Personnel from a large pulp and paper mill made a surprise visit to the mill oil supplier. The mill scheduled the unannounced visit for the purpose of identifying original conditions for the handling of drums and lubricants. This was an outgrowth of contamination control issues with lubricants delivered to the site.
During the unannounced inspection and audit of the drum cleaner, numerous problems with container cleaning and handling processes were uncovered.
The visit was conducted to assess oil supplier capabilities along three fronts: supplier storage methods, oil supplier lubricant delivery methods, and drum reconditioning and handling methods.
Observations on each criteria are noted as follows:
-
Storage Methods
- Empty and full containers are stored exposed to weather and environmental contamination.
- Storage tanks are located on a gravel drive and near railroad tracks, exposing stored lubricants to exhaust fumes and road dust.
- Storage tanks have open gooseneck vents with no filtration.
- Empty containers are stored outside, exposed to weather and temperature changes.
- Storage tanks provide no method or means of filtering stored lubricants.
-
Oil Supplier Lubricant Delivery Methods
- Bulk truck tanks and drum containers are exposed to atmosphere.
- Bulk delivery trucks have only a 50-micron screen filter that is changed weekly.
- Bulk trucks have no effective breather elements.
- Bulk trucks used to deliver lubricants are also rented to other sites to transport unknown substances.
- Transfer pipe fitting and caps are in many cases missing or very dirty.
- Transfer hoses are in some cases left open.
- Oil transfer pumps and hoses are used for a number of differing types of lubricants.
- Barrels are filled in a less-than-ideal environment.
- Procedures and methods are not always clearly posted, and are unreadable in some cases.
- There are no methods present to test for moisture or solid contaminants.
-
Drum Reconditioning Methods
- Drum conditioner used one charge of flushing water for an entire day’s work.
- There is no focus on container contamination control beyond visual inspection.
- Cleaned drums are stored inside a shed, face down as a contamination prevention method.
- Specifications for cleaning and testing are not available from the drum reconditioner to the lubricant supplier.
Results from the Audit
Since the audit and discussions with the supplier/distributor, the mill has seen marked improvement in cleanliness of bulk oil deliveries. All deliveries are now sampled at the time of delivery for testing at a later date, with intentions of installing on-site analysis equipment to test oils before the oils are off-loaded.
The distributor indicates that filters were installed on bulk tanks to improve the quality of lubricants stored on-site. Improvements in the methods for internal handling of lubricants and filtration of lubricants during transfer from bulk to smaller containers have contributed to significant overall improvements in cleanliness and condition of new lubricants.
Mill mechanics have been involved in these upgrades and have received training on the need for improved lubricant handling.
Recommendations from this exercise: Audit your oil supplier and drum reconditioner routinely. Establish clear parameters and work with the supplier to help them achieve the improvements that are necessary. Then, expect the oil supplier to conform to new, higher quality expectations. Continue to include mill mechanics and lube technicians, and provide training to reinforce the necessity and benefit of these new measures.
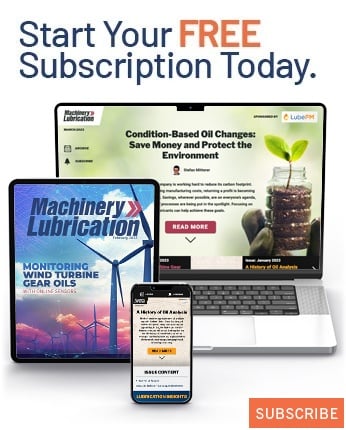