Routine particle counting is an important part of a modern, proactive contamination control strategy. The practices of ensuring proper oil handling and storage and improving seals, breathers and filters can greatly improve overall equipment reliability. To ensure that these practices are paying off and that contamination control targets are being met, accurate particle count data is more important than ever.
For many, a particle counter is the first onsite oil analysis instrument they purchase. The reasons are obvious; a particle counter is perhaps the most versatile tool in any condition monitoring toolbox. Among its many uses, an onsite particle counter can be used to:
- Ensure cleanliness of new fluids,
- Verify performance of in-service filters,
- Warn of incipient wear,
- Identify seal and breather failures,
- Monitor roll-off cleanliness of new and rebuilt components,
- Identify the need for an on-condition filter change, and
- Schedule the use of offline filter carts to maintain target cleanliness levels.
Despite the obvious advantages of onsite particle counting, many facilities reject this option outright. Their fear - in many cases well justified - is that with less and less time to perform even basic maintenance tasks, adding one more task that could be outsourced to an external lab is unnecessary and unwarranted.
To overcome these difficulties, Pamas GmbH, a sensor and instrument development company headquartered in Rutesheim, Germany, has developed a simple, easy to use particle counter, the Pamas S-40, in conjunction with a unique software program, Routing and Analysis Software (RP). When used together, they allow the end user to store sample point specific and routing information along with particle count data, making the Pamas system an accurate, effective time-saving package.
In many plants and facilities, the number one complaint by end users is it takes too much time to take bottle samples. Most people responsible for the sampling simply do not have the time to take the samples needed. Depending on the operator’s personality and commitment to the program, there is always the temptation to take a short cut to save time. However, saving time during the sampling process can lead to serious errors that can invalidate the data.
The best solution to this problem is to make the simplest way, the correct way. With bottle sampling, attention to a consistent sampling procedure, bottle cleanliness and flushing volumes all serve to make sample taking a time consuming process. However, with the Pamas S-40, it’s as simple as connecting the instrument to the test port with the sampling tube and pressing “Start.”
The second issue that can lead to inaccurate data is operator error. The Pamas system is setup from the beginning to limit user error. Once the profiles, or parameters, are set in the routing software for each sample and sample point, the operator cannot change them. This can only be done in the “administrative” level of the program.
These profiles are customized for each point of each hydraulic or lubricant system to be tested. By limiting the sampling operator’s access to change the equipment parameters and by removing the need for bottle sampling, sampling and operator error are removed from the particle count equation.
How Does It Work?
The Pamas Routing and Analysis Program along with the Pamas S-40 is a modular-based system for monitoring contamination control levels in plants, equipment fleets and oil labs. Not only does the software download and store the particle count data, but it also has trend analysis capabilities for tracking a system’s cleanliness.
Other Pamas systems can also be used in conjunction with this system. For example, result files from the Pamas SBSS bottle sampler as well as digital photographs of membrane filtered oil samples (according to ISO-4407) can be saved to the Pamas-RP program. Therefore, if a potential customer already has an existing program, Pamas can adapt the RP program to the customer’s process.
Whether you have a plant floor full of machines or a fleet of equipment, this system will allow you to utilize predictive and proactive maintenance strategies without interrupting your current manufacturing process.
To illustrate the point, the following is an example of a typical facility setup:
-
A Pamas representative will show up at your facility to setup and install the Routing and Analysis Program.
-
Each machine number will be setup in the software, as will the individual test points on each machine. (Existing equipment ID numbers are typically used for this purpose, along with a unique sample point identifier.)
-
A profile, or parameter, will be setup for each test point. It is important to set up the S-40 so that the sample is a good representation of the oil in-service.
-
A test run of the system will then be performed with all people involved and hands-on training provided. If you do not already know, this is a good time to find the systems’ baseline cleanliness for a starting point!
The typical day-to-day operation of the Pamas system consists of the following:
-
Supervisor of person in charge of program uploads the days testing into the S-40 by simply connecting the S-40 to a computer via a nine-pin serial cable.
-
The operator in charge of the actual sampling turns on the unit and presses “New Sample.” The screen on the S-40 shows the machine number and point to test.
-
The operator then simply connects the S-40 to the equipment via a quick connect and presses “Start.”
-
When the sample is finished, the operator simply repeats this process until all points have been tested.
-
The supervisor then downloads the day’s data into the Routing and Analysis Software Program via the same nine-pin serial cable to view, print or analyze the data for each test point.
It seems simple here, and it is - that’s the point! Making the whole sampling and analysis process as simple as possible is the key to accurate, reliable data.
The Pamas particle count system comprises all the elements required to get started: the Routing and Analysis Software Program; installation and support; and hardware. The hardware used for this program is the Pamas S-40 laser particle counter. It can be calibrated according to ISO 11171, as well as ISO 4402. This allows cleanliness standards to be reported for ISO 4406:99 (including AS4059D) or ISO 4406:87 (including NAS 1638). The S-40 is a proven workhorse in the particle counting industry. Released three years ago, it is a system designed for many different applications and operates in all different environments.
The S-40 was designed with the end user and tested by end users with rugged durability in mind.
Some of the user-friendly features of the Pamas S-40 system include:
-
Portable for both bottle sampling (non-pressurized) as well as high pressure sampling up to 6,000 psi;
-
Auto sensing power supply for 110 to 230 volts as well as internal battery operation;
-
Stores up to 1,500 profiles;
-
Operates with viscosities up to 400 cSt with an option of up to 1,000;
-
Minimess and standard connectors; and
-
Built in thermal printer.
Particle counting is a vital part of any modern reliability program. The Pamas S-40 along with the Routing and Analysis Software Program will help you save time and money, while aiding you in implementing a solid predictive and proactive maintenance program without disruption of your current manufacturing and operating processes.
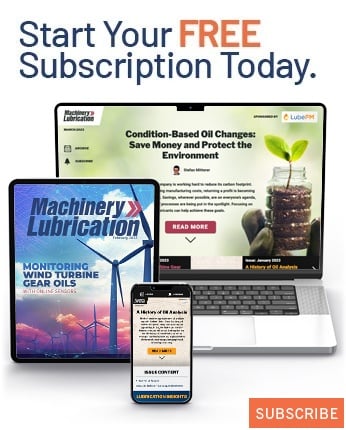