P&H MinePro Services Predictive Diagnostic teams provide condition-monitoring programs to mobile mining equipment throughout North and South America. The services include on-site oil analysis, vibration analysis, infrared thermography, passive ultrasonics and off-line motor testing.
One of the most noticeable improvements resulting from the diagnostic team’s program was increased oil cleanliness, which is important in the aggressive mining environment. The following case study discusses a water contamination issue and some surprising results from the oil lab.
The Problem
The transmission in question is one of two planetary swing transmissions on a 2800XPA electric mining shovel (Figure 3) at an open pit copper mine in New Mexico.
This was the second monthly testing of this transmission. In June 1997, an oil change was recommended due to an improper grade of lubricant being used.
In July 1997, increases in the indexes of iron from the CSI Oilview on-site oil analysis equipment 5100 and 51 FW were noted with some concern.
Vibration analysis showed no problems with the transmission and no changes from testing the previous month. An oil change was recommended, and information regarding maintenance actions performed between the June and July visits was requested. The oil sample was sent to an outside oil lab for a more detailed analysis.
A Possible Cause
Discussion with maintenance personnel indicated that an oil change had recently been performed following the previous recommendation. An oil sample was drawn from lube trucks from both of the mines. Oilview testing indicated possible water contamination. A visual crackle test verified the presence of water contamination in the lube trucks.
The mine indicated that the source of the water was probably the wash rack, where the lube trucks are regularly washed off using a high-pressure washer. In the past, the trucks were washed with the tank vents open, allowing water into the lube tank. The oil in this transmission was changed and the lubrication staff was informed of the importance of keeping water out of the lube tanks.
The outside oil lab results came back from the July 1997 transmission sample confirming the water contamination (Table 2).
Diagnostic Message
The lab also provided the following comments: “Suggest immediate inspection of this unit, including resampling to verify results and check for sources of contamination, water ingress into system and wear. Wear debris analysis revealed several abrasive particles (cutting wear ribbons and needles of steel origin) and these should be considered abnormal in nature.”
With these results, the staff determined that the high ferrous and contaminant levels were caused by increased boundary wear due to water contamination.
The Root Cause
Because of the known problem with water contamination, a visual crackle test was performed on each oil sample at the mine during subsequent diagnostic visits. There continued to be a problem with water contamination.
Lubrication personnel were blamed for the problem. P&H checked for other sources of contamination, beginning with sampling a newly delivered bulk storage tank. The results indicated high moisture levels and a contamination source.
P&H approached the lube vendor regarding the condition of the new lubricant and offered to help determine the source of the water. After some investigation, it was found that when the empty storage containers were returned to the oil supplier, they were steam-cleaned prior to refilling.
A new employee was responsible for the cleaning. Apparently after cleaning the tank, the drain valve was closed without ensuring the tank was fully drained and dry. When the tanks were refilled, in some instances there was more than two inches of water standing in the bottom.
The vendor changed its cleaning procedure and the mine started random testing of its incoming lube. There has not been an issue of water contamination since.
Determining Wear
Atomic emission spectroscopy (AES) through the methods of rotating disc electrode (RDE), inductively coupled plasma (ICP) or X-ray fluorescence is useful for capturing evidence of normal wear in the 1 to 5 micron range, but the particle size upper limit is approximately 10 microns.
Consequently, advanced wear problems (evidenced by large population of particles larger than 10 microns) can be missed when viewed exclusively with the very common RDE spectroscopy method. The rotrode filter (RFS) method enables the lab to more effectively characterize larger particles, characterized as coarse particles. When used in combination, the RDE method characterizes wear debris as fine and the RFS method characterizes wear debris as coarse.
Lube Oil Condition Analysis
2800XPB Electric Shovel
Date: 7/14/1997
System: Front Swing: Transmission - Unfiltered
Problem: Extreme amounts of contaminants and ferrous wear present in the oil.
Analysis
The 5100 oil analyzer measured the contaminant level at 19.6, with the iron level greater than 5000. The 51FW (indicates relative levels of paramagnetic material) measurement was 271. These are dramatic increases compared to previous samples. The ferrous levels could indicate a severe wear problem or component failure. Vibration analysis does not indicate a problem. The system should be flushed to remove any accumulated wear debris.
Recommendation
Drain oil and flush system thoroughly. Replace oil. Report any maintenance action performed to predictive diagnostic team, which will continue to monitor the ferrous levels for any increases.
On-site vs. Off-site Analysis: The Contradiction
During this process, a question was raised regarding the high ferrous levels from Oilview and the low levels of wear metals in the outside oil lab results (see Table 3 above).
The large difference in the results is due to the different methods used for the measurements.
The outside oil lab uses rotrode filter spectroscopy (RFS) to measure wear metals. This method makes use of the fact that the carbon disc electrodes used in rotating disc electrode (RDE) are themselves porous. A fixture is used to clamp the discs so that oil can be drawn through the outer circumference of the discs when a vacuum is applied to the inside of the discs.
The particles in the oil are captured by the disc. The oil is then washed away with solvent, the disc is allowed to dry, and the particles are left on the disc electrode so that they are vaporized and detected when run on the RDE spectrometer.1
This testing method, while extremely accurate for small particles, is limited by the size of the pores on the electrode and is not accurate for particles larger than 10 µm.2
The techniques used by the 5100 and 51FW are based on the electromagnetic properties of the wear particles and are sensitive to particles of all sizes. However, these methods are subject to other interferences that influence electromagnetic properties.
This case study illustrates the difference between providing a single technology service where test results are reported, and providing a multi-technology program where results are confirmed and analyzed to improve the overall condition of the equipment. It also highlights the need to understand the benefits and limitations of the test equipment used in the assessment itself to maximize the value of the information to the end user.
References
- Lukas, M. and Anderson, D. Rotrode Filter Spectroscopy, Does It Have a Place in the Commercial or Military Oil Analysis Laboratory? Spectro Incorporated, Littleton, Mass.
- Lukas, M. and Anderson, D. Analytical Tools to Detect and Quantify Large Wear Particles in Used Lubricating Oil. Spectro Incorporated, Littleton, Mass.
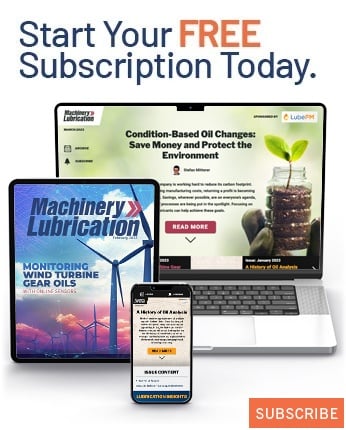