technology was put to the test to examine its sustainability impact on an in-service turbine oil in the hopes avoiding having to perform an oil flush. This technology, which claims to decontaminate lube oil systems, thereby helping rotating equipment users avoid the need to perform a varnish flush, was added to an in-service gas turbine oil at a rate of 3%. The gas turbine oil had a 5,000-gallon reservoir and an eight-year lifespan.
The cost and carbon footprint of adding the solubility-enhancing technology were compared and measured against the value of not having to perform a flush during the next oil change. The results can be viewed in Figure 4.
By using solubility-enhancing technology and avoiding having to perform a lube oil system flush, this turbine would avoid generating 18 metric tons of CO₂e per year. A calculation like this would be challenging without performing a cradle-to-grave LCA. As with most sustainable lubrication practices, avoiding a varnish flush also saves considerable money for the power plant.
Case Study 2: Replenishing Turbine Oil Antioxidants Instead of Performing an Oil Change
Antioxidants are sacrificial components in turbine oil formulations. The life of a turbine oil is largely dictated by the rate of antioxidant depletion, with the condemning limit by most OEMs and industry bodies stating that action needs to be taken when the antioxidants reach 25% of their original value.
The traditional approach when the life of the antioxidants has been consumed and the oil is at the end of its life is to drain, flush, and recharge the system with new turbine oil. However, this consumes outage resources and is expensive, so many plants have considered simply replacing their antioxidants instead.
Custom-made antioxidant concentrates can be added to turbine oils, provided the correct up-front qualification tests are performed to certify compatibility. This emerging practice has been done successfully in hundreds of turbines and is a cost-saving alternative to the old model of dump and replace. It seems that this would also be environmentally beneficial, however, to quantify this, an LCA is required.
Below is an example of a large frame cogeneration system with a single shaft configuration. Since the system is in Eastern Europe, a whole new set of assumptions is required compared to the first case study. Transportation and the percentage of oil that is re-refined versus incinerated are two examples. Figure 4 shows the results of adding an antioxidant concentrate to the in-service oil.
In this case, over 200,000 kgs CO₂e are estimated to be saved over a ten-year period, which translates to almost 60 kgs CO₂e per day. The power plant also benefits from cost savings, waste reduction, and other benefits.
Other Strategies to Manage Oils in a More Sustainable Way
There are multiple other lubricant management strategies that can lower the carbon footprint of your lubricant program, including:
- Selecting the best-performing oil for your application, resulting in longer drain intervals and lower maintenance costs.
- Implementing an oil analysis program to optimize the drain intervals of your oils. Keep in mind that not acting when oil analysis warrants not only increases maintenance costs but can also dramatically increase your carbon footprint.
- Avoiding varnish. In addition to failed components, deposits can create an insulating layer on bearing surfaces resulting in higher temperatures, which lowers the system’s energy efficiency.
- Re-refining an oil at the end of its life. Creating a circular economy with your lubricant at the end of its life by re-refining instead of incinerating will reduce your lubricant program’s carbon footprint.
- Minimizing contamination ingression. Studies have shown that contamination is responsible for up to 70% of premature machinery failures. Deploying a strong contamination control program not only saves significant operational costs but will also reduce the associated carbon footprint.
Summary
As the saying goes, “If it doesn’t get measured, it doesn’t get managed.” In the case of achieving sustainable lubrication, using cradle-to-grave LCA principles allows you to measure and improve the sustainability of your lubricant program. This paper illustrates how to perform these calculations, and as the case studies illustrated, the initial carbon footprint of the lubricant does not necessarily mean decreased sustainability.
Performing these LCA studies allows users to easily identify areas for improvement and can quantify the benefits. These calculations can also shed some light on the practices which should be negated to assist in the decarbonization efforts, such as lube oil flushing illustrated in Case Study 1.
The carbon footprint of lubricants may seem small, especially if one does not consider “product use” in the LCA equations. However, tribology can have a tremendous impact on lowering society’s carbon footprint. A report to ARPA-E in 2017 calculated that 24% of energy can be saved annually through tribology efforts. Measuring these efforts start with cradle-to-grave Life Cycle Assessments.
References
Livingstone, G (2023). Measuring and Attaining Sustainable Lubrication. Precision Lubrication Magazine. https://precisionlubrication.com/articles/sustainable-lubrication/
Bieker, G. (2021). A Global Comparison of the Life-Cycle Greenhouse Gas Emissions of Combustion Engine and Electric Passenger Cars. The International Council of Clean Transportation. European Climate Foundation and the Climate Imperative Foundation.
Fehrenbach, H. (2005). Ecological and Energetic Assessment of Re-Refining Used Oils to Base Oils. Institut fur Energieund Umweltforschung GmbH (IFEU), a study commissioned by GEIR-Groupement Europeen de l’Industrie de la Regeneration.
Fluitec. (2022). Life Cycle Assessment. Bayonne, NJ: Fluitec International, LLC.
Life Cycle Assessment. (Kein Datum). Von Wikipedia: https://en.wikipedia.org/wiki/Life-cycle_assessment
Abgerufen Muralikrishna, I. a. (2017). Life Cycle Assessment – An Overview. Science Direct Topics. Environmental Management Science and Engineering for Industry.
Raimondi, A. e. (2012). LCA of Petroleum-Based Lubricants: State of Art and Inclusion of Additives. The International Journal of Life Cycle Assessment, DOI: 10.1007/s11367-012-0437-4. 987-996.
Taylor, R. e. (2005). Lubricants & Energy Efficiency: Life Cycle Analysis. Life Cycle Tribology.
(2017). Tribology Opportunities for Enhancing America’s Energy Efficiency. Advanced Research Projects Agency – Energy at the US Department of Energy.
Wernet, G. B. R. (2016). The Ecoinvent Database Version 3 (part I): Overview and Methodology. The International Journal of Life Cycle Assessment, 1218-1230.
Young, J. E. (2020). Energy Efficient Industrial Lubricants: Reducing Energy Consumption with Industrial
Lubricants. Pennsylvania Statewide Technical Reference Manual – Work Paper.
A portion of this article was previously published in Precision Lubrication.
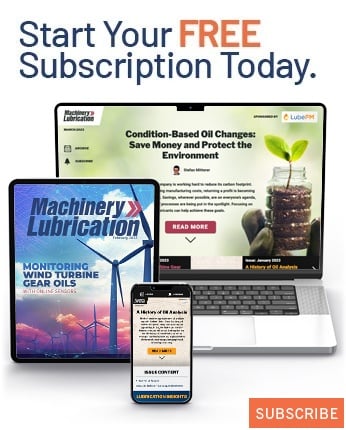