Grease is comprised of three components – oil, a thickener, and additives.
Thickeners impact grease capability and compatibility. Compared to oil, greases are better for leakage control and sealing against contaminants, which are one of the leading causes of mechanical failures.
Grease can remain in equipment for extended periods of time under a variety of conditions. However, grease is difficult to drain and doesn’t circulate, meaning if the grease is contaminated while in service, the particles will remain in place and cause significant damage to the bearings.
Additionally, rolling element bearings operate in an elastohydrodynamic regime. According to Machinery Lubrication, this regime occurs when the lubricant comes between surfaces where a small contact area and a rolling motion exist, such as ball bearings.
These conditions create high-contact pressures – sometimes hundreds of thousands of psi – meaning that if water or particle contaminants are present, they become incredibly destructive.
Contamination Control Strategies
The most commonly used strategies found in contamination control programs are a combination of:
- Preventing contaminants from ever entering
- Removing contaminants through filtration systems
It is possible to remove contaminants from oil once introduced by using filtration systems. However, it is always advisable to minimize the contaminants from entering the system to avoid lubricant degradation and additive depletion. It will always cost more to remove dirt than it is to keep it from entering in the first place.
In contrast, once contaminants are present in grease, they are nearly impossible to filter out. This means the only option for a grease contamination control strategy is to prevent contaminants from ever entering.
Unfortunately, it’s common for end users to unintentionally expose grease drums to contaminants. This seriously affects the quality of the grease and the machine parts. One simple and sometimes overlooked solution is a follower plate.
What is a Follower Plate?
A follower plate is a tool capable of pumping grease directly from the drums. In this process, a pump creates a vacuum that pulls the follower plate to the bottom of the drum, collecting the grease along the way.
The follower plate has four core benefits:
- Keeps the grease clean and preserves its characteristics.
- Compresses the grease, preventing air pocket formation and pump cavitation.
- Helps collect grease from the bottom of the drum, which would otherwise remain stuck.
- Improves the pump’s overall capabilities.
Left Drum No Follower Plate; Right Drum With Follower Plate
Image Source: Tecalemit Australia
Benefit 1: Keep the Grease Clean
Keeping grease clean should be a crucial objective for every workshop and technician.
The purpose of keeping grease clean is to safeguard the longevity of the lubricated parts or systems. This is because the lubricant film separating the contacting surfaces—whether rolling or sliding—is usually very thin, anywhere from less than 1m up to 10m. Particles larger than the film thickness can be detrimental to the smooth running and service life of the bearing.
Additionally, grease cannot be effectively filtered after formulation. There are two main reasons for this:
- Filtration requires the fluid to flow and mix to help remove contaminants uniformly. Because grease doesn’t possess these characteristics, filtration is not effective.
- Standard filtration methods generally disrupt and break down the grease’s thickener, which is designed to give the grease its consistency and keep the grease in place when in service.
Benefit 2: Compress the Grease
If grease is left open and not compressed, air pockets can form. These air pockets can disturb the lubrication system and damage the pump through cavitation – the mechanism by which vapor bubbles (cavities) in a fluid grow and collapse due to local pressure fluctuations.
Benefit 3: Help Collect Grease
When a follower plate isn’t used, the drum can’t be completely emptied, leading to wasted grease. In some cases, there can be as much as 5 kg of waste per 180 Kg drum.
Extended to the number of grease drums consumed in a workshop, this grease waste can be enormous and justify the purchase of a follower plate.
Benefit 4: Improve Pump Capabilities
When grease isn’t compressed, a facility can experience several challenges, including:
- Affecting the flow of the grease.
- Affecting the life of the pump.
- Under-lubricating machines.
Selecting a Follower Plate
The diameter of the follower plate depends on the diameter of the grease packaging. The mass of the plate is also a good criterion since the compactness of the grease will rely on the pressure exerted on it.
The consistency of the grease also plays a role in selection; for example, an NLGI 1 grease may need a lighter follower plate than an NLGI 3 grease.
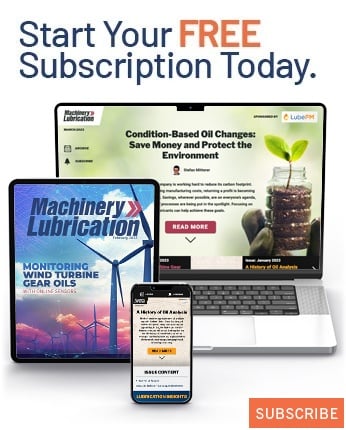