Hydraulic systems are old technology. This statement is true, to a degree. The field of hydraulics cannot be measured in decades, or even centuries. In fact, the basic principles appear to date back thousands of years to the water clock, which employed the first known float valve and was designed in Alexandria around 250 B.C.
This is thought to be the earliest fluid feedback system on record, although since then there has been a long gap in its documented history. The pressures of the Industrial Revolution helped rediscover the potential of hydraulics. Two world wars and the rapidly expanding automotive and aviation industries have further driven evolution into today’s complex pumps, valves and servomechanisms.
Their origins may be ancient, but for controlling the enormous pressures created by relatively small energy inputs, hydraulic systems have been unparalleled.
Injection molding technology, by comparison, is relatively new. The creation of celluloid by John Wesley Hyatt around 1900, heralded the new age of thermoplastics. These novel materials were moldable with the application of heat and pressure, but held their shape once cooled. By the 1930s, several cost-effective alternatives to rubber and metal had been synthesized, including PVC,
Teflon and polyethylene. The desire to explore the potential of these wonderful new materials quickly combined with the industrial trend toward process automation. The result: the plastic injection molding machine (IMM). The basic operation involved two halves of a mold, mounted on supporting platens, being clamped together at high pressure using hydraulic cylinders.
Plastic substrate pellets were melted in a special screw device and the liquid injected under pressure into the mold cavity as fast as possible. The plastic cooled and hardened, the mold halves were separated for finished part removal, and the cycle began again.
Mass production of consistent, quality parts in this way represented an immediate and huge commercial advantage when compared to the cost and variation in hand-produced items of that era.
Machine Development
The earliest IMMs had quite different capabilities compared to their modern descendants. Clamp tonnage was relatively low, and machines were restricted to using simple molds which turned out small parts; typically just a few ounces. Both ends of the spectrum have since developed dramatically.
The largest hydraulic IMMs turn out massive automobile parts such as entire bumpers or panels. Parts heavier than 50 pounds are now possible, from machines controlling clamp forces up to and exceeding 8,000 tons. In stark contrast, micro-molding machines work in the 10 to 30-ton range; creating the most complex and delicate of medical and electronic supplies that weigh mere fractions of an ounce.
Click here to see Figure 1. Cutaway View of the Injection Molding Process.
Most plastic-based technology can be similarly applied to powder and metal injection molding, in which metal-based molded parts are later transformed into finished metal items through additional processing steps.
A plastics processor choosing a new machine now has better selection than 10 or 20 years ago. Equipment of all types is getting smaller, faster and more energy efficient. Vertical molding is now a familiar option in some applications, while tiebarless technology has improved product removal and mold changing in others.
Overall, the fastest growing segments of the popular midrange (200 to 500 ton) market are the all-electric and hybrid molding machines. All-electric manufacturers claim to offer greater precision and control over machine movements, combined with significant energy savings. Hydraulic machines are often considered to be more effective where greater clamp forces or high linear speeds are required, where plastic nozzle pressures are greater or holding times longer.
The pros and cons of each type depend on the application and the environment, with hybrid machine manufacturers claiming to offer the best of both worlds. Hydraulic machines represent the majority of the installed equipment base and overall new sales, and thus are the focus of this article.
Economic Perspective
The United States leads the world in plastics processing. Depending on the methods of classification and measurement, approximately 20,000 plastics processors employ around one and a half million workers in the fourth largest industry in the United States. Around half of these processors have injection molding onsite, creating an installed base of some 100,000 IMMs. Japan, Germany, France, United Kingdom and Italy follow some distance behind.
To put the European markets into perspective, the U.S. injection molding market, estimated at around $100 billion, is almost twice the size of the whole European Union market.
Success in the competitive plastics processing market is achieved through competitive edge. The nature of this edge is constantly changing. Several years ago, when customers were right on their doorstep, injection molders could maintain and grow their business by offering improved quality and consistency at a good price.
More recently, the stakes have been raised and the prices lowered. The United States may be the biggest plastics producer, but it is now as much under threat from the global marketplace as Europe.
Where many Asian and Middle Eastern producers once lacked sufficiently advanced machines to deliver quality in their end products, they are now able to supply and ship finished goods of a comparable standard. And at a price considerably lower than any U.S. or European molders.
Manufacturer purchasing teams are under increasing pressure to reduce their costs; many must reduce spending year to year, regardless of market prices. Despite satisfaction with their long-term supplier partnerships, an increasing number are now farming out their once-guaranteed injection molding contracts on an international basis.
The economic downturn during 2001 and 2002 has also had a negative impact on U.S. and European industry. The manufacturers that buy molded products have suffered, as their suppliers have too. Businesses are only slowly starting to show the predicted signs of recovery during 2003. For molders, continued pressure to reduce operating costs is now one of the main survival strategies.
It has been suggested that more than $600 billion per year is spent by industry (in general) on repairing damage caused by wear. Better maintenance and lubrication are key to reducing such operating costs. For hydraulic systems, the right lubricant and right lube engineer can really be worth their weight in gold.
The Maintenance Challenge
An ideal IMM should include the following:
- the fastest possible cycle speed
- continuous, smooth operation for long periods
- no significant downtime: quick changeovers, no major failures
- maximum repeatability: few/no reject parts despite fine tolerances
- low (or no) materials waste
- minimal energy costs
- mold protection
- long machine life span
A basic hydraulic system is a distributed drive, consisting of an electric motor-driven hydraulic pump, control valves, pistons and interconnecting pipes and hoses. Whatever the level of complexity, all such systems must overcome the same two fundamental issues.
One fundamental issue is leakage of hydraulic fluid, which can cause unpredictable pressure drops in an IMM. This ruins consistency of operation, causes high levels of reject parts and can cause mold damage. However, most sources estimate that 80 percent of all problems with hydraulic IMMs originate from the second issue - hydraulic oil contamination.
When capital investment can exceed half a million dollars for a brand new, large machine, and when today’s increasingly sophisticated and expensive control mechanisms are more easily damaged by wear or contamination, lube engineers need to fully understand the exact nature and condition of their hydraulic fluids.
Fluid Classification
Not all hydraulic fluids were created equal. It pays to know more about the characteristics of the selected fluid than one might think. Especially when considering the large volumes of fluid required to fill some large machines. The hydraulic fluid needs to resist oxidation, while protecting mechanical components from the high-pressure, hot environment. More challenging still, the fluid must do this in the presence of water from condensation and contaminants from the operating environment while remaining finely filterable.
Most hydraulic fluids use mineral oil as a base, which is categorized into quality Groups I, II or III according to American Petroleum Institute (API) definitions, with Group III mineral base stocks having performance properties similar to Group IV synthetic hydrocarbons (poly alpaholefins).
Base oils for hydraulic fluids are increasingly hydrotreated and hydrocracked to improve their viscosity index (VI) and lower their aromatic and sulphur content. These changes improve oxidative and color stability. Generally speaking, selected oils from Group II provide the best base stocks for hydraulics. Group III oils possess qualities close to synthetic and are mainly used in crankcase applications, largely due to their expense. Synthetic (Group IV) oils are relatively uncommon in hydraulic systems.
“The Group classification is not everything. There can be wide variation in performance within a group,” advises Dr. Helen Ryan, head of global industrial development at Ethyl Petroleum Additives.
“Even a good Group II base oil cannot alone provide effective lubrication under the operating conditions in IMMs,” Ryan says. “Effective additives and filters are essential for hydraulic fluids to operate successfully in the presence of water and contaminants.”
Typical antiwear hydraulic additive treat rates (concentration) are less than one percent, but the characteristics they deliver are essential to maintaining lubricant and machine health. The priorities for a good fluid include: viscosity index (VI), hydrolytic and thermal stability, antiwear performance and filterability.
Viscosity
An appropriate VI (100 +/-) denotes the lubricant’s effectiveness in separating moving parts of pumps and valves under changing conditions. Viscosity is determined largely by the base oil, but may be enhanced by adding shear-resistant viscosity index improvers, which help to maintain the desirable viscosity at higher temperatures and pressures.
Air Release and Foaming
Air release is mainly a function of the base stock, and oils need to be monitored for this. Foaming will also vary in different base oils but can be controlled by the addition of antifoam agents.
Hydrolytic Stability
Hydraulic fluid needs to be resistant to hydrolysis, which is chemical breakdown in the presence of water.
Thermal Stability
Lubricant oxidation rate increases with temperature, causing formation of sludges and varnishes that damage and plug fine tolerance parts. Antioxidant additives, usually aminic or phenolic compounds, help resist lubricant breakdown at higher operating temperatures. IMM hydraulic fluids are generally maintained at around 110ºF to 120ºF during operation, using appropriate thermal control systems.
Modern IMMs now tend to have safety shut-offs that activate at temperatures higher than 130ºF, well below the point beyond which heavily accelerated breakdown of the fluid begins.
The degree to which a lubricant is becoming oxidized should be tracked by measuring its acid number (AN), which indicates when it should be replaced.
Antiwear
Antiwear additives are essential for hydraulic fluids because in these systems, hard surfaces come together under pressure. Normally, zinc dialkyldithiophosphate (ZDDP) is used. It was originally developed for crankcase applications in the 1940s, and was refined for hydraulic use during the late 1970s. ZDDP has both effective antiwear and antioxidant properties.
In some sensitive areas, because of environmental legislation, the use of nonmetal (sulphur and/or phosphorus-based) additives are used. Using this form of technology was once a performance compromise because it tended to be less thermally stable, however high-performing ashless additives now exist.
Antiwear additives deplete naturally with usage, so their levels should be carefully monitored over time to ensure the fluid doesn’t lose its effectiveness, resulting in component damage. The more extreme the application and temperatures, and the more contaminants involved will result in shorter oil life.
Filterability
A good hydraulic fluid must have excellent filterability. The AFNOR NFE 48-690 test measures filtration performance under dry conditions. However, for injection molding hydraulics, only fluids passing AFNOR NFE 48-691 under wet conditions are up to the task.
The latter test measures filtration in the presence of water for an aged oil, which more closely replicates actual operating conditions. The tests measure the times taken to filter initial and subsequent volumes of oil, which are then used to calculate the Index of Filtration (IF). The closer the IF is to one, the lower the tendency to clog filters over time and therefore the more desirable the oil.
Additives such as rust and corrosion inhibitors must be water-friendly. Some acidic rust inhibitors will actually interact with water to form precipitates which worsen problems with blocked filters or corroded pumps and valves. Surface active additives will fall out of the additive package when other precipitates form, which means they start to lose performance. Significant precipitation indicates that additive concentrations remaining in the fluid should be checked.
Condition Monitoring
Traditional reactive or preventive maintenance procedures are fading in usage. The more popular predictive maintenance ethos - changing parts and fluids only when their condition shows it is necessary - better suits both cost-saving activities and the latest machine technology. For this approach, analysis of lubricant composition and therefore performance, needs to be carried out regularly while the equipment is in operation.
This condition monitoring is used to predict the remaining useful life of the lubricant and its additives (and to some extent machine parts) to avoid breakdowns as well as unnecessary expense or downtime. It appears to require lube engineers to add the title of chemist to their job descriptions, but this does not have to be the case.
Fluid, additive and filter condition should be the lube engineer’s guide to fluid replacement. State-of-the-art, built-in or mobile sampling equipment is one possible route, which allows on-machine or onsite fluid analysis at standard intervals. Another method is to install simple dirt alarms or pressure switches into the hydraulic system. These alert maintenance engineers to blocked filters or excessive contamination, prompting samples to be taken and checked.
Those not in a position to purchase monitoring equipment need not lose out, because many hydraulic fluid and equipment suppliers also offer oil analysis services. They will monitor fluid condition on your behalf and advise of any issues. When working with an external lab, particle counts (as well as content analysis) should always be requested. Understanding how quickly lubricants or additives are changing is as useful as identifying the nature of change.
Presence of metallic particles may indicate wear in a particular component, but knowing the number of particles and rate of build up indicates how imminent failure could be. Obviously, condition monitoring needs to take place with sufficient frequency to allow the proactive protection of machine parts, and ideally would allow maintenance to be planned for already-scheduled downtime.
Recommendations on this do vary from supplier to supplier, but as a general rule, fluid analysis at least once per month is considered a useful interval without incurring excessive cost. Better still is proactive maintenance - controlling root causes of system and fluid degradation.
Cleanliness
Hydraulic fluid should be physically clean, as determined by the number and size of particles suspended in the oil (refer to ISO 4406 cleanliness codes for details). Foreign matter can contaminate the system through fluid top-ups, reservoir tanks and faulty cylinder seals. Internally generated silt and sludge from lubricant or mechanical breakdown also represents a problem.
As hydraulic components develop in complexity, tolerances have become much smaller, significantly increasing particle contamination sensitivity. Sophisticated pump and valve parts commonly have clearances of under five microns, so most OEMs recommend return line filters of three microns or less, providing cleanliness levels of ISO 15/12 or better. Anything less can place the health of control systems, and therefore molds, at risk.
External contamination can be dealt with at the source. Hydraulic reservoirs should have a fine, low-pressure air filter fitted to the breather. Machines should not reside next to mills, lathes or other airborne particle-generating machinery. Oil storage and handling procedures, plus efficient stock rotation, help avoid contamination from new fluid.
Some new oils may be filtered to only around 40 microns and therefore are not clean enough, even if they visually appear to be. Such oils should be filtered through the system several times until the correct cleanliness levels are reached, before machine start-up.
Future Trends
Original equipment manufacturer (OEM) investment suggests that the future is bright for hydraulic injection molding equipment. Key players believe that with smarter control systems, hydraulics could soon match or exceed the precision performance (and energy-saving benefits) of all-electric machines without their current weight/tonnage limitations.
More and more electronic components have been integrated into hydraulic motion control packages, enhancing performance with new features such as midstroke positioning. In parallel, clamp pressures continue to rise, with no apparent limits yet other than sheer machine size.
All-electric machinery is being touted as the way forward in some areas, because of its energy-saving claims. Indeed, it is predicted that by the end of this year as many as 15 percent of all installed machines could be all-electrics or hybrids, mainly concentrated in 200 to 500-ton range.
Despite this optimism, all-electrics still seem limited by clamp forces, topping out around 1,000 tons. However, manufacturers remain convinced that with further technical breakthroughs there will be no limits in the future. If that does happen, whether all-electrics will retain their energy-saving advantages remains to be seen.
Customers continue to push for smaller footprints, wanting to maximize use of space in their facilities. Some hydraulic machines already have a dramatically cut-down cylinder travel of around one inch (from 30 or 40 inches), reducing oil volume requirements by up to 50 percent and driving faster cycle times.
Noise levels and leakage are still being targeted for reduction and eventual elimination by hydraulic OEMs. Pump manufacturers have been working on this for several years and tests now specify leak-free operation for at least 10 million cycles in IMMs.
Hydraulic development shows no signs of slowing in IMMs. Outside this arena other hydraulic applications are also showing rapid progress; the smarter the system, the greater the lubrication challenges will be. Dr. Ryan of Ethyl Petroleum Additives indicates technical programs are underway to ensure the lubricants of the future can deliver.
“We are already working to meet the challenge of sophisticated new pump and valve systems for related fields such as critical mobile hydraulics. Recent OEM specifications in those applications exceed all previous test standards. The enhanced lubricants and additives we have generated through this latest phase of development can ultimately be extended to protect the latest injection molding machinery, as well as support new technology in the future.”
References
- American Plastics Council Web site: www.americanplasticscouncil.org
- Jenkinson, J. (September 2002). UK Plastic Injection Moulding 2002. Industry Report: Jenconsult.
- National Fluid Power Association Web site: www.nfpa.com
- Park, R.W. (August 1997). Contamination control: A hydraulic OEM’s perspective. Workshop on Contamination Control: Monash University.
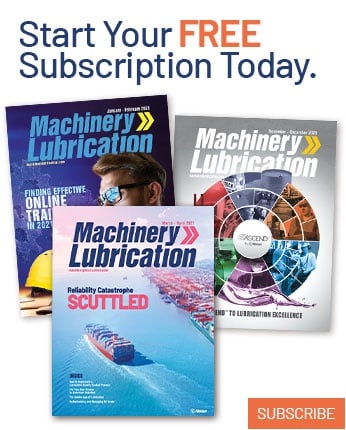