The various sections of a modern papermaking machine expose about 1,500 different bearings to harsh conditions including water, heat, steam and paper dust. Each section has special lubrication requirements.
Figure 1. High-speed Papermaking Machine
A modern papermaking machine can be larger than 10 meters (33 feet) wide, 20 meters (66 feet) high, and the length of two football fields. Each huge machine consists of at least four distinct sections - a forming or wire section (often called the “wet” section), a press section, a drying section and a reeler.
Different types of machines process an assortment of papers, and speeds can range from as low as 100 meters (328 feet) per minute for some pulp-drying machines to 2,200 meters (7,218 feet) per minute for the fastest tissue machines.
While acknowledging that there are differences in lubrication requirements based on variations in products and machine speeds, there are still general guidelines to a mill’s operations and engineering personnel regarding how to correctly lubricate the bearings in each section.
Forming Section
Pulp entering the first section of a paper machine, the forming section, is about 99 percent water. By the end of the forming section, the water content has to be low enough to make the paper web self-supporting as it moves into the press section (Figure 2).
Figure 2. The Forming or Wire Part of a Fourdrinier Machine.
The Original and Most Widely Used Type of
Paper-forming Unit.
Various types of forming sections, most running between 900 and 2,500 meters (2,953 and 8,202 feet) per minute, operate in today’s paper mills. Whatever the type and speed of a forming machine, its bearings are exposed to large amounts of water.
Thus, heat usually is not a factor in selecting a lubricant and lubrication method for a forming section. For the most part, bearings in a forming section should be lubricated with grease. The grease lubricates the seals, keeps water out and purges contaminants, especially water, from the bearings.
A good procedure for lubricating bearings in the wet section is to use an automatic system that pumps a predetermined amount of grease per day into each bearing. This procedure ensures that a fresh amount of grease purges the bearings on a regular basis.
Sometimes, mill personnel choose oil rather than grease for lubricating bearings in the wet section. This may occur for one of a number of reasons. For example, in relatively high-speed forming sections, elevated operating temperatures may require excessive grease for relubrication. The right oil may be more economical and less messy.
Or perhaps there are other oil-lubricated bearings nearby. With an oil system present in the area, it might be used instead of grease. When one selects oil lubrication, bearing seals must be selected to suit that lubrication medium.
For spherical roller bearings as well as for toroidal, nonlocating bearings (marketed by SKF® as CARB® bearings), oil lubrication is actually the preferred lubrication method when the speed is 50 percent or higher than the selected grease’s speed rating.
In general, though, the best choice for a bearing lubricant for the forming section is a high-quality grease with synthetic thickeners and outstanding water-repelling properties. Protection against corrosion also has top priority for bearings in a forming section. Therefore, the lubricant - grease or oil - must have good rust-inhibiting properties.
Press Section
The purpose of the press section is to remove additional water from the paper web, which enters the section with a water content of about 80 percent (Figure 3).
Figure 3. Valmet Sym-Press Press Section with Multiple Nips
Pressing is a much less expensive way than steam heating to remove water from the paper web. Consequently, the pressing process on paper machines is being extensively developed. For example, high-temperature pressing (also called impulse drying) is gaining in popularity because it produces a dryer paper web and can improve paper quality as well.
Plain press rolls are sometimes called “solid press rolls,” although they are not always solid. Heated press rolls are becoming more common, and extensive developmental initiatives are underway to find the optimum design and heating temperature for heated rolls for specific grades of paper.
Typically, in the press section as in the forming section, water is the problem; heat is not. However, heated rolls, high-temperature pressing and high speeds will compound lubrication problems.
Thus, both grease and circulating oil are commonly used for bearings in the press section. The type of lubrication selected is usually a function of the size and speed of the bearings and the rolls on which they are found.
For grease lubrication, multistage labyrinth seals help keep water out and protective covers help prevent the entry of water during hose downs.
Circulating oil is usually specified for large bearings that rotate relatively fast - a situation in which grease can cause skidding problems. Also, in high-speed paper machines the frictional heat in the large bearings on the press rolls can be high enough to require that large quantities of circulating oil pass through the bearings to dissipate the heat.
A low oil inlet temperature, obtained using a cooled tank in a separate system, may help maintain the required viscosity. In a press roll bearing lubricated by a circulating-oil system, a flinger will prevent oil from escaping from the housing, while radial labyrinths will keep out the water. Whatever the lubricant, rust inhibitors should be part of its formulation.
Within the press section, felt rolls carry the felt that absorbs and conveys away the water in the paper web. Spherical roller bearings and toroidal, nonlocating bearings are recommended here as is oil lubrication.
There are several reasons for using oil with felt rolls. One is that if grease lubrication were employed for the bearings of high-speed machines, the operating temperatures would be so high that regreasing would be required much too often. Then, excessive grease could contaminate the machine.
Another reason for using oil on felt-roll bearings is that there are surely other oil-lubricated bearings nearby. Demands made on the oil by the felt-roll bearings are not as great as the demands on the oil for the press-roll bearings.
Therefore, the same oil can be used for felt-role bearings as is used for the press rolls, provided it was correctly selected in the first place.
Be aware that seals for oil-lubricated bearings are normally not as efficient as the multistage labyrinths used for grease-lubricated bearings. However, seals for oil-lubricated bearings in the press section have to be equally efficient due to their exposure to water during operation and hosing down.
Dryer Section
When the paper web leaves the press section, the water content is typically between 50 and 65 percent. It then enters the dryer section for the removal of more water, down to 5 percent to 10 percent.
Bearings in the dryer section are exposed to high temperatures over long periods. Thus, the operating conditions for these bearings are quite severe. Constantly increasing demands brought about by larger, faster machines and higher steam temperatures will add to the challenge on the lubricant and lubrication delivery system.
A dryer section might have several kinds of rolls, three of which are described here (Figure 4).
Figure 4. Traditional Dryer Section
First, there are drying cylinders that carry the paper web and are heated by steam. Depending upon the product and the machine’s speed, the temperature of the steam used to heat drying cylinders varies. But in many cases, even when the journals are insulated, the bearings can see temperatures as high as 125°C (257°F).
Like the press section, the dryer section also has felt rolls carrying felt along the surfaces of the progressing paper web. Also, there may be Yankee cylinders in the dryer section. They are used for drying tissue and board.
A Yankee cylinder is normally 4 to 6 meters (13 to 20 feet) in diameter but can be as much as 9 meters (30 feet) in diameter. It is designed for high-pressure steam at more than 200°C.
One or two press rolls, positioned below the Yankee cylinder, press the web against the cylinder. The paper adheres to the heated cylinder, and it is dried by the heat from the cylinder and by hot air blown onto the outside of the web.
The bearings in all of these rolls and cylinders are, of course, lubricated by circulating oil, and the general oil requirements for the section are dictated by the requirements of the drying-cylinder bearings.
Achieving proper lubrication of drying-cylinder bearings requires large quantities of water-free oil of the appropriate viscosity. In modern machines with insulated journals, it is usually possible to cool the bearing to temperatures below 90°C.
Because so many factors influence the calculation of the requisite oil flows, these must be determined for each individual dryer section. Many bearing and lubrication suppliers can perform computer analyses to aid papermakers with this determination.
Typically, circulating oil from the system that lubricates the drying-cylinder bearings lubricates the felt-roll bearings in the dryer section.
However, a separate circulating-oil system is recommended for Yankee-cylinder bearings, for which operating conditions are similar to those of drying cylinders but the rotational speed is usually lower, as is the ambient temperature.
As with drying cylinders, effective journal insulation is recommended for Yankee-cylinder bearings.
Reeler
Most large paper machines produce a continuous paper web 8 to 10 meters (26 to 33 feet) wide (Figure 5).
Figure 5. Reeler
This web must be cut and made into smaller rolls before the paper is distributed to customers. The first reel or spool of paper is created on the reeler at the end of the paper machine.
When the roll of paper on a reel reaches the desired diameter, reeling is continued on a new spool. The jumbo roll of paper, which may weigh as much as 100 tons, is then transferred to a slitter and rewinder where it is cut to the width required by the customer and rewound into rolls for shipping.
The principal bearings in the reeling operation are those on the reel drum, which feeds the paper web onto the spools, and those on the reel spools, onto which the paper web gets rolled. Compared to the other sections of a paper machine, the bearings in the reeler operate in a relatively good environment: dry and about 25°C. Still, these bearings must be protected from paper dust.
Reelers are relatively slow-running machines, and in most of them grease is used on the reel-drum bearings. However, circulating oil is becoming more common as a lubrication method for these bearings, and when a circulating-oil system is used, it is often the same system used for the drying-cylinder bearings.
In this case, care must be taken to ensure the oil is adequate for both applications. The bearing arrangements for reel spools are usually lubricated with the same grease as that used for the forming and press sections. Relubrication should be carried out about once a month.
The preceding are general guidelines for the correct lubrication of papermaking machines. Special circumstances - unusual products, high speeds, requests for more throughput from the same equipment, etc. - may require appropriate adjustments.
Good practices for paper mill production and maintenance personnel include ongoing interaction with bearing and lubrication suppliers regarding appropriate lubrication products and techniques, being wary of so-called “miracle lubes” and being aware of common paper-machine lubrication problems and how to solve them.
Common paper-machine lubrication problems and their solutions will be addressed in an upcoming issue of Machinery Lubrication magazine.
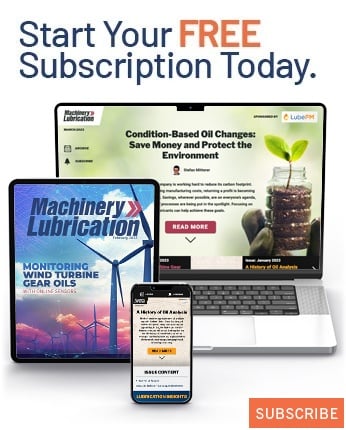