In 2002, Westar Energy made the decision to aggressively implement a lubrication management program throughout its six plant facilities. Management recognized that change needed to start with education and training.
With the oil analysis program in need of overhaul, oil analysis training began for predictive maintenance (PdM) technicians, operators, mechanics and supervisors. Westar capitalized on what its employees learned and with continuing education, has seen big successes company-wide.
The primary motivator behind this new philosophy was the need to move from a time-based to a condition-based maintenance practice to reduce costs, and maintain and improve reliability at a much lower cost.
Prior to 2002, free vendor oil analysis was being used on a small portion of the plants’ equipment. Oil analysis results were not fully understood and were primarily used as a flag to change the oil in a particular machine.
The oil analysis program started out using a professional off-site lab and quickly evolved to an in-house program consisting of seven PdM technicians who are actively involved in the oil sample collection and data analysis process. Management realized that to reach a high level of reliability and confidence in the oil analysis program, education for all plant personnel would be key.
The Beginning
Westar’s first step was to identify a professional lab to process and analyze oil samples. The professional lab helped select the type of tests to be run on the plants’ different machines. Equipment data sheets were filled out for each plant’s selected critical equipment.
At this point, Westar personnel were confident that samples would need to be collected and sent to the professional lab only once a month. Personnel would then merely wait for the reports. Obviously, it was assumed that the reports would be clear and would provide advice and/or recommend the actions for any problems.
Because plant personnel had no real education about where oil samples should be taken or how they should be collected, it is easy to understand why they were confused when the reports began to come back as marginal or critical.
These results caused Westar to seek advice from the professional lab, which could base recommendations only on the test results and could not take into account whether the oil sample collecting methods were correct. The possibility of a false positive or negative was high.
Phase Two
After several months into the program, Westar questioned whether there would be advantages to an in-house oil analysis program. When the company compared the cost of sending roughly 280 samples to the off-site lab each month to the cost of performing some of this analysis on-site, a definite savings was suspected.
Also, the ability to react quickly to a possible problem with results in less than an hour compared to 24 or 48 hours for off-site testing was attractive. When actual costs were compared to the payback, Westar was convinced that it would be advantageous to implement an in-house oil analysis program, where oil samples could be screened and analyzed and only questionable samples sent to the professional lab.
Westar chose the Emerson Process Management - CSI 5200 minilab for its in-house laboratory. The 5200 works in conjunction with Westar’s vibration analysis software. Test results can be seen and analyzed by many people at any of the plant locations through a wide-area networking software application (Figure 1). It was at this point that the company realized education in oil analysis and lubrication management was essential to a successful program.
Figure 1. Typical Plant Network Link
Education
On-site training from the professional lab covering basic oil analysis took place in March 2002. In April 2002, Noria conducted formal oil analysis training, which was attended by maintenance and operations personnel, supervisors and PdM technicians. The training provided an understanding of the importance of lubrication to machinery reliability, health and extended component life.
Those who attended the training learned basic key components that were implemented immediately, such as:
- Proper sampling locations
- Proper sampling techniques
- Types of tests for particular machinery
- Alarming schemes for different parameters
- Analysis and interpretation
The PdM lab technician responsible for processing the samples through the on-site lab received more specific training.
Implementation
Once training was completed, primary sampling locations were identified on all equipment being tested and the installation of valves and ports began. One person was assigned to process the samples through the in-house oil lab. The primary people responsible for pulling samples were trained on proper sample-gathering techniques.
For those locations where sample valves or ports could not be immediately installed, installation was scheduled during an outage. On those machines where samples would be pulled from a reservoir, personnel developed a metal insert tube to be used as a guide for controlling the depth and location of the plastic tubing. This method ensured an accurate and consistent method of acquiring these types of samples.
The next challenge was to determine the type and frequency of tests to be performed on each specific type of machine. By understanding the in-house lab information, the lab technicians were confident they could detect the health of both the lubricants and the machines. This allowed them to strategically identify the tests that would need to be conducted by the off-site lab.
By referring to the written material from training, the tests that would enhance Westar’s overall testing scheme were determined. From this assessment, monthly in-house lab tests for each piece of equipment were identified, along with a complementing backup, quarterly and yearly testing scheme from the professional lab.
In-house Monthly Oil Analysis
On-site oil analysis is performed monthly for selected equipment from all plant locations. An analyst at each plant analyzes the data from each oil sample. There are three main vectors for analysis: chemistry, contamination and wear.
Dielectric count, ferrous and nonferrous index, particle count, water content and wear debris analysis are performed. If the lab technician finds any abnormality, the affected plant PdM representative must be notified through e-mail and a phone call.
The plant PdM representative further investigates the possible problem. A resample of the oil may be requested to either verify the analysis results or to be sent to the professional lab for further analysis.
Working closely with the professional lab, report files that can be dumped directly into the in-house lab software were developed. Here, test information can be viewed and tracked by company personnel.
Off-site Oil Analysis
In addition to the monthly in-house oil samples, oil samples are sent to the professional oil lab every three months for additional testing that the in-house lab cannot perform. These test results are downloaded into the in-house database for trending and analyzing. These tests include: elemental analysis (atomic emission spectroscopy), Fourier transform infrared spectroscopy (FTIR - infrared analysis) and acid number (AN).
Once a year, additional samples from critical machines are sent to the professional lab for rotating pressure vessel oxidation tests (RPVOT) and demulsibility tests. An off-site oil lab may also be used to ensure the oil program stays up to date when the lab personnel are on extended vacation or the lab is out of service. These test results are downloaded into the in-house database for trending and analyzing. These tests include: viscosity, particle count, wear particle concentration and crackle test.
The analyst at each plant is responsible for reviewing the oil analysis results, determining any abnormalities, determining the urgency of repair for any oil-related problems, creating oil reports and work requests, and any follow-up work that may be needed after repair work has been performed.
Alarming Scheme
After referencing the training material once again, Westar began to apply alarm levels to the different types of testing parameters. Training recommendations and historical sample data were used to set up an alarm scheme that would be both effective and logical based on the plants’ current lubrication and equipment health conditions (Figure 2).
Figure 2. Oil Limits and Alarms (In-house Lab)
Initially, personnel were careful not to set alarm limits that could not be achieved. However, as machine improvements and conditions changed, the alarm limits were adjusted. Two-wheeled filter carts are being purchased to address high particle counts and water in closed systems.
Oil Analysis Reporting
As oil analysis is performed and results reviewed, reports are written for oil and/or equipment abnormalities (Figure 3). These reports are then e-mailed to the proper plant personnel. Those receiving the reports may include, but are not limited to, all PdM personnel, plant managers, directors, engineers, supervisors and crews responsible for the equipment. These reports are also attached to the CMMS work request.
Click Here to See Figure 3. Sample Trend - All Data
Program Audit
Once the oil analysis program was up and running, the problems that were revealed provided evidence that the plants’ lubrication practices needed to be addressed. Westar arranged for Noria to perform an audit at one plant site, knowing that the problems identified there would be consistent throughout the fleet. The audit identified strengths and weaknesses in the areas of oil analysis and lubrication management.
Westar’s oil analysis program proved to be strong as a whole; however, lubrication management was found to be equally as weak. This audit was effective in capturing management’s interest. Immediately after the audit, one plant began work on the implementation of a lubrication team. This team would be responsible for establishing lubrication procedures and oil-handling techniques, PMs, changing and adding oil to machines and greasing components.
Many different people performed this practice throughout the plant, which made it difficult to capture detailed lubrication functions that were being performed on any particular piece of equipment. Improvements to the oil storage areas to protect lubricants and provide a first-in, first-out system are being implemented. In addition, oil handling containers were purchased to ensure better contamination control when delivering lubricant from bulk storage to the machine.
More Training
Once the lubrication team was in place, additional training was scheduled. The lubrication team and other plant personnel attended Noria’s Oil Analysis I training. Once again, this provided more education to plant staff on both the importance of lubrication management and what the company was trying to achieve.
Internal Audit
Once internal employees had a fairly good understanding of oil analysis and lubrication management, the company selected a few individuals to perform a lubrication audit, similar to the one performed by Noria, at the other remaining plant sites within the company.
Although this audit was not as detailed as the Noria audit, it identified the basic and most common faults found throughout the fleet. Storage and handling, temporary storage tanks, sampling techniques, contamination control at the machine, procedures and predictive maintenance were reviewed. These audits stimulated positive changes at the audited sites.
Oil Analysis Results
Westar Energy has realized the benefits of its oil analysis program. Varying anomalies have been detected through the in-house lab. These cases include water issues in turbine and boiler feed pump lubrication. Having the information available on-site allowed for a quick response to entrainment issues before valve or system problems were experienced. High ferrous particle count in some of the gearboxes prompted an investigation and a switch to a higher viscosity oil in these components to reduce the wear rate.
Nonferrous materials that pointed to worn and damaged bearings and gears were also detected. Mixed oils were detected through viscosity analysis, enabling a quick reaction before any damage could occur.
The professional lab support has also been a key element for exception, quarterly and yearly testing. Through AN, RPVOT, elemental, FTIR and demulsibilty testing, a better understanding of the current fleet lubrication condition was acquired. The number of generated work requests based on oil analysis indicates how well the program is addressing oil-related issues (Figure 4). This is proving to be extremely beneficial in improving reliability and extending machinery life.
Figure 4. Westar Energy Monthly PdM Tasks Created by Oil Analysis
Lubrication Management
Presently, Westar’s lubrication management is in the process of being drastically improved. Management and plant staffs are committed to addressing the problems identified. Main storage facilities issues are being addressed through new construction or different locations. Inventory is being reviewed along with a first-in, first-out system to prevent old products from being put into service.
Containers for lubrication handling are being purchased and properly marked to eliminate contamination issues. Preventive maintenance procedures are being written to address lubrication as a stand-alone task.
Conclusion
Westar Energy has made great efforts to improve its lubrication and oil analysis program. Although the program is young, it has produced favorable results in addressing machine and lubrication problems.
The key element to success so far is directly related to education about lubrication management and oil analysis. Plant management, who now have knowledge in lubrication, provided additional support and cleared the path for further budgetary improvements. Educating the workforce helped diminish the “oil is oil” myth, creating a smooth transition for present and future changes.
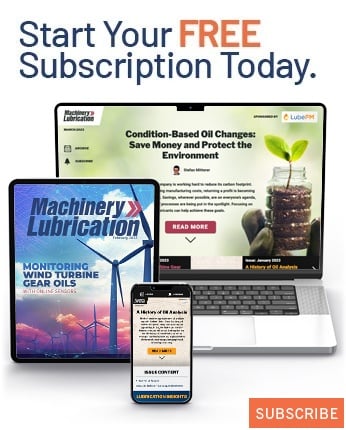