"After reading an article recently about the dangers of electrostatic discharges in oil, we wondered how you can detect discharge problems at turbine oil filters. Is there a simple method for doing this?"
The simplest method for determining spark discharge problems is simply to listen for a clicking or ticking sound in the area around the filter or near the reservoir. Of course, it would be better to be proactive and work to eliminate the problem at its source rather than detecting the spark discharge problems.
Most turbine oils in use today are Group II oils, although some situations may call for Group III oils. Due to the level of refining, these oils have a much lower level of conductivity. Keep in mind that as an oil's conductivity decreases, the potential for electrostatic discharge increases. The charge develops from friction between the oil's molecules as well as between the oil and the surface of the piping, reservoir, filter housing, etc.
Among the contributing factors include the piping diameter being too small for the system, which increases flow velocity; a lack of polar additives; insufficient grounding of the system; low oil level and entrained air in the system; and the pursuit of cleaner oils, which often leads to a greater intensity in the filtration of the oils. The base oil, additives and polarity also affect an oil's conductivity.
Some oil analysis laboratories are equipped to perform an electrical conductivity test (ASTM D2624). While this test method is intended primarily for aviation fuels, it has been proven effective for lubricating oils as well.
An oil's conductivity is measured in picosiemens per meter (pS/m). For reference, a picosiemen per meter is equal to 10-12 ohms. Studies have shown that if an oil's conductivity is more than 400 picosiemens per meter at 20 degrees C (68 degrees F), there is little to no risk of electrostatic discharge.
You may also wish to incorporate ultrasonic or vibration equipment to alert you of spark discharges. This type of equipment offers several advantages, but as mentioned previously, the best approach usually is to be proactive and focus on the root cause of the problem. Special filters, system modifications or a different oil formulation may help minimize the charge potential or even keep a charge from occurring.
Remember, by controlling the oil's conductivity, it is possible to prevent electrostatic discharges and thereby eliminate the need to detect them.
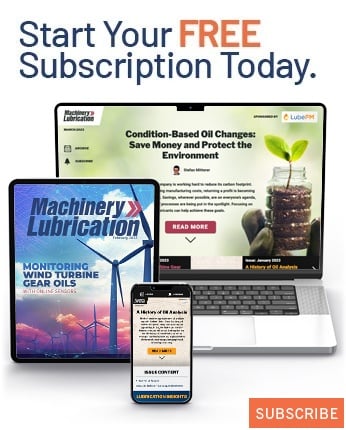