The blotter spot test dates back to the early 1950s. It is one of the oldest techniques used to identify excessive engine soot, evaluate a lubricant’s dispersancy and detect the presence of glycol, diesel fuel and other contaminants in diesel engine crankcase lubricants. Several different field methods and even sophisticated instruments are used to take advantage of this simple technique.
For large fleet operators, this simple, yet powerful technique can provide valuable information when used as a screening tool. In fact, this method is so powerful that Grupo Flecha Amarilla of Leon, Mexico, one of the largest transportation companies in Mexico, found a significant reduction in catastrophic engine failures in its passenger bus fleet by integrating offsite laboratory-based oil analysis with onsite blotter spot testing.
Flecha Amarilla operates more than 2,500 buses, each logging approximately 500 miles daily under stop-start conditions. Standard operating procedure required changing the oil every 25,000 miles, which led to about 1,500 oil changes per month.
The procedure also required an oil sample to be taken at every oil change and sent to a laboratory for complete oil analysis.
Oil analysis was performed in an independent laboratory located in Houston and the results were delivered electronically to each service shop for trending and interpretation. The turnaround time from the time the oil sample was collected to the time analysis results were received averaged 16 days. This was mainly due to the logistics associated with consolidating the oil samples from different service shops and sending them to the lab.
The oil analysis program delivered some benefits to the company, alerting it to diesel fuel leaks and glycol contamination. It also helped the company detect combustion problems and abnormal wear. However, the maintenance manager was not satisfied because he had to wait up to 20 days to find out when an engine had a problem - all the time with the engine in operation.
In some cases, the problem might be present in an engine for more than 40,000 miles before oil analysis identified the problem. This delay sometimes led to major engine failures, even though an oil analysis program was in place.
To aid the maintenance department in identifying problems before they caused major engine failure, a plan was presented to refine the procedure and use the blotter spot test onsite as a screening tool. The test was seen as a way to quickly detect problems in the diesel engines and as a decision tool for those engines requiring immediate maintenance inspections and corrective action.
Dual Analysis and the Learning Curve
The strategy employed by Flecha Amarilla was simple. A sample was taken at each oil change interval and was initially pre-screened using the blotter spot method (see The Blotter Spot Method, page 26). Any abnormal result was used to trigger either an exception field test or inspection, or more in-depth analysis by the outside lab. Samples that showed no initial problem from the blotter spot test were sent to the outside lab for routine analysis (Figure 1).
Figure 1
An important part of implementing a successful program was to compare the blotter spot test results with data provided by the outside lab. Whenever an abnormal oil analysis result was flagged by the lab, maintenance staff analyzed the blotter spot results to try to correlate the appearance of the blotter with the lab data.
By doing this over a period of months, their maintenance staff began to recognize how different problem conditions such as soot, glycol and fuel dilution identified by the lab appeared on the blotter. Eventually, maintenance personnel became so comfortable with analyzing the test data that they could rely on the results to make important maintenance decisions, well in advance of data being returned from the lab.
The Blotter Codes
Abnormal results were classified according to severity and a code was created for each category. This simplified the interpretation and decision process. Also, a reference standard was created to help implement the program in different service shops (Figure 2).
Figure 2
A three-digit blotter code was created to report results in a pseudo quantifiable fashion. The first digit indicates soot load, the second fuel dilution and the third relates to glycol contamination (soot-fuel-glycol). Each code has three possible categories, which are related to the observed conditions and correlated to laboratory data (Table 1).
When results are reported, the position relates to the contaminant or condition, while the numbers identify the problem’s severity. For example, an oil sample that indicates excessive soot load, but is negative for fuel and glycol, will have a 3-1-1 result (3 soot, 1 fuel, 1 glycol).
Click Here to See Tables 1 and 2.
Chromatogram Patterns
In addition to the blotter codes, four different zones for each chromatogram were created (Table 2):
- C - Center Zone - Area where the original oil drop was initially deposited
- A - Aureole Zone - Rings formed outside of central zone
- D - Diffusion Zone - Area of diffusion of medium to small size particles
- T - Translucent Zone - End of the chromatogram (base oil and diesel fuel)
The most frequently detected problems are diesel fuel dilution and excessive soot load. Glycol has been the most difficult to detect. However, based on severe dispersancy failure and samples that are thought to contain glycol, a filter inspection is ordered to confirm the glycol leak. Glycol contamination is confirmed if the filter paper is wavy and saturated with gel or sticky materials, again allowing corrective action to be taken in advance of catastrophic failure.
While the blotter spot test is not a substitute for quality, laboratory-based oil analysis, Flecha Amarilla has found that by integrating onsite blotter spot analysis with offsite oil analysis, important insight can be gained into common engine oil problem conditions, such as excess soot loading and dispersancy failure, fuel dilution and glycol leaks. Since the routine blotter spot test program was put into practice, no major engine failures have occurred and problems are now controlled in the early stages, helping increase engine life.
Additional Reading on Blotter Spot Testing
Lantos, E., Lantos, F. and Lantos, J. (2002, July-August). The Lantos Method. Practicing Oil Analysis.
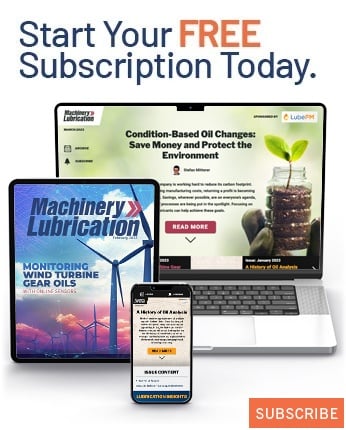