The U.S. Environmental Protection Agency (EPA) continues to adopt and enforce more rigorous nitro-oxidation (NOx) and hydrocarbon emission policies for heavy-duty diesel engines used in trucks and buses.
New environmental policies fueling ever-increasing engine soot loads spell good news for the environment, but bad news for lubricants. The soot has to go somewhere. Since its expulsion into the air is linked with respiratory diseases, the lubricant must serve as the "trash-can" of the system collecting the soot generated during combustion.
Given the clear and undisputed priority to protect air quality and human health, we in the lubrication management business must gear up to ensure that the impact of this new legislation on engine performance is minimized. Major engine manufacturers have identified soot and "black sludge" deposition as a major cause for engine failure.
We in oil analysis must be sure we are supplying appropriate information with which to make good decisions and ensure that this important impairment to engine reliability is held in check.
For 2004 and later model engines, the EPA has imposed tough new standards intended to decrease NOx emissions by 50% compared to 1998 model engines. The EPA expects the new standards to reduce ozone precursors by 1.1 million tons per year, abate acid rain and decrease particulate matter by about 43,000 tons per year.
In sum, the legislation substantially reduces contaminants that are believed to cause or exacerbate the effects of a wide range of pulmonary and respiratory health problems.
Soot, comprised 98% of carbon by weight, is formed during the combustion process and enters the crankcase with combustion gas blow-by. Soot particles have a near spherical shape and originate in the .01 to .05 micron size range, but tend to agglomerate to form larger particles.
Research into soot particles suggests that the size distribution during normal operation varies, but averages about .078 micron with a skew to the right due to the dominance of small particles (see Figure 1). Normally, soot generated during combustion exits via the engine's exhaust system.
Recent regulations limiting the emission of NOx and soot has led to the employment of exhaust gas recirculation (EGR). Certain diesel engine manufacturers have recently negotiated an agreement with the EPA that has resulted in a settlement to tighten emissions by October of 2002, largely through the introduction of new emission control technology like EGR.
EGR essentially sends the emissions back to the combustion chamber creating a multi-pass opportunity for soot to ingress to the lubricant. An EGR valve regulates how much exhaust gas is recirculated. At idle, about 70% of the exhaust gas is recirculated, while only about 10-20% is recirculated at full load.
While EGR does effectively reduce NOx and soot emissions to the atmosphere, soot loads in the lubricant can be expected to increase dramatically, causing increased temperature and viscosity, dispersancy failure, fouling, deposits and wear.
To deal with the effect of EPA regulations on engine lubricants, the cycle-time between engine lubricant upgrades is shortening. API CH-4, the most recent upgrade in lubricant quality for emission-controlled four stroke heavy-duty diesel engines took effect on December 1, 1998, only four years after API CG-4, its predecessor.
Engine manufactures have already requested Proposed Category 9 (PC-9) for licensing in January of 2002, accelerating the previously planned release in 2004 and further shortening the cycle to three years. A challenge faced by lubricant manufacturers is the disagreement among engine manufacturers on the topic of lubricant qualification testing. Presently, seven engine tests and six bench tests are proposed for PC-9 qualification. This makes lubricant qualification very expensive and time consuming.
In addition to EGR, numerous operational factors affect the level of soot contamination in the engine. Fuel injection timing, combustion chamber design, engine type, scavenge efficiency, air cleaner restriction, air/fuel ratio, low compression, excessive idling, lugging, etc. all affect soot levels. Soot enters the lubricant with exhaust gas in the form of blow-by, or it is deposited on cylinder walls and subsequently scraped off by the rings and deposited into the oil.
Increasing concentration of soot contamination causes a variety of problems summarized in Table 1. Strain on the lubricant's dispersant additive is among the more concerning effects of increasing soot loads. Soot particles are attracted to one another (by forces of the van der Waals type), agglomerating to form larger particles when they collide, presenting a greater risk to the system.
The same forces cause soot to deposit onto machine surfaces. The job of the dispersant additive is to keep the soot particles finely divided and off of machine surfaces. It works by enveloping the soot particle in a single layer. The polar head of the dispersant molecule clings to the particle directing the additives "oleophillic" tail outward to dissolve easily into the oil (see Figure 2).
By surrounding the particle and dissolving its tail in the oil, the dispersant additive suspends the soot particle in the oil, prohibiting it from agglomerating with other soot particles or depositing onto component surfaces. The dispersant additive provides once-through protection. Once it is depleted, dispersancy is lost, leaving the machine at risk.
![]() |
Figure 2
|
Research has clearly concluded that soot increases the viscosity of the oil. Increased viscosity leads to higher temperatures, higher pumping costs and the risk of lubricant starvation, especially at start-up. Figure 3 identifies the soot/viscosity relationship for various base oils.
Highly saturated base oils (API Groups II, III and IV), it seems from the research, resist soot thickening better than the lower quality Group I base oils containing a larger number of unsaturated molecules. These Group II, III and IV base oils exhibit later and less severe increases in viscosity than the Group I base oils.
Research conducted by Lubrizol reveals that dispersancy concentration also plays a major role in reducing the soot thickening effect. Figure 4 illustrates the increase in viscosity (expressed as multiples of the new oil’s base-line viscosity in cSt @ 100° C.) relative to varying soot concentration for oils with 1.2% and 4.8% dispersancy respectively.
In other research, Lubrizol assessed the effect of various soot loads on the component wear. Their results suggest that increasing soot load does not necessarily affect the wear rate (see Figure 5) as long as dispersancy performance remains good.
The researchers found in a study of roller follower wear on engines with increasing soot levels that the rate of wear is sporadic and not systematically related to the soot level. Conversely, they did find that dispersant level significantly affects the rate at which wear is generated.
In their research, abrasion was identified as the cause for the roller follower wear and it was tied to soot dispersion. The study purportedly eliminated corrosive attack and abrasion caused by other particles as possible influencing factors.
The Lubrizol researchers concluded that wear is caused by the agglomeration and deposition of soot caused by dispersancy loss rather than high concentration of soot. That leaves the question: should oil analysts schedule oil changes based upon soot concentration or dispersancy performance?
The answer is probably both. We need to increase our soot monitoring efforts to be sure, but according to Lubrizol, we should be equally interested in measuring dispersancy performance, a parameter not typically included in a diesel engine oil analysis program.
Measuring Soot and Dispersancy
The research by Lubrizol might lead one to conclude that soot measurement is not important and that efforts should focus entirely upon dispersion. This is not true. Soot concentration, especially the change in concentration, is very important because it provides a general indication of the health of the combustion process and identifies abnormal blow-by.
Also, when dispersancy is effective but soot load is high, other contaminants like water and glycol can quickly knock out dispersancy performance without an increase in soot load. When soot loads are high, this sudden loss of dispersancy leads to rapid agglomeration and deposition of soot onto machine surfaces. The analyst must take this relationship into account when responding to water or glycol alarms in systems carrying a high soot load.
Diesel engine condition monitoring in the future will require increased focus upon measuring both soot concentration and dispersancy performance. Common methods for measuring soot and dispersancy performance are reviewed below.
Soot Load Measurement
Measurement of soot can be accomplished using a number of different methods. Below is a general review of each:
Thermogravimetric Analysis (TGA)
This widely accepted technique provides the most accurate estimate of the concentration of soot as a percent by weight. The test involves progressively heating the sample in a nitrogen-rich atmosphere over time to vaporize volatile fractions until the weight of the sample levels off, typically occurring at around 600º C.
Then, the nitrogen environment is replaced by air and the temperature is further raised allowing the oil to oxidize until the weight again stabilizes. Soot concentration is then calculated by subtracting the weight of the volatile ash components from the weight of the original sample. While this technique is accurate, it is strictly a research level laboratory method and is very expensive, usually costing around $200 per test.
Infrared Analysis
Infrared Analysis has become very popular for measuring soot concentration. Results seem to correlate very well with TGA and the technique is relatively low cost, especially with the proliferation of labs now offering Fourier Transform Infrared (FTIR) analysis. There are also several reasonably priced on-site instruments available for soot measurement.
Essentially, soot absorbs infrared energy. Unlike many parameters measured with FTIR, soot creates a broadband change in absorption (baseline shift). So, FTIR instruments generally search for soot in 2000 wavenumber region. That region is relatively clear of interference from other oil constituents or contaminants making soot measurement relatively easy.
The primary interferences related to this method include the disproportionately increasing absorption of infrared energy as soot particles increase in size, and other particles, like dirt, also absorb broad-band infrared energy and are indistinguishable in measurement from soot.
Insolubles Test
This test involves the separation of insolubles from the oil after it has been mixed with various solvents like pentane and toluene. The pentane or toluene insolubles are removed by high-speed centrifugation or by filtration onto a membrane disc. When centrifuged, the insolubles are measured as either mass or volume.
When filtered, the weight of the new filter is subtracted from that of the prepared filter to determine weight. The technique is relatively inexpensive and very well established. The main drawback is that all insolubles are measured together, not just the soot. Also, the solvent selected affects the outcome. If pentane is used, organic oxides are included in the measurement of total insolubles. Toluene leaves the organic oxides dissolved.
Light Extinction Measurement (LEM)
The LEM method, researched by Analysts, Inc., method involves casting light at the visible and near infrared frequencies through an object area containing a volume of oil. The light obscured by the oil, as measured by the voltage drop across the object area, is purported to vary with soot concentration. This technique offers simplicity, low cost and a quantitative result.
The major drawback lies in the fact that anything that blocks or scatters light is subject to inclusion in the soot estimate (e.g., particles, water, air bubbles, insoluble oxidation by-products, etc.).
The Blotter Method
This sample method requires only a drop or two of oil on standard chromatography paper. The insolubles separate from the oil and provide a quick visual identification of soot. Further, the paper can be diluted in different solvents to provide an indication of the different insolubles present in the sample.
The blotter method offers elegant simplicity, but fails to quantify soot concentration. However, a trained eye can estimate concentration given enough experience; but still, any quantification of soot load must be viewed as suspect.
Dispersancy Measurement
Unlike measuring soot concentration where numerous options exist, measuring dispersancy performance is a real challenge to the analyst. There are two ways to approach the issue: one can attempt to measure the concentration of the dispersant additive itself, or one can measure the dispersancy performance of the oil. For routine used oil analysis, the latter offers a much more promising solution.
While the blotter test offers limited value measuring soot concentration, it provides an excellent assessment of the lubricant's dispersancy performance. An oil that is properly dispersing soot and other insolubles produces an evenly graduated blotter (see Figure 6A).
A blotter indicating a high soot load, but even graduation, suggests the oil is still fit for service, but should be watched closely for degradation (see Figure 6B). When dispersancy begins to fail, the insolubles begin to form a dense ring on the exterior of the absorbing oil drop as seen in Figure 6C.
Figure 6D indicates the characteristic dense black dot and sharp periphery that forms when the oil completely loses dispersancy performance. From a maintenance perspective, when the ring begins to form around on the exterior of the oil blotter, it is time to look at scheduling a drain.
If the black dot is allowed to form, the situation is problematic because the undispersed portion of soot that has deposited upon surfaces will not be removed by the oil change. Often, several changes made at frequent intervals will be required to effectively scour the engine clean. Also, if dispersancy performance degrades at an unusually rapid pace, a more extensive review of combustion and ring performance should be undertaken.
![]() |
Figure 6 – Blotter A shows good dispersancy, blotter B shows high soot load with marginal dispersancy, blotter C shows high soot load and failing dispersancy, blotter D shows failed dispersancy.
|
Looking forward, oil analysis programs will have to increasingly combine monitoring of both soot load and dispersancy. Clear limits for soot have not been established. However, according to one industry expert the lubricant manufacturers will need to inform operators of the acceptable condemning limit for soot load.
A cautionary limit should also be set at about 50% of the condemnation point. While dispersancy performance will play an increasingly important role in the proactive condition monitoring process to ensure that the lubricant is operating properly, soot load must be carefully trended too. Should dispersancy suddenly fail in a heavily loaded engine, agglomeration occurs rapidly, and it’s too late.
Conclusions
Since EPA regulations have and will continue to force the crankcase lubricant to serve as the "trash can" of the combustion process, we in the oil analysis business must respond with more aggressive and informative monitoring of soot and dispersancy performance. The engine oil analysis program of the future must combine routine measurement of the soot concentration with routine measurement of dispersancy performance.
Measuring one or the other is not sufficient, especially if your organization seeks to extend oil drain intervals. New and improved methods for measuring soot concentration and dispersancy performance are required for lab, depot level and on-site oil analysis to ensure engine reliability under the EPA's strict new emission requirements.
References:
1. Lubrizol On-line Reference Library (1998) "New Emissions Standards for Heavy-Duty Diesel Engines".
www.lubrizol.com.
2. Desjardins, J. and W. Seifert (1994) "Soot and Your Diesel Engine”. Lubrication System, Proceedings of the Joint Oil Analysis Program (JOAP) Conference.
3. PC-9 Development Notebook, Infineum, 1999.
4. Donnet, J., C. Peng and T. Wang (1997) "Scanning Tunneling Microscopy Study of Lubricating Oil Soots", Carbon Vol. 35, No. 6, pp. 853-854.
5. Bondi, A. (1951) Physical Chemistry of Lubricating Oils, Reinhold, New York, New York.
6. Lubrizol On-line Reference Library (1999) "How Base Oil Affects Soot Mediated Oil Thickening".
www.lubrizol.com.
7. Instrument Review - "The Soot Meter for Condition-Based Maintenance", Practicing Oil Analysis Magazine, September/October, 1998.
8. Mansfield, C. (1999) - Email exchange between Dr. Clifton T. Mansfield, of Equilon Corp., and the author.
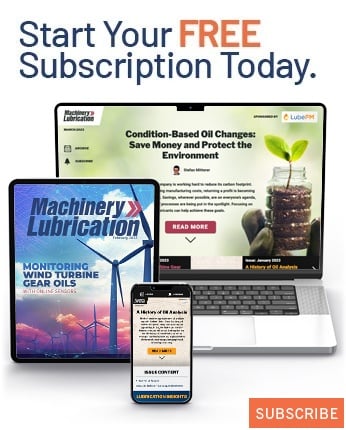