In today’s tumultuous stock market, building share price is the primary concern for managers and shareholders of companies. Gone are the days of easy growth in share price based on the flimsy promise of windfall profits. Today’s tough stock market demands real value and real earnings.
Historically, maintenance has been viewed as an expense - a cost of doing business. Increasingly, maintenance is viewed as a profit center, a method by which to create value and differentiation. Let’s explore this further and discuss the role of machinery lubrication in this emerging strategy.
In most heavy industries such as pulp and paper, primary metals, power generation, petrochemical, mining and general manufacturing, the participants are price takers for raw materials and for finished goods.
In other words, the plant, mine or mill has little say about the price it pays for the raw materials and energy required to produce its products, nor does it dictate the price it is paid for the finished products. In most instances, the raw materials and the finished goods are commodities.
Any profits earned must be gleaned from the process, assuming little or no control over raw material costs or the value of finished goods. This is called a commodity sandwich. In commodity markets, the low-cost producer creates the rules by which everyone else plays.
So what does this brief lesson in economics have to do with maintenance and machinery lubrication? Dupont has said that “maintenance is the largest single controllable expense in the plant; in many companies, it often exceeds annual net profit.”
Klaus Blache claims that top performers spend about 4.4 percent of sales to maintain their equipment vs. the actual average of about 5.9 percent (Table 1). One can argue that the actual percentages vary from industry to industry, but the relative differential between world-class and average is probably applicable. Imagine the difference between the best performers and the worst performers!
The great thing about avoided maintenance costs is that they go directly to the bottom line as profit - there is no cost of goods sold (COGS). In addition, when maintenance cost reductions are engineered, and not of the slash and burn variety, higher throughput and improved quality are typically enjoyed. This enables the plant to make money coming and going through improved maintenance.
Lubrication plays a vital role in improving maintenance and reliability. Baltimore Gas & Electric reported that improvements in lubrication and oil analysis, prompted by commitment to maintenance, contributed the lion’s share of its reported $15 million in additional profits (Figure 1).
This shouldn’t be surprising, as improvements in lubrication practice and contamination control actively modify the failure rate of equipment. Given that 30 to 50 percent of mechanical failures are in some way tied to poor lubrication, it should be the first target of a maintenance improvement plan.
Figure 1. Baltimore Gas and Electric's Reported
Profit from Improvements in Maintenance.
So what does this have to do with a company’s share price? Take for example a manufacturing company with annual sales of $2 billion dollars, earnings before interest and tax (EBIT) of $120 million and 50 million shares outstanding. That results in earnings per share (EPS) of $2.40.
Assuming a typical price to earnings ratio (P/E), the company’s stock would trade at $30 per share. Improving from average performance in maintenance to world-class would increase earnings per share from $2.40 to $3.00. Assuming a constant P/E ratio of 12.5, one could argue that the share price would trade at $38 per share - an increase of $8 per share, or 27 percent! See Table 2.
One may presume that if maintenance costs are reduced through well-engineered programs, not arbitrary cutbacks, reliability will improve throughput and quality, which should further bolster stock price. Likewise, it is well known that the most profitable players in an industry are rewarded with higher P/E ratios.
So if your management is interested in bolstering share price, maintenance is a great place to look. Building lubrication excellence into your maintenance program is a great place to start. That is my Viewpoint. As always, I am interested in yours.
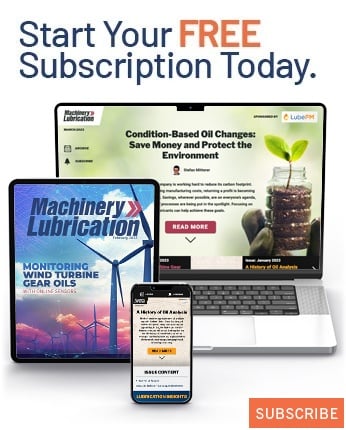