The significance of properly storing oil drums cannot be overstated when it comes to lubrication and long-term machine reliability. The correlation between unprotected oil drum storage and eventual machine failure is undeniable. Within these seemingly innocuous containers lies a potent source of contamination, harboring dirt and moisture that can wreak havoc on machinery.
Despite this knowledge being common among professionals, the urgency to address it often falls by the wayside. Unlike the proverbial squeaky wheel that demands attention, the neglect of proper oil drum storage can easily go unnoticed. Compounding this issue is the challenge of retroactively pinpointing storage conditions as the root cause of machine failure.
Consider this: How often do we trace a bearing failure back to the conditions in which its originating oil drum was stored?
The truth is that the repercussions of leaving oil drums unprotected set the stage for failure right from the start. It's not just about the oil becoming riddled with sludge and degradation products; rather, it's the gradual deterioration of crucial lubricant properties. From shortened oxidative oil life to compromised friction and wear protection, insufficient foam suppression, water emulsification, and impaired filterability — the consequences are manifold.
What makes this situation particularly insidious is how these early-stage deficiencies obscure their connection to eventual machine failure. When lubricant performance issues manifest during service, it's all too easy to lay blame on the manufacturer or chalk it up to a bad batch of oil.
However, the reality often reveals a different story — a story of oil inadequately stored.
Fortunately, solutions exist for those willing to take proactive measures. Implementing simple safeguards like ingress-prevention devices, such as the Air-Lock by Luneta, not only preserves oil integrity but also translates into substantial cost savings down the line. It's time to recognize the critical role of proper oil drum storage in safeguarding machinery performance and longevity.
Typical Oil Degradation
Oil doesn’t last forever and degrades over time because of what it’s exposed to. Water, Heat, Air, and catalytic Metals (WHAM) are all examples of contaminant exposures that directly degrade the oil. Oxygen and moisture can lead to oxidation and hydrolysis, respectively. Increased temperatures expedite these chemical reactions (due to the Arrhenius rate rule). And one of the most prominent drivers of oil oxidation is the presence of catalytic wear metals and water in the oil together. All these are bad things that lead to machine failure.
When oil in a machine starts to oxidize, it may appear dark and sludgy if you check the sight glass, for instance. An even better way to spot this problem is through oil analysis, which can detect changes like increased viscosity and acid levels.
When oil is freshly made, it's at its peak condition, with all its base oil quality and additives intact. However, as it's exposed to factors like heat, air, and moisture (WHAM), its oxidative life starts to decline. This happens because the oil's antioxidant additives are used up through decomposition. This process can happen anywhere, whether it's during storage, transfer, or while in use.
Oil analysis indicators are typically measured while the oil is in service. However, if the oil is stored in poor conditions, its initial condition may already be compromised. This could mean its oxidative life, or the level of additive depletion, might start off lower than expected, which can further weaken it from the start.
How much the oil deteriorates depends entirely on how much WHAM the oil is exposed to in storage and for how long. Unfortunately, drums are not made to fully protect the oil and can allow contaminants and moisture to seep in over time through daily thermal syphoning effects.
Even small temperature changes can draw in contaminants and moisture through the gaps around the bungs. And this is not just 55-gallon drums storing oil, but any fluids being stored in a typical drum.
Additive Separation
As mentioned above, additives in oil can break down as they shield the base oil from contaminants. This is mainly done by antioxidants. Additionally, some additives are naturally drawn to contaminants because of their chemical properties, known as polarity, which makes them naturally bond with other polar materials.
These additives can “hitch a ride”, so to speak, on particles or water, and move out of the main oil supply. Examples include metal deactivators and dispersants (which cling to particles) and emulsifying agents (which attach to water). Over time, these additives may separate out or get filtered during oil purification processes.
All of these issues can be avoided by ensuring that oil remains clean and dry, whether it's in use or in storage.
Oil Contamination in Storage Leads to Costly Negligence
Now that you have a fundamental understanding how oil can degrade and additives can deplete if contaminants are allowed to sit in the oil (either in storage or in-service), let's delve into how storing drums without protection can lead to costly oversights:
- The Cost of Machine Wear and Tear: The cascade of damage initiated by unfiltered particles is alarming. Each ingressed particle acts as a progenitor of further particulate generation, a process that exponentially escalates wear and tear. The stark contrast between systems with high-quality filtration and those without illustrates the critical role of proactive contamination exclusion.
- The Cost of Moisture Contamination: Moisture's insidious effects on oil and machinery are well-documented, with even minimal water presence leading to drastic reductions in component lifespans. The economic argument for moisture exclusion, particularly through simple solutions like Air-Lock, is irrefutable when considering the costs of damage and downtime.
- The Cost of Reactive Measures: While oil filtration and dehydration are essential, they represent a significant financial outlay. These reactive measures, although necessary, are far more costly compared to the preventative exclusion of contaminants. Keeping contaminants out in the early stages of oil storage with maintenance-free strategies presents an economically sound alternative.
- The Cost for Oil Consumption and Operational Costs: Contamination not only shortens oil life but also exacerbates oil consumption and leakage issues, such as through seal damage. By minimizing contaminant ingress and maintaining cleaner oil, many companies have reported more than an 80-percent reduction in leakage. This directly contributes to reduced oil consumption, fewer oil changes, and lower operational costs.
- The Cost of Poor Performance and Increased Energy Consumption: The impact of contamination extends beyond wear and machine failure, affecting energy consumption and machine performance. If machines are allowed to run with contaminated oil, there is sluggish or erratic machine function. This is the case with hydraulic pumps and actuators that lose volumetric efficiency due to contaminant-induced wear. All the while, there is increased energy consumption from friction and wear.
Conversely, clean and dry oil — free from the burdens of particulate and moisture-induced wear — ensures optimal efficiency and extends the long-term lifecycle of machinery.
Your Action Item: Stop Contamination Early
You’ve heard it all before: get out of the reactive maintenance mode and embrace a proactive approach. One significant step in this direction is ensuring the cleanliness of oil drums during storage using effective technologies. While there may be a small initial cost involved, the long-term benefits in terms of economics, operations, and the environment far outweigh it.
Taking action to protect oil drums from contaminants demonstrates a forward-thinking approach to maintenance, particularly as we strive for excellence in our practices. Implementing protection devices like the Air-Lock not only reduces the risk of machine failure but also fosters a culture of responsibility among those managing lubrication. This simple proactive measure sets a standard for cleanliness throughout the oil's lifecycle, from storage to dispensing and usage in machinery.
By prioritizing contaminant exclusion in oil storage, we not only improve machine performance but also signal our commitment to operational excellence and sustainability. It's time to stop hesitating and start taking decisive steps to safeguard the health of our machinery through smarter lubricant management practices.
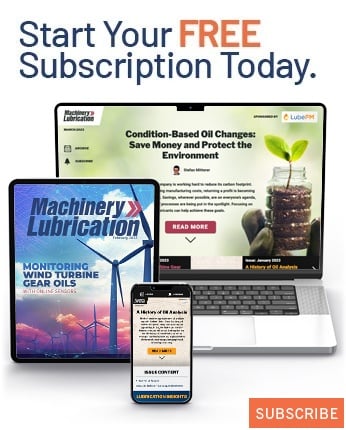