Having spent a good portion of my career around heavy machinery, both in the military and later in the civilian world, I’ve come to realize one critical fact: the tools you use matter just as much as the skills you have.
When it comes to maintaining the reliability of machines, especially in environments where downtime is costly, having the right equipment is essential. This is particularly true in lubrication management, which can make or break the longevity of your machinery.
If you want to avoid costly breakdowns and ensure everything runs smoothly, you need to have the proper tools, like color-coded grease guns with meters and color-coded top-up containers. These aren’t just fancy add-ons; they are key pieces of equipment that can prevent serious issues like cross-contamination and system failure.
Cross-contamination in lubrication is no joke. You might think, “Grease is grease,” but it’s not that simple. Different greases and oils have specific properties suited for different machine components. Some are designed for high temperatures, others for high loads, and mixing the wrong kinds can result in anything from excessive wear on parts to outright equipment failure.
Cross-contamination happens when lubricants get mixed due to improper handling, storage, or maintenance procedures. This can lead to chemical reactions that break down the lubricant’s ability to do its job, which is to reduce friction and wear and protect the parts.
The consequences? Premature bearing failure, reduced machine life, and ultimately, costly repairs and unscheduled downtime.
The Importance of Color-Coded Systems
In both military and industrial settings, confusion or misapplication can lead to major issues. One simple but effective solution to prevent mistakes in lubrication is a color-coded system for grease guns and top-up containers.
Different types of grease are formulated for specific applications, and mixing them up can cause serious damage. This system simplifies the job for the lube tech by ensuring there is no confusion between lubricants meant for different applications.
For example, if you have three different types of grease in your shop—say, one for high-temp bearings, one for low-speed, high-load components, and another for general-purpose lubrication—you can assign each one a specific color. By using color-coded grease guns, lube techs can quickly identify which tool is meant for which grease type, eliminating the risk of applying the wrong lubricant to the wrong part.
The same logic applies to top-up containers. Color-coded containers not only make it easy to identify which lubricant goes where but also help maintain cleanliness. These containers are often sealed to prevent dust, dirt, and moisture from contaminating the lubricant, which is critical in environments where heavy machinery operates.
Contaminated lubricant can lead to accelerated wear, reduced performance, and eventual failure of machine components. The Noria Ascend Chart emphasizes the importance of controlling contamination in lubrication management, and color-coded systems are a practical way to meet this standard.
Preventing cross-contamination is not just good practice, it’s a cost-saving measure that aligns perfectly with the Ascend Chart’s focus on reducing overall operational costs through efficient maintenance.
Grease Guns with Meters: Precision Matters
In my experience, precision is everything. Whether you’re tuning a motorcycle or maintaining a massive industrial machine, guessing doesn’t cut it. One of the most effective tools for lubrication is a grease gun with a built-in meter.
Over-lubrication is more common than people realize, and it’s just as bad as under-lubrication. Over-greasing can blow out seals or create pockets where contaminants can collect, leading to breakdowns. On the flip side, under-greasing causes parts to wear out more quickly.
A grease gun with a meter removes the guesswork by delivering the exact amount of lubricant required. It’s like using a torque wrench—precision is key to preventing damage. To take it a step further, the Machinery Lubrication Bearing Grease Calculator is an excellent online tool that helps you calculate the precise amount of grease needed for your bearings based on their size and operating speed. This tool is especially useful in making sure you don’t under- or over-grease, ensuring optimal bearing performance.
By combining a grease gun with a meter and tools like the bearing grease calculator, technicians can follow maintenance procedures and guidelines down to the last detail. This precision ensures the right balance, reducing wear and optimizing machine performance. This aligns with the Noria Ascend Chart’s focus on precision, which ultimately extends the life of critical machine components and prevents expensive downtime.
The Real Costs of Cross-Contamination
Mixing lubricants doesn’t just lead to mechanical failures; it also introduces safety risks. Machines running on compromised lubrication are more prone to overheating, which can cause fires and catastrophic equipment failure. In industries where heavy machinery operates 24/7, safety is paramount, and the cost of getting it wrong is more than just financial.
The upfront investment in quality tools and systems is minimal compared to the potential costs of machine failure, unplanned downtime, and safety incidents. In the long run, preventing cross-contamination not only saves money but also enhances operational safety.
Cost Benefits of Reliable Lubrication Practices
When it comes to maintenance, cutting corners never pays off. Reliable lubrication practices—using color-coded grease guns, meters, and top-up containers—lead to measurable cost benefits. Proper lubrication management reduces the frequency of repairs, extends machine life, and minimizes downtime. The savings from preventing unplanned breakdowns far outweigh the cost of investing in a disciplined system.
Following this strategy, businesses can expect fewer breakdowns, extended equipment lifespans, and better overall performance. Ultimately, prioritizing the right tools and following best practices leads to fewer emergency repairs and more predictable, reliable machine operation.
Conclusion
The role of proper tools in machine reliability cannot be overstated. Simple solutions like color-coded grease guns with meters and organized top-up containers prevent cross-contamination, ensure proper lubrication, and contribute to machine longevity.
The Noria Ascend Chart serves as an essential guide for companies looking to improve machine performance and reduce maintenance costs. In the end, investing in the right tools isn’t just about avoiding mistakes—it’s about safeguarding equipment, ensuring safety, and optimizing long-term operational efficiency.
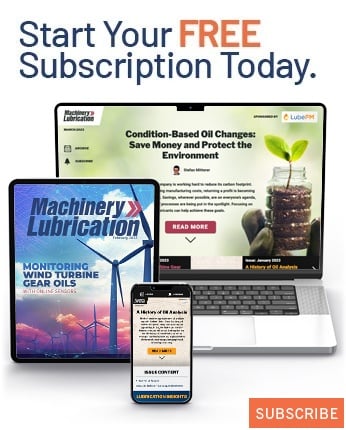