The plastics products division of Clopay Corporation in Augusta, Ky. recently installed a new film winder - a piece of equipment used to form finished rolls of plastic film products.
Principle sections of a winder include the finished roll shafts, driven pull nips, layon and tension control system. On this particular winder, there are two pull nip sections. The pull nip consist of one driven metal roll, located directly above a rubber-covered roll that when closed, creates a nip that pulls film through it.
Each pull nip has a gearbox reducer motor with an oil capacity of approximately three quarts. The winder manufacturer recommended using a synthetic ISO VG 460 (AGMA 7) oil while the gearbox label specified a synthetic VG 680 (AGMA 8) oil.
We chose the recommendations of the winder manufacturer because we believed the manufacturer better understood the application. Prior to start-up, we flushed the gearboxes with a cleaning solution, installed a nontoxic synthetic VG 460 worm gear lube, desiccant breather, sight glasses, and stainless steel piping.
Figure 1. Upper Nip Gearbox
Preventive Maintenance Discoveries
Upon start-up, preventive maintenance (PM) checks consistently found both gearboxes were running abnormally hot. An infrared (IR) heat gun was used to determine the following temperatures with VG 460 synthetic worm gear lube:
- At 40 percent speed, the temperature was 110ºF.
- At 80 percent speed, the temperature was 167ºF.
Keep in mind the actual temperature of oil inside a gearbox could be 15 to 20 degrees higher than exterior surface temperature.
Why were the temperatures so high? One possibility was that flushing the gearboxes with a seven-viscosity flushing solution may have left some flushing solution residue in the gearbox. Could mixing the flushing solution with the VG 460 gear oil have drastically reduced the viscosity? An oil sample was sent to the lab for analysis. The results showed normal lubricant condition; however, excessive amounts of copper indicated bronze gear wear.
Temperature Variations
We then decided to go with the original equipment manufacturer (OEM) recommendation, which was synthetic 680. To test this, we drained one of the two gearboxes and installed the 680. Upon start-up, we had the following temperature readings:
- At 40 percent speed, the temperature was 105ºF. A decrease of 5ºF.
- At 80 percent speed, the temperature was 177ºF. An increase of 10ºF.
These results indicated a strong possibility that heat was being generated from viscous churning losses, which would indicate the need for a lower viscosity lubricant. The next step was to test this theory by utilizing a lower viscosity lubricant. We drained the 680 and replaced it with 320 nontoxic sythentic worm gear lube. The results were:
- At 40 percent speed, the temperature was 100ºF.
- At 80 percent speed, the temperature was 152ºF. A decrease of 25ºF.
The results determined that the recommended viscosity was not suitable for this application. We contacted the manufacturer to discuss concerns over the warranty. With a company representative, we took temperature readings, with the VG 460 still in one gearbox and the VG 320 in the other. The representative, as well as Clopay personnel, was astonished at the difference in temperature, but agreed we should continue using the VG 320. He assured us in writing that the manufacturer would honor the warranty as before.
Lessons Learned
The rule of thumb is to increase viscosity when excessive heat is generated; however, due to churning, the opposite worked. The gearbox representative stated that the manufacturer, when asked, will put onto the label any oil designation the customer requests.
He was open about the manufacturer not being a lubrication expert. Clopay personnel assumed this meant that in new applications, that a facility needs trained people capable of determining the appropriate lubricant for a particular application. They also need to know what checks should be performed.
I am certain that in this situation, had there been no one at Clopay who had taken a Noria lubrication training course, we would have changed out many gearboxes before finding the root cause of gearbox failure. We would have experienced much unnecessary downtime on a machine that is critical to us and our customers.
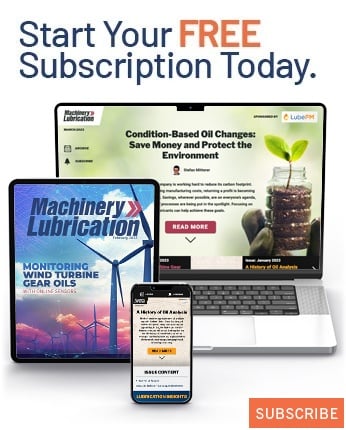