Today’s global economy is here to stay. Manufacturers from automobiles to toothpicks are under continuous pressure to reduce costs. In order to survive in this environment, a company must either adapt, embrace and master newly emerging technologies or be swallowed by those that do. EVTAC Mining is one of many companies currently striving to make such changes.
Several years ago, in an effort to reduce overall maintenance costs and improve production uptime, EVTAC decided to invest in an improved lubrication reliability program. As is the case with most production-based businesses, maintenance cost reduction was targeted by the reliability group due to the inherently fixed nature of operational expenses. Lowering maintenance costs of the mobile equipment at its open pit mining facility was at the top of the priority list.
Prior to making necessary changes, a cost benefit analysis was conducted to determine which areas would yield the best “bang for the buck” with respect to some of the proposed cost reduction efforts.
Overview
EVTAC is one of the smallest of six active taconite mines on northern Minnesota’s Iron Range. The EVTAC facility is a comparatively small open pit mine operation and employs three drills, two large 18 cubic yard loaders, four 23-cubic yard shovels and ten, 240-ton haul trucks to excavate and transport the raw materials to the plant. Unlike many of the other mines, EVTAC has made a break from the tradition of using electrically powered shovels and is instead relying on hydraulically powered machines. These shovels use twin 900-horsepower diesel engines to drive multiple hydraulic pumps, which in turn power the machine.
Each hydraulic system is extremely complicated and component intense. The major components of the system include a 1,000-gallon tank, seven main cylinders, 10 hydraulic pumps and several drive units. In all, the total system capacity is roughly 1,500 gallons and the system uses an ISO 46 hydraulic fluid. With only four active shovels, the loss of an hydraulic system can cut production by as much as 25 percent, making this system one of the most critical pieces in the whole mine site.
Maintenance Cost Analysis
Examining how maintenance man-hours were distributed on their shovel fleet was the first approach in evaluating maintenance costs. It was found that 44 percent of the maintenance hours allotted to the shovels were spent maintaining the hydraulic system (Figure 1).
Figure 1. Distribution of Shovel Maintenance
Hours by System
Based on further, in-depth analysis, it was documented that in a 23-month period, nearly $860,000 had been spent maintaining the hydraulic systems of the three machines, and more than $600,000, or 71 percent, was spent on maintaining the pumps, valves and cylinders (Figure 2).
Figure 2. Hydraulic System Maintenance
Cost Distribution
While the costs presented in Figure 2 indicate a significant cost of maintaining and repairing the hydraulic systems, they do not take into account the cost of lost production, which can run from one to several thousand dollars per hour for each of the four shovels, depending on production quotas and other variables. Clearly, the shovel hydraulic systems represented a significant cost-savings opportunity for EVTAC.
Root Cause Analysis
Having identified the largest cost center for the hydraulic shovel fleet, the reliability team’s next move was to determine the most efficient way to reduce expenditures on pump, cylinder and valve maintenance. To do this, the root cause of the accelerated pump, valve and cylinder wear had to be determined. At the onset of the project, it was suspected that a high level of contamination in the hydraulic oil was the culprit - not surprising in a mining environment.
This opinion was based in part on historical data and comments from both mechanics and maintenance planners, who complained about excessive spool valve wear, some with “holes worn clear through the castings” during previous routine preventive maintenance (PM) and repair work. Operators had also complained about poor control response on numerous occasions, a factor that can also be attributed to contaminated oil.
In order to confirm its suspicions, the reliability team turned to oil analysis for the answer. Fortunately for EVTAC, the lease contract for its shovels had included routine oil sampling by the local shovel service representatives. Although EVTAC Mining had leased the shovels well before the reliability program’s inception, the reliability engineer was delighted to find a database containing three years of oil sample data for each shovel.
Needless to say, the information proved to be a gold mine (not bad for an iron ore mine!). After reviewing the data, it was discovered that the shovel fleet was averaging an ISO fluid cleanliness level of 21/20/16. Since the system operates at pressures in excess of 4,000 PSI, it immediately became obvious that steps had to be taken to reduce the contamination levels, because the typically recommended fluid cleanliness levels for a high-pressure system with spool valves and piston pumps are around 16/14/11 to 17/15/12.
Corrective Actions
In light of the oil analysis results, the reliability team’s focus immediately shifted to the filtration systems currently used on the machines. Prior to upgrading the system, the only filtration was 10-micron nominal paper element filters installed on the low-pressure return lines to the tank. After making several calls to local filter distributors as well as the equipment OEM to discuss the team’s goal, it was decided that a retrofit filter design, rather than an attempt to upgrade the existing filters, would more cost effectively meet EVTAC’s goals.
Meetings were held with the local shovel representatives to review the system layout. Through these meetings, it was determined that a kidney loop system was not feasible unless the kidney loop pump was driven directly by the engine. Due to the complexity of piping such a system and the associated environmental risks, the reliability team rejected this idea and instead proposed tying into the low-pressure return lines and installing additional filters in parallel with the existing OEM filters.
It was reasoned that as the additional filters plugged, the flow of hydraulic fluid through the machine would approach that of the original OEM’s design, and would not compromise the performance of the system in any way. By setting the bypass pressure of the additional filters higher than that of the OEM filter system, it was also concluded that the addition of more filters would not cause a “short circuit” in the filtering system, with at least some of the fluid directed through the finer, add-on filters.
The Results Are In: Reduced Maintenance Costs
The shovel with three filters added to the hydraulic system has been a tremendous success.
Figure 3. Fluid Cleanliness Levels after the Addition
of the New High-Efficiency Filters.
Figure 3 shows the particle count trends that have been observed since the new filters were implemented in June 2001. It is obvious from the graph that oil cleanliness levels have significantly improved and are continuing to trend down. The gradual decline is because the team began with 12-micron, absolute rated, glass media filters and worked down to the 3-micron units which are currently used. At the same time, because only a fraction of the flow is directed through the new, higher efficiency filters, it will take some time for the whole system to finally reach the maximum obtainable cleanliness with the current system design. Also worth noting are the spikes that can be seen after the system went online.
These occurred when the additional filters were not changed during a PM task, and perhaps indicate the impact of contaminants introduced during routine PM procedures. The most recent (December 2002) hydraulic fluid particle count resulted in an ISO solid contamination code of 18/15/12, which represents an approximate tenfold to 12-fold improvement in overall fluid cleanliness levels, well on the way to achieving the targeted fluid cleanliness level of 16/14/12 set forth by the team at the outset.
Although it is too soon to gauge the full impact this improved level of fluid cleanliness has had on shovel reliability and related maintenance costs, it is anticipated that by maintaining current cleanliness levels, life expectancy of the system’s components will increase two to four times above their current life expectancy. Using these figures, annual savings for the four active shovels will be $160,000 to $240,000, or around 20 percent to 25 percent of the annual operating costs.
Again, it must be stressed that these numbers are based solely on maintenance, material and man-hour costs and do not include the savings associated with increased productivity and improved operational efficiency. Filter testing is still continuing today in an effort to further reduce the number of 5-micron and smaller particles in the system. Based upon the success seen thus far, the reliability group is now looking at ways to modify other machinery to achieve similar results.
Editors Note:
This case study illustrates an important aspect of any lubrication improvement initiative. Before starting on any improvements, the EVTAC team evaluated the maintenance costs associated with its critical assets, in this case the shovels, and put an action plan in place to target the suspected root cause, based on a Failure Modes Effects Analysis (FMEA). Because of this up-front planning, the reliability team at EVTAC was positive that its initiatives would be successful, lending credibility to the team’s plans and ensuring management buy-in. So go ahead - figure out where your biggest paybacks lie with lubrication, put an action plan in place that targets the root cause and reap the rewards of lubrication excellence. Let us know your successes!
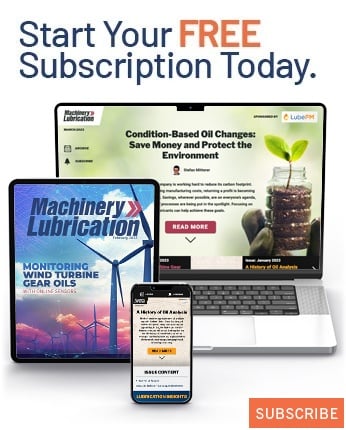