Visiting the doctor and receiving blood test results can reveal the overall health of a person's body. In much the same way, the quality and condition of oil are telling signs of a machine’s overall health. Like medical lab results, an oil analysis report helps maintenance personnel understand how well a machine is functioning.
For oil analysis, an oil sample is taken, sent to the lab, analyzed, and a report is generated. When performed correctly, oil analysis is highly effective in determining the health of equipment and its lubricants. A successful program can help:
- Determine when the oil needs to be changed
- Predict impending machine failure
- Diagnose equipment issues
Over time, the insights gained from an effective oil analysis program can enhance a company's productivity and competitiveness while increasing profits. Unfortunately, many companies are not seeing the full benefits because they do not fully understand the importance of the first step in oil analysis—collecting a reliable, representative oil sample.
The Reliable Base Layer
Reliable oil samples are key to a successful oil analysis program. A reliable oil sample should be repeatable, data-rich, and clean. It should be taken while the machine is running, from the oil's live (active) zone, and from the same location every time. These practices save money by avoiding the costs of:
- Sample retakes
- Excessive repair costs due to inaccurate results
- Unnecessary downtime or lost production
Without a reliable oil sample, the analysis and trending will be undependable, and any action taken based on that report could be less effective or even counterproductive. Taking a proper sample may seem simple, but many companies still use less-than-best-practice sampling. These practices can ultimately result in companies incurring thousands of dollars in additional maintenance costs.
How Reliable Is Your Foundation?
Years ago, I walked into a lab and was shown a gearbox oil sample that had recently arrived from a steel manufacturer. It looked just like the figure below:
Figure 1. A recreated example of the steel manufacturer’s oil sample
Upon examination, it was evident that no oil was present. This is because the sample was drawn from the drain valve of a gearbox, which had collected a large amount of free water.
Although some could argue the sample was “good” because it uncovered a water contamination problem, what if it had also shown an increase in ferrous wear debris? The company would have shut down the equipment for a component replacement and found no abnormal wear.
Below is an example of the associated costs from the false positive report:
Note: These figures are estimates based on customer cases and are intended for demonstration only. Costs may vary.
Unfortunately, pulling an oil sample from the drain valve is all too common. Although the sample is collected from the same location every time, it does not originate from the active zone. Because the machine’s drain or sump is often filled with historic bottom sediment, samples taken from there can show falsely elevated wear metal or contamination levels because wear particles, contaminants, and water settle to the bottom.
These reports can lead to lost productivity and elevated maintenance costs from attempting to resolve a problem that never existed. Additionally, through drain sampling, maintenance teams risk introducing external contaminants into their system or sample.
Besides drain sampling, another standard sampling method is drop-tube sampling. Here, technicians open their equipment, insert tubing, and suction out the oil with a vacuum pump. It's simple and low-cost. However, it does not always lead to the most reliable oil samples. Due to the nature of flexible tubing and internal obstacles within the machine, inserting the tubing into the same spot and at the same depth consistently is challenging.
Western University conducted a study to investigate the inconsistencies of drop-tube sampling results. Three sampling methods were used to draw oil samples from the same piece of machinery for one week:
- Method A (Push-button sampling valve)
- Method B (Sampling valve with tube)
- Method C (Drop-tube and vacuum pump)
They found that “Method A would be preferred over Method C because Method C has high variability in measurements (or resampling Method A has the least variability in particle counts). In addition, Method C gave a wide result of particle counts when resampled.” In total, drop-tube sampling can produce false negative sample results, harming an oil analysis program.
Consider this scenario: A key production line has slowed, and the gearbox is noisy. An oil sample is taken using the drop-tube method; the oil analysis report returns with no problems indicated. Nothing was done, and a complete failure occurred because the company missed the chance to replace a seal on the axle. This is what the cost comparison looked like:
Note: These figures are estimates based on customer cases and are intended for demonstration only. Costs may vary.
These sample results occurred because the sample was taken from the top of the oil level, where the cleanest oil resides, not near the “active zone.”
Cross-contamination can also lead to unreliable oil samples from drop-tube sampling. I had a customer using drop-tube sampling for the equipment on his ferries. In his case, they were sampling hydraulic units, coolants, engines, and gearboxes.
The oil analysis reports consistently returned positive for coolant. The engine system was flushed and inspected, costing thousands of dollars. Eventually, they discovered that the technicians had sampled the ferry engines with the same vacuum pump and tubing as the coolant, resulting in residual coolant in the engine sample.
Creating a Base Layer for Trending
The best method for reliable oil samples is dedicated oil sampling valves, which minimize the data disturbances from other sampling methods. Sampling valves help obtain reliable, convenient, safe, and quick oil samples from a system, making it possible to take oil samples from running machines safely while reducing the chance of introducing contaminants to the sample or machine.
The ferry company above installed dedicated sampling valves on its ferries to resolve its cross-contamination issues.
“We installed all the valves and are now using that method. We had a previous dirty coolant sample on one main engine. Draining and flushing this system was a big deal, costing us over $3,000. We had another bad sample come in using the old method of taking samples. I took a new sample using the installed valve, and it came back clear, with no need to flush.”
Not only did he save a flush on his engine, but he also extended the drain intervals on his hydraulic oil. "Hydraulic oil change came due — 130 gallons of ISO 68. Oil analysis returned normal, so we avoided the cost and mess of a big oil change."
Note: These figures are estimates based on customer cases and are intended for demonstration only. Costs may vary.
Installing sampling valves isn’t difficult, but a proper sampling location must be determined. This can vary between equipment, but oil samples should be taken dynamically when possible with a valve installed at a point within the system with the most active fluid. This ensures the functioning fluid is always taken from the same point within running equipment, avoiding any settling effects of particulate, moisture, or wear metals.
For Pressurized Equipment
A port located pre-filter on a circulating lubrication or hydraulic return line is often the best place to start. Mounting hardware can modify existing systems to include a sampling port without drilling and tapping new locations. For example, inline connectors can add a valve to an existing return line (Figure 2).
Figure 2. An inline connection on a hydraulic power unit
In Figure 2, reliable samples are gathered by pushing a button. If samples cannot be safely obtained directly from the valve, short extensions to a safe location can be made (Figure 3).
Figure 3. A remote-access installation on an engine
For Non-Pressurized Equipment
Common installation locations for sampling valves on gearboxes and reservoirs are within the existing:
- Vents
- Drains
- Sight level ports
Sampling tubes are recommended to remove the oil sample from the bottom and side sediment. If installed on a drain port, bend the sampling tube toward the active zone. If installing on a side or level port, bend the tube toward the oil level. In most cases, a 12-inch tube is the perfect length to reach the oil in the active zone.
In addition, all sample ports should be flushed prior to extracting an oil sample. The appropriate volume to flush is 5 to 10 times the deadspace volume, which is impacted by the length of the tubing used.
Figure 4. An example of a sampling tube installed on a reservoir
Both installation examples allow companies to collect reliable samples necessary for starting to baseline and trend the oil health of equipment. However, reliable oil samples alone won’t allow an oil analysis program to reach its full potential.
Incorporating maintenance techniques such as visual oil analysis and desiccant breathers can impact the overall success of a conditioning monitoring program. Several products combine oil sampling with visual analysis, filtering, and particle protection.
Adding visual oil analysis and sampling to a program can help detect problems before a scheduled oil sample. Visual oil analysis tools, including sight glasses and level gauges, assist in detecting contamination and other oil problems early. They continuously monitor the oil's clarity, color, sediment, and water contamination. For example, a bottom sediment and water (BS&W) bowl can be used to find the presence of water before it impacts a machine and before the next scheduled sampling time (Figure 5).
Figure 5. An example of combining sampling with a BS&W bowl and a level gauge
Desiccant breathers offer a front-line defense against particle detection. As air is drawn into the equipment, the desiccant filter elements remove particles while the beads stop harmful moisture. Additionally, while in service, the desiccant beads attract moisture from inside the equipment reservoir, actively drying the equipment (Figure 6). Many desiccant breathers’ beads also change color when saturated with moisture, which provides useful data that can be incorporated into a plant’s visual inspection process.
Figure 6. Example of combining sampling with a desiccant breather on a hydraulic reservoir
Portable filtration units can hook up to quick connects on drain/breather mount (adapter) options for in-service filtration without shutting down (Figure 7).
Figure 7. Example of combining sampling with a desiccant breather and in-service filtering on a gearbox
Besides adding simple maintenance techniques, integrating an oil analysis program with other condition monitoring technologies, such as vibration analysis, can reduce unsuspected breakdowns.
Testing and Caring for New Lubricants
The next step in complete lubrication management is proper testing and care of incoming oil. Oil is blended, inspected, transported, packaged, and labeled by humans, and humans have one thing in common—they make mistakes.
Because of these potential errors, facilities should always test oil to verify its cleanliness before use. It is less expensive to sample incoming oil than to repair a failure and face unplanned downtime costs. Sampling incoming oil also helps establish an oil analysis baseline that reflects the oil’s condition before entering service. This information assists in creating subsequent reports and monitoring for changes in the oil’s properties.
Because new oil doesn’t equal clean oil, plant personnel can inadvertently add new lubricants, assuming their cleanliness, to a system without realizing the potential for introducing contaminants. Lubricants should be filtered with the correct filter elements before entering the equipment. Periodic filtration and agitation should also be performed to prevent additive settling and maintain cleanliness codes.
In addition, stored oil must also be monitored. Proper sampling methods and techniques should be used for sampling oil drums and totes. For example, drums and totes are often stored in areas where significant temperature variations are possible, causing condensation. This can lead to a “new” oil containing more water than the maximum recommended amount.
What’s Next?
Like the new technologies in the healthcare industry that monitor different aspects of the human body, new sensors and technologies are being developed in the condition monitoring field. These innovations are adding a new layer to total lubrication management. We will have to stay tuned.
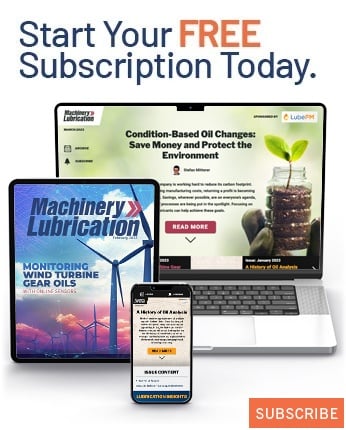