Survey Participants: Herb Springer, Southern Company; Bryan Johnson, Palo Verde Nuclear Generating Station, Arizona Public Service Co.; Dwayne Jenkins, Reliant Energy
The trend toward onsite oil analysis is ever increasing. For some, the desire to rely on an outside lab for routine analysis is the driving factor, while for others, access to immediate data is the key. To see how onsite oil analysis works in practice, we asked three of the more successful onsite oil analysis practitioners, Herb Springer of Southern Company, Bryan Johnson of the Palo Verde Nuclear Generating Station, Arizona Public Service (recipients of the 2001 Augustus H. Gill award for Excellence in Oil Analysis) and Dwayne Jenkins of Reliant Energy to share their views on how oil analysis can be an effective onsite condition monitoring tool. Here’s what they had to say:
1. How does onsite oil analysis make you more confident in making oil analysis-based decisions and in recommending associated maintenance actions?
Herb:
The results I get from doing onsite oil analysis are more representative of the health of the machine at that moment. I also know what my limitations are in interpreting the data, and can use the other condition-based maintenance (CBM) technologies (vibration, infrared, motor analysis, etc.) to verify my findings.
Bryan:
Doing the testing onsite improves our understanding of test data. As we process the sample with multiple unique tests, we are better able to draw correlation between those tests. A better understanding of the test methods and how they correlate improves our confidence in making a recommendation.
Dwayne:
Onsite oil analysis provides machine/ oil diagnostic information quickly. This is perhaps the largest benefit. With onsite oil analysis, it is now possible for the analyst to find a specific problem with a machine or lubricant, take the necessary corrective measures, and verify that the corrective measures actually eliminated the problem - all in the same day.
2. How has onsite oil analysis increased your team’s awareness and understanding about opportunities to improve machinery lubrication?
Herb:
We can demonstrate to others within the plant how we get our oil analysis results, so they have a better understanding of what we are doing. This allows them to draw a direct correlation from those results to machine health.
Bryan:
Onsite testing provides immediate feedback along with a deeper understanding of the significance of test data. This builds onsite expertise.
Dwayne:
You can’t measure what you can’t see. Being more aware of where lubrication problems exist allows the analyst to appropriately address them. (Generally speaking, sites with onsite oil analysis programs monitor more machines more frequently. Those involved with lubricants are trained in the field of oil analysis, and therefore opportunities to make improvements present themselves. Knowledge is key!)
3. Has onsite oil analysis helped promote a change in the organization’s culture toward precision lubrication practices?
Herb:
Cleanliness control is a major effort on our part throughout Southern Company. We use our onsite particle counters to monitor the cleanliness of new oil, top-off containers and in-use oil. We publicize improvements in systems such as turbine oil reservoirs and large circulating oil systems and bring attention to problem systems. By doing this, plant management and craft personnel alike are more aware of how their practices affect those cleanliness control efforts. Another example is water content in turbine oil reservoirs. By using our onsite oil analysis equipment, we can get a ballpark idea of water content and see potential problems with water ingress usually before the situation gets too bad. We can also monitor how effectively our water-removal systems are operating.
Bryan:
Our testing program can distinguish between similar lubricants. This sensitivity helps us find vendor-made formulation changes that we may not discover otherwise. When a product formulation change without a corresponding label change is found, we treat the material as a new product and evaluate it to ensure that it is the intended product. The sensitivity to small differences has increased awareness of differences in lubricants at our facility.
Dwayne:
In the way of organizational change, the early development of Reliant Energy’s oil program revealed that regularly tracking and trending oil analysis data could gain many predictive benefits. These benefits were seen to be of such value that four new positions were created within our central predictive maintenance (PdM) testing group.
4. Has onsite oil analysis increased the lube techs’ self-perception about the value they create for the organization? And, has this increased their enthusiasm to facilitate change in lubrication practices?
Herb:
In some places, yes. Those lube techs who are outgoing and assertive make very good arguments for improvements/ changes to plant systems. Those people get a sense of satisfaction when completing projects. Those lube techs who are not so outgoing but have supportive management also feel like they are providing value. I am constantly encouraging those techs who are not as assertive to be more vocal about potential issues and find ways to express their solutions in a manner that management will better understand.
Bryan:
My perception is yes. For example, oil cleanliness has been embraced by the electrical shop employees who have implemented cleanliness specifications and inspection hold points to ensure that sumps are clean in the large motors that are overhauled offsite. Care is taken to ensure cleanliness is maintained once the motor is returned, including pre-filtering new oil as it is installed.
Dwayne:
All of our PdM specialists believe in the values of onsite oil analysis. This is partly due to the fact that most specialists are cross-trained in multiple technologies and have personally seen instances where oil analysis provided information that was crucial in the decision-making process.
5. How does onsite oil analysis enable better integration of oil analysis with other condition-monitoring technologies?
Herb:
Our lubrication specialists are in the same department as the other CBM specialists. As part of our CBM certification process, each specialist must attend an awareness class to learn how other technologies complement each other. Their proximity to each other in the same office also lends to more communication between the different technologies.
Bryan:
The strongest recommendation is often one that is supported by multiple predictive technologies. We use this information to detect problems, estimate severity and provide feedback into future failure prevention.
Dwayne:
I think it’s a natural fit, however, the lube tech has to create value first. After all, seeing is believing, and training is the key to success. It is important that teams share successes with management. When management can see the results, oil analysis will naturally take its place.
6. Has onsite oil analysis eliminated your dependence on offsite laboratories, and/or does it enable you to employ the offsite laboratory services more effectively?
Herb:
We feel that it enables us to use the offsite labs more effectively. Instead of sending every sample to be tested at the offsite lab, we can screen out the good samples and send problem samples to the offsite lab for further review. Besides onsite screening, we send samples from each of our large turbine oil reservoirs to the lab annually for a bank of tests to determine water separability, foam resistance, rust inhibitors, RPVOT and several other tests. This gives us an idea of whether or not we need to plan a partial or full oil change out in the following year.
Bryan:
We perform all routine testing onsite and are not dependent on others for testing or analysis. We use outside vendor support for very limited offsite testing.
Dwayne:
We still regularly depend on offsite laboratories. It depends on the plant and how it operates. As a rule, we depend on the frequency of onsite screening for detecting incipient problems, then send the sample off for a more detailed analysis when a problem is perceived. Also, we send samples to an offsite lab for regular quality assurance/quality control (QA/QC) checkups.
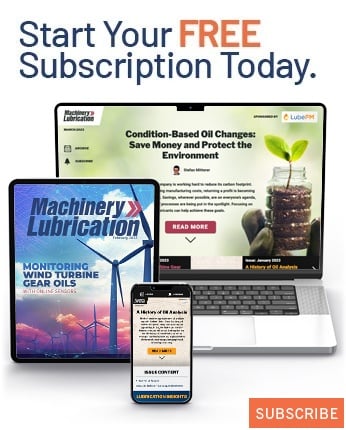