Particles. Think about it. Tribological studies on wear-related machine failure rank particle-induced abrasion as the No. 1 cause of wear. This is often referred to as three-body abrasion, where particles become interposed between two surfaces in relative motion, leading to damage (cutting) of both surfaces. Particles contribute to an assortment of other types of wear and failure too, including surface fatigue, silting and erosion.
With this in mind, it is only natural that monitoring the size and concentration of particles in lubricating oil would be of keen interest to the astute reliability professional. It’s no wonder the particle counter is a leading oil analysis instrument and is high on the list of favored instruments in the condition-monitoring field in general.
Practicing Oil Analysis magazine conducted a review of particle counters being sold into the machine condition-monitoring market. This was no short list, mind you - it included 24 different models that are being offered by 15 different suppliers. How can the condition monitoring industry support so many different instruments at the same time? Perhaps you’ve heard that if something is important, you measure it. Cleanliness is important … hence the reason for such mainstream use of particle counters.
But there’s a flip side to this story. Particles are also the No. 1 consequence of wear and failure. After all, it’s pretty darn hard for a machine to wear and ultimately fail without liberating particles from internal frictional surfaces in the process. So, regardless of the cause of wear, the consequence will always be the same - wear particles. Abrasion, pitting, corrosion, cavitation, scuffing and misalignment are all particle-producing events, but only two on this list are caused by particles.
You can refer to your machine as having a wear debris life. Think of your machine as a pencil. How long does a pencil last? It depends on how long the pencil is and how much you use (and sharpen) it. The same is true with your machine. Its life is defined by how much metal remains and how fast the metal is being removed (wear rate).
In essence, the machine eats itself up from the inside out, little by little, like tread wearing from a tire. Most machines have only a fixed amount of metal to give up. For instance, a 20 gallon-per-minute hydraulic gear pump can wear (lose) only about 100 grams of metal, at which point the pump must be replaced. The loss of these 100 grams could occur rapidly - days or weeks - or very slowly over a period of years. Controlling this wear rate is the central objective of proactive maintenance (reread the first paragraph above).
However, unlike the pencil or tire tread, it isn’t easy to inspect machine surfaces to determine how much metal remains and thus estimate remaining useful life. Therefore, the practical alternative is to look to the wear particles instead of the wear surfaces. But where do these particles go? Many stay locked in the flowing matrix of the oil while others search for a resting place - a final resting place. This of course points to an important condition-monitoring strategy - discovering your machine’s internal debris field.
If your machine’s debris field is primarily in your oil, then sampling the oil can prove essential to trending wear rates and understanding reliability-threatening wear modes. However, there are other debris fields that often go unnoticed and untapped - despite the repository of rich information they might represent. These include wear debris found in the following locations:
-
Filters and strainers
-
Magnetic collection plugs
-
Sediment bowls
-
Centrifuge bowls
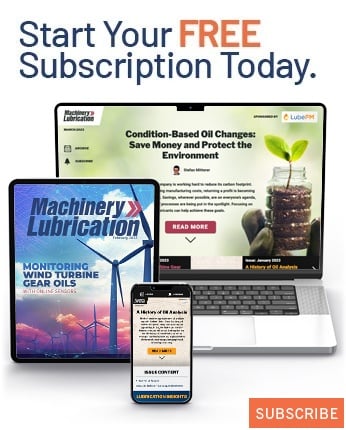