Deeter Foundry, located in Lincoln, Neb., produces gray iron castings used in manhole frames and covers, storm sewer inlet frames, grates and curbs, trench grating and tree grates. The foundry has enjoyed the benefits of using desiccant breathers on its machines for more than two years.
The foundry began using desiccant breathers for two reasons. First, during the summers, water contamination increased in the hydraulic reservoirs. Second, the foundry found it more difficult to maintain target ISO cleanliness codes throughout the plant.
It has always been the theory of the author that machines are like humans and should be treated as such. With this approach, the Deeter Foundry team recognized that like people, equipment must also breathe. During normal operation of the hydraulic units, the oil levels in the reservoirs rise and fall, much like the human lungs when breathing.
Moisture from the air accumulates in the reservoir when the machine takes in, or “breathes in” humid air. The dirt, which comes from the clay and sand used for molding, combined with humidity and the heat generated from pouring molten gray iron, created a less than ideal environment for contaminant-sensitive hydraulic components.
Deeter Foundry wanted to achieve two goals: to lower the water concentrations and reduce the amount of silicon (dirt) in the hydraulic fluids.
In the beginning, they reviewed different fill caps, breathers and vents. Nothing filtered the air well enough. To combat the water problem in the oil, a superabsorbent filter was used to remove the water from the oil. To reduce the water concentration in their hydraulic units, the author used a water gel filter.
This type of filter has media in it which removes water. He consulted a filter manufacturer, providing information on each of the hydraulic units, such as size of unit, ppm of each unit, and the base oil sample. With this information, the filter manufacturer put Deeter on a program to change out the water gel filters.
Upon discovering that using spin-on oil filters worked as breathers, they were able to maintain the oil ISO cleanliness code and kept water ppm within the target range. However, the spin-on oil filters were expensive.
The additional cost of the superabsorbent filters made maintaining the cleanliness code an expensive proposition. This is when desiccant breathers became a reasonable option.
Desiccant breathers use filter media to remove particles greater than three microns, and a silica-gel desiccant to remove moisture from the air entering the hydraulic oil reservoir and contaminating the fluid.
This approach enabled Deeter to achieve and maintain its target moisture and dirt levels through six months of use, and without the use of the superabsorbent oil filter element. Based on this success, the foundry upgraded other systems to incorporate desiccant breathers.
The teams started by installing desiccant breathers on the large gearboxes. Within 90 days, oil analysis reports showed a decrease in silicon levels. The ISO cleanliness levels were set at 17/15/13 - levels which could not be achieved previously. After installing the breathers, the teams saw a reduction in silicon in the first oil sample taken.
Not all machines were immediately converted to desiccant breathers because at the time, size options were limited. Desiccant breather manufacturers now offer several different sizes.
Today, Deeter Foundry has desiccant breathers on many types of applications, including air compressor separator exhaust, fan bearings (outside), gearboxes, bulk hydraulic oil totes, lube storage racks and all the hydraulic units.
Some may ask, “Why use desiccant breathers?” My response is “Why not?” A desiccant breather removes both moisture and dirt from the air the machine breathes. This is true with equipment of all sizes and most locations. Breathers are sized according to the required cubic feet per minute (cfm) of air exchange for each machine application.
A filter distributor can help answer these questions. Another commonly asked question is “How do I know my breather is still working?” The desiccant beads in the breathers change color as they become saturated with moisture, indicating that the unit is spent.
For the true skeptic, a trial run on a piece of equipment with trendable contaminant (moisture and particles) is recommended. This should prove or disprove the desiccant breather performance and effectiveness. The Deeter Foundry plant has more than 50 desiccant breathers installed on a wide variety of equipment. Desiccant breathers are now a part of the yearly maintenance budget.
While it was a change in thought and concept, Deeter Foundry has found desiccant breathers to be a vital part of the maintenance and reliability optimization process. The plant realizes the benefits of desiccant filters every day.
Many of the obstacles encountered in the beginning have been addressed. Such changes are not possible without the support of senior management and more importantly, the buy-in from your technicians. Good documentation and a continuing education can spell success for any program.
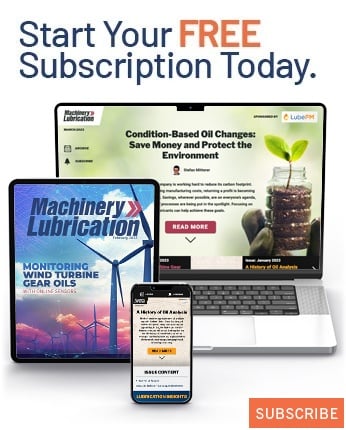