You've heard the expression: There are only two things in life that are certain, death and taxes. Some have suggested that the same applies to machinery. We all know that if a machine generates a profit, taxes will be levied on that profit. But how about death? Is machine mortality also inevitable?
Let’s take a closer look. According to Massachusetts Institute of Technology professor emeritus and luminary tribologist Ernest Rabinowicz, there are three things that cause machines to lose their usefulness:
obsolescence, accidents and surface degradation. Without question, obsolescence is fundamental to the evolution of engineering and technology. The old must make way for the new. Yet some inventions have long life cycles, the grease fitting for example. Its design has changed little since
Oscar Zerk invented it in the early 1920s, yet is still widely used today. The automobile, on the other hand, is dynamic and in constant flux. While the classics cars live on into perpetuity, most automobiles face practical obsolescence long before they are functionally inoperable.
Accidents and other forms of human agency events can put a machine in imminent danger as well. Two identical machines working in identical work environments but operated by two different individuals can exhibit sharply dissimilar reliability and operating life spans.
The dissimilarities are typically operator (human) induced. Human agency failures also apply to errors in machine design and manufacturing. In this same category are accidents caused by acts of God (tornadoes, earthquakes, etc.) and other natural and random events.
Rabinowicz’s third reason why machines lose usefulness deals with the world of tribology (study of wear, friction and lubrication). He describes this as surface degradation, which can be divided into chemical degradation (corrosion) and mechanical damage.
The protection of a machine’s internal surfaces from chemical damage (20 percent) is largely affected by controllable conditions. Consider the following causes of chemical damage and the potential for their control or intervention by maintenance practices:
- Lubricants with ineffective or distressed barrier-film corrosion inhibitors
- Lubricants prone to rapid oxidation (acid producing)
- Crankcase lubricants with impaired alkalinity reserve (acid neutralizing)
- Overextended oil change intervals
- Oil contamination by water and/or acids from the work environment
- Uncontrolled growth of biological contamination
- Moist headspace of tanks, sumps and other lubrication compartments
- Exceedingly high operating temperatures
- Improper use of chemically aggressive antiscuff (EP, etc.) additives
- Improper preservation of stored or laid-up equipment; protection from moisture and corrosion agents
- Lubricants that are incompatible with seals, process chemicals, machine metallurgy or surface treatments.
Mechanical surface degradation is subdivided into abrasion, fatigue and adhesion (for simplicity, less common wear modes were excluded). Let’s take a closer look at these three surface-destructive wear modes that correspond to roughly 50 percent of why machines are removed from service. More specifically, let’s examine the extent to which this internal destruction can be controlled, or even arrested.
Two-Body Abrasion
Perhaps 20 to 30 percent of all abrasive wear is two-body. In this case, two surfaces (bodies) are sliding against each other, such as a shaft rotating within a stationary journal bearing. The asperities (high points) of the harder surface (shaft) tend to plow or gouge the softer surface like a file.

Two Body Abrasion
Can this be controlled? Not in every case, but in the majority of cases, it probably can. Ample oil film generation is all that’s needed. This can be designed into the machine by proper selection of bearing configuration and size, for instance.
Operating temperature and lubricant viscosity impact film thickness as well. So too, important mechanical conditions such as misalignment, unbalance, overloading, dry starts and sudden coast-downs play a vital role and are generally controllable.
Three-Body Abrasion
When a solid foreign body is allowed to become interposed between two surfaces in relative sliding motion, a more severe and common form of surface destruction can occur. This foreign body, of course, is a hard particle in the general size range of the oil film thickness. These particles, typically invisible to the unaided eye, have the potential to be massively destructive.
A particle of the right size can function like a microscopic cutting tool to produce furrows in the opposing surface. However, unlike two-body abrasion in which the soft surface plays a sacrificial role, in three-body abrasion the particle can inflict equal damage on both hard and soft surfaces. Some researchers assert that three-body abrasion is responsible for as much as 80 percent of all wear in machinery.
Can three-body abrasion be controlled? Absolutely. The vast majority of the microscopic particles originate as terrain dust, previously airborne. When airborne contaminants are allowed to become ingested into the machine and mixed with the oil or grease, human agency failure occurs. It’s human-agency because these wrecking-crew particles are not a part of the machine’s original bill-of-materials.
They were allowed to ingress during operation, often due to neglect and poor maintenance practices. Over time, an oil can become more of a honing compound than a lubricating medium. Much has been published on how to exclude contamination from machine lubricants and hydraulic fluids.
Fatigue
Fatigue is a broad term that can relate to bending fatigue (for example, a gear tooth) on a macro scale or contact fatigue (for example, pitting) on a micro scale. The latter is the dominant case and occurs typically in rolling contacts such as at the pitch line of gear teeth and the load zone of rolling element bearing raceways. It typically initiates as micro pitting and then advances to macro pitting. A final stage would be large destructive spalls.
Contact fatigue is the greatest when loads are permitted to concentrate on surface asperities, shoulders of dents, and where particles bridge surfaces under load. Surface fatigue is influenced by numerous conditions including surface roughness, surface hardness, viscosity, fluid pressure-viscosity coefficient, operating loads and speeds, moisture contamination and particle size distribution.
With few exceptions, most of these conditions are within the realm of control, either at the machine design stage or at an operating and maintenance stage. One large rolling element bearing manufacturer has stated that its bearings can have “infinite life when particles larger than the oil film are removed from the oil.”
Adhesive Wear
Unlike surface fatigue that takes time to initiate, adhesive wear can occur immediately. Under severe boundary sliding conditions, surfaces of like-metals can literally spot-weld together. Heavily loaded slow-moving machines are the most prone to adhesive wear - especially if surfaces slide over considerable distance building frictional heat (for example, large meshing gear teeth).
Also known as scuffing and galling, adhesive wear may be the least controllable as compared to contact fatigue and abrasion. More often it is the extent or rate of wear that is most controllable. When machines are well-engineered, well-manufactured, properly commissioned and operated within rated loads and speeds, adhesive wear is usually minimal.
However, when loads are exceedingly high, there may be a need to deploy surface-active EP/AW additives or solid lubricants (borate, molybdenum disulfide, graphite, etc.).
![]() |
![]() |
![]() |
![]() |
Adhesive Wear |
Machines Don’t Just Die . . . They’re Murdered
For some machines, trying to stop the progress of wear is like trying to defy gravity. We can’t escape the inevitable. Many machines perhaps are already on life support - they are too-far gone. However, this is just for some machines . . . not all. A high percentage of lubricated machines in normal service can have a seemingly infinite lifespan.
They are less prone to wear and failure when well-maintained. This is due to the many reasons we’ve just discussed relating to the environment and operating conditions to which we expose our machine’s surfaces.
You’ve probably heard the word “risk” defined as the probability of failure multiplied by the consequence of failure. When it comes to machine reliability, the consequence of failure may not be within practical control, but the probability of failure may be.
We’ve talked about the vital impact of human-agency on machine reliability. The frequency of human-agency failures tends to run inversely proportional to such factors as training, performance metrics and reliability culture.
Consider this; I recently heard a manager mention that maintenance has two problems:
- It’s broken because we didn’t work on it.
- It’s broken because we did work on it.
This is the maintenance paradox, no doubt. Anyone in the maintenance field has likely experienced it firsthand. Yet the answer to solving the paradox lies within, by simply restating the two problems as follows:
- It’s broken because we didn’t know how to prevent it from breaking. Or it’s broken because we didn’t know it was breaking and therefore didn’t work on it.
- It’s broken because we didn’t know it wasn’t breaking and worked on it anyway. Or it’s broken because we didn’t know how working on it might cause it to break.
“We didn’t know” is the common, operative phrase in the statements above. It too is controllable, like wear, but only when an initiative is taken to empower maintenance organizations through knowledge. For more on this, refer to my editorial on the “Hidden Cost of an Uneducated Workforce” in Practicing Oil Analysis magazine, (March-April 2003).
So . . . no, machines aren’t supposed to wear out. Yet they often do and if you investigate why, you will likely find they were in-fact murdered. If you follow the root-cause trail, you will likely find a smoking gun in the hands of one or more well-intentioned individuals (operator, craftsman, technician, mechanic, engineer, etc.) who simply didn’t know any better.
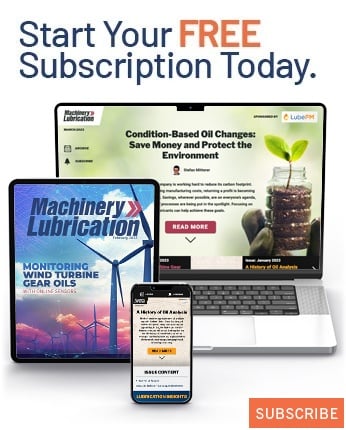