In fluid systems, the fluid acts as a repository for component wear debris, fluid break down products and contaminant ingressed from outside the system. Thus, evaluating debris in hydraulic, lubrication and other fluid systems can provide valuable information about abnormal contaminant ingression, accelerated component wear, impending component failure and/or fluid break down.
While a number of techniques have been developed over the years for monitoring debris in aircraft engine lubrication systems1 and aircraft hydraulic systems, filter debris monitoring has gained increasing acceptance over the last decade or so.
Numerous studies evaluating aircraft engine lube system filter debris, including debris morphology and chemical composition, via energy dispersive X-ray fluorescence (EDXRF) spectroscopy or energy dispersive X-ray (EDX) emission spectroscopy, have been reported.2, 3, 4, 5, 6
The advantages of employing filter debris analysis include: the full-flow nature of the filter element allows all the fluid in the system to pass through the filter element; the coherent surface for capturing fluid system debris efficiently, over time, results in a high concentration of debris compared to debris in the fluid or in magnetic plugs/chip detectors; and the filter element retains debris of all types (metallic and nonmetallic).
In current filter debris analysis methods, the debris is removed from the filter element onto an analysis membrane by back flushing with solvent or solvent-air mixture, by ultrasonic removal in a solvent, or by flushing debris off the filter element with a solvent.
The debris collected on the analysis membrane is evaluated for amount, size distribution and morphology. The chemical elemental composition is determined by EDXRF spectroscopy or SEM-EDX and by infrared (IR) spectroscopy for organic contaminants.
The Diagnostic Filter System
A new diagnostic filter system, comprised of a diagnostic filter element having a pull-out diagnostic layer and a custom-designed contaminant analyzer, that allows for on-site analysis of debris captured on the diagnostic layer, is in development.
The diagnostic filter system is comprised of two components: (1) the Dirt Alert® filter element, which features a pull-out diagnostic layer, and (2) the contaminant analyzer for the evaluation of the chemical composition of the filter debris via EDXRF spectroscopy.
The diagnostic layer can be easily removed on-site for convenient visual inspection of the captured debris. The porosity of the diagnostic layer can be adjusted, within the constraints of the regular filtration medium pack, so that the captured debris is appropriate for diagnostics.
In the current configuration, the Dirt Alert diagnostic layer exhibits a particle capture efficiency of more than 95 percent for particles 70 m or larger, and an efficiency of about 60 percent for particles 30
m or larger.
The contaminant analyzer provides semiquantitative information about key chemical elements of interest, and is designed to be a rugged device for field use. A prototype of the contaminant analyzer, known as the DLA, depicted in Figure 1, accepts analysis membranes, sections of Dirt Alert diagnostic layers, and filtration media.
No solvents or wet chemistry are required. Because the analysis is nondestructive, additional evaluation of the filter debris may be performed. It should be noted that the prototype, shown in Figure 1, was fabricated with existing hardware and does not represent the final envelope/configuration; the final envelope is expected to be significantly smaller.
Figure 1. Prototype of Contaminant Analyzer (DLA) Showing
a Section of Dirt Alert Diagnostic Layer Installed for Analysis
A preliminary evaluation of the prototype DLA was conducted using Dirt Alert diagnostic layers and filtration media from filter elements from the field, and Dirt Alert filter elements artificially contaminated in the laboratory. A discussion of the evaluation and results follows.
Calibration Considerations
Because EDXRF spectroscopy is sensitive to the size distribution of the analyzed debris as well as matrix effects, the calibration of the EDXRF analyzer is important for semiquantitative debris analysis. Two types of calibration materials were evaluated in this study:
-
Micromatter standards, fine uniform solid calibrants, typically used as calibration standards for EDXRF spectroscopy.
-
Metal powders, metal oxides, or other chemical compounds, with a broader size distribution that may be more representative of contamination in the field.
Homogeneous suspensions of the calibration materials were prepared in MIL-H-5606 hydraulic fluid at different concentrations, in the range of 0.5 mg/L to 20 mg/L. The suspensions were drawn down through 0.8 m rated cellulose acetate analysis membranes to provide a uniform dispersion of the calibration material on the analysis membranes. These membranes were then subjected to EDXRF analysis with the DLA prototype to establish the required calibration curves.
The calibration curves for iron and molybdenum were similar for both the Micromatter standards and the granular powders; however, the calibration curves for the other chemical elements differed significantly, indicating that the reported concentrations of these elements would differ considerably, based on the choice of calibration standard.
For the present work, it was decided to retain the traditional calibration method employing the Micromatter standards because additional work is required to determine the appropriate calibration for evaluating field samples, and will be undertaken in the future.
Evaluation of Laboratory-contaminated Dirt Alert Filter Elements
For this phase of the program, Dirt Alert filter elements, corresponding to an engine lube application with a 30 m filtration rating were used. The four Dirt Alert filter elements, designated S/N 1 through S/N 4, were loaded with four different mixtures of contaminants (chemical elements), shown in Table 1.
A test set-up, designed to simulate the engine lube system, was used for loading the four filter elements. Each contaminant was added, sequentially, to the reservoir, in solid form, and allowed to recirculate through the filter element for about 20 minutes. Two regular filter elements, without Dirt Alert diagnostic layers but otherwise identical in construction, were loaded with contaminant mixtures corresponding to S/N 1 and S/N 4, respectively, as a control.
Subsequent to the contaminant loading, the Dirt Alert diagnostic layers from the four filter elements were removed (pulled out), and three sections (beginning, middle and end) were evaluated with the DLA. Three areas in each section were evaluated. For comparison, SEM-EDX evaluation of the three sections of each diagnostic layer was also performed.
Contaminant was flushed off the two filter elements without the Dirt Alert diagnostic layers - designated as Filter Rinse No. 1 and Filter Rinse No. 4 - onto 0.8 m analysis membranes. The analysis membranes were evaluated with the DLA. Three areas in each membrane were evaluated. SEM-EDX evaluations were also performed on each membrane.
Figure 2 shows the Dirt Alert diagnostic layer of filter element S/N 4, along with photomicrographs (~100X magnification) of the contaminant on the diagnostic layer and the contaminant on the analysis membrane corresponding to Filter Rinse No. 4.
Note: The Dirt Alert layer averages are based on three sections: beginning,
middle and end; three areas in each section. The filter rinse averages are
based on three areas of the membrane.
Table 2 shows the results of the analyses: the concentrations of the chemical elements, determined from the EDXRF analysis of the diagnostic layers, for Dirt Alert filter elements S/N 1 and S/N 4, along with the corresponding Filter Rinse No. 1 and Filter Rinse No. 4. For brevity, the results for Dirt Alert filter elements S/N 2 and S/N 3 are omitted. (The trend of the results for these filter elements were similar to S/N 1 and S/N 4.)
Comparison of the concentrations of the chemical elements in Table 2 with the concentrations used to load the filter elements in Table 1, shows that, in general, the trend of concentrations is reproduced for the higher atomic number chemical elements (Cr and above), but the concentrations are under estimated for the lighter chemical elements (Al, Mg and Si).
It should be noted that a more quantitative agreement is precluded by the fact that the porosity of the diagnostic layer would permit a significant fraction of the contaminant to pass through, depending on the size distribution, and be collected in the filtration medium of the filter element.
Additional factors for the lighter elements include the current prototype DLA’s lower sensitivity for lighter chemical elements, the calibration standards used, and matrix effects.
With the exception of the lighter chemical elements, there was also general agreement between the EDXRF and SEM-EDX spectra for the Dirt Alert diagnostic layers S/N 1 - S/N 4 and Filter Rinse No. 1 and No. 4.
Because the analysis membranes for Filter Rinse No. 1 and No. 4 were prepared by rinsing off contaminant from the filter elements, the results would be similar to those obtained by the current methods used to evaluate filter debris.
In general, the chemical element concentration trends are similar to those for Dirt Alert diagnostic layers S/N 1 and S/N 4. A noteworthy observation is the large standard deviations in the estimated chemical element concentrations for the contaminant on the Dirt Alert diagnostic layers S/N 1 and S/N 4 (Table 2). They are about the same magnitude as the concentration values at the lower concentrations.
A primary factor contributing to this would be the nonuniformity of contaminant distribution on the diagnostic layers (visible in the Dirt Alert diagnostic layer S/N 4 shown in Figure 2) due to non-homogeneous flow characteristics; the flow inlet/outlet configuration for the Dirt Alert filter element housing causes the flow to impinge on one side of the filtration medium and then exit the filter at right angles to the inlet.
![]() |
Diagnostic Layer S/N 4 |
![]() |
Filter Rinse No. 4 |
![]() |
|
Figure 2. Dirt Alert S/N 4
|
Visual inspection of the diagnostic layer S/N 4 showed that the lack of homogeneity in contaminant distribution was primarily along the length of the diagnostic layer. Thus, increasing the sampling along the length of the diagnostic layer would alleviate the effects of the nonuniform contaminant distribution.
The standard deviations in the estimated chemical element concentrations for Filter Rinse No. 4 were also large, indicating that a similar, nonhomogeneous contaminant distribution may also be an issue in preparing analysis membranes by flushing filter debris from filter elements. Again, increasing the sampling area would reduce concentration errors associated with nonhomogeneous contaminant distribution.
Dirt Alert Evaluation Using Diagnostic Layers from Aircraft Hydraulic Systems
Dirt Alert diagnostic layers, from the “Green Run” testing of hydraulic systems on aircraft, were supplied by the aircraft manufacturer.
Visual inspection of the diagnostic layers showed the presence of some metallic debris, but the overall concentration of visible contaminant was low. Three sections of each diagnostic layer (beginning, middle and end) were sampled for EDXRF and SEM-EDX analyses; one area in each section.
As stated previously, the SEM-EDX analysis was effective in detecting the lighter chemical elements, such as aluminum. Table 3 tabulates the estimated concentrations of the chemical elements determined from the EDXRF analysis. The concentrations of most of the chemical elements were low.
The standard deviations for the chemical element concentrations were significantly lower for the heavier chemical elements (chromium and higher), compared to those for the Dirt Alert filter elements described in the previous section.
This may be rationalized by the flow distribution in the hydraulic filter housing resulting in a more homogeneous deposition of contaminant on the Dirt Alert diagnostic layers. The higher deviations in the lighter chemical element (Al, Si and Mg) concentrations are likely due to the lower sensitivity of the DLA for the lighter chemical elements, the calibration standards used, and matrix effects.
Evaluation Using Helicopter Gear Box Filters, Debris from the Gear Box and a Lubricant Sample
Two main transmission gearbox (MGB) lube filter elements, along with an analysis membrane with debris from the MGB filter bowl and a sample of MGB lubricant, obtained during testing of a military helicopter MGB, were provided by the helicopter manufacturer. The filter elements, designated MGB Filter Elements No. 1 and No. 2, were not equipped with diagnostic layers, so the evaluation was conducted on the filtration media that was removed from the filter elements.
The filtration media and analysis membrane with debris from the MGB filter bowl, henceforth designated MGB Oil Debris, were subjected to EDXRF and SEM-EDX evaluations (four areas in each sample). The sample of MGB oil was evaluated using spectrometric oil analysis (SOA) for comparison of SOA and filter debris evaluation results.
![]() ![]() |
Figure 3. Contaminant from MGB
Filter Element No. 2 (left) Filter Bowl (right) |
Figure 3 shows the contaminant that was rinsed off MGB filter element No. 2 and the contaminant on the analysis membrane containing the MGB Oil Debris. A variety of metallic and oxidized metallic debris were present, along with some nonmetallic debris.
Table 4 shows the estimated chemical element concentrations determined from the EDXRF evaluation. The chemical element concentrations in Table 4 show high concentrations of zinc for the two MGB filter elements and a much lower concentration for the MGB Oil Debris. The filtration medium is comprised of glass fiber and contains both silicon and zinc, which would contribute to the high zinc concentrations.
There was also overall, qualitative agreement between the EDXRF and SEM-EDX spectra for both the MGB filter elements and the MGB Oil Debris for the higher atomic number chemical elements, with the exception of zinc; as expected, the SEM-EDX analysis showed high concentrations of silicon and lower concentrations of zinc.
The standard deviations for the chemical element concentrations were significant, about 50 percent of the concentrations, for the two MGB filter elements, but significantly lower for the MGB Oil Debris sample on the analysis membrane. As stated previously, a more comprehensive sampling of the filtration medium is required to alleviate this.
Table 5 summarizes the results of the MGB lubricant sample SOA. The analysis detected only silicon (18 ppm) and zinc (1 ppm).
The limitations of SOA with respect to particle size, if no acid digestion techniques are employed, are well known. In this case, the amount of debris in both the MGB filter elements and in the filter bowl (MGB Oil Debris) clearly illustrates the advantage of filter debris analysis.
Conclusions and Future Development
The intent of the present work was to evaluate the concept of the diagnostic filter system: the Dirt Alert diagnostic layer in conjunction with the EDXRF-based contaminant analyzer (DLA), for hydraulic and lubricant system condition monitoring. Specifically, the work was performed to evaluate, using the DLA for EDXRF analysis, the chemical composition of debris collected on a diagnostic layer of the filter element (or the filtration medium).
The results of the evaluation of Dirt Alert diagnostic layers prepared in the laboratory and diagnostic layers and filter elements from the field, show that the diagnostic filter system is viable and can be developed to provide a suitable, convenient on-site vehicle for fluid system condition monitoring.
Future development efforts will focus on:
-
Improving the semiquantitative correlation of chemical element concentrations (calibration standards, diagnostic layer sampling protocol, improved algorithms for data analysis, etc.).
-
Improving the detection of low atomic number elements.
-
Incorporating filter loading with time into the diagnostic algorithms.
-
Commencing development of an expert system to simplify data analysis and maintenance decisions for operators.
References
- Guide to Oil System Monitoring in Aircraft Gas Turbine Engines (1984). SAE AIR 1828 - SAE.
- Madhavan, P. (1994, September 28). Monitoring Gas Turbine Engine Lube System Debris via Diagnostic Filters. Proceedings of the SAE E34 Technical Symposium on Propulsion System Lubricants and Lubrication. Munich, Germany.
- Humphrey, G.R. (1996). Characterization of Debris from F404 Engine Oil Filters by Energy Dispersive X-ray Fluorescence. JOAP-TSC-TR-96-02, Joint Oil Analysis Program Technical Support Center. Pensacola, Fla.
- Humphrey, G. R., Godin, Sgt. R., Little, Capt. D., and Whitlock, R. R. (1998, April 19). Energy Dispersive X-ray Fluorescence Evaluation of Debris from F-18 Engine Oil Filters. Technology Showcase - Proceedings of the 1998 JOAP International Condition Monitoring Conference. Mobile, Ala.
- Nowell, T. (1998, April 19). The Use of the Scanning Electron Microscope in the Analysis of Wear Debris - A Case History. Technology Showcase - Proceedings of the 1998 JOAP International Condition Monitoring Conference. Mobile, Ala.
- Humphrey, G. R. (2000, April 3). Joint Strike Fighter - Analysis of Filter Debris by Energy Dispersive X-ray Fluorescence. JOAP International Condition Monitoring Conference, Technology Showcase 2000. Mobile, Ala.
Editor’s Note
This article was reprinted with permission from the Joint Oil Analysis Program (JOAP). It was presented at the International Condition Monitoring Conference held in Pensacola, Fla., on April 18-22, 2004. The article is a condensed version of the original paper.
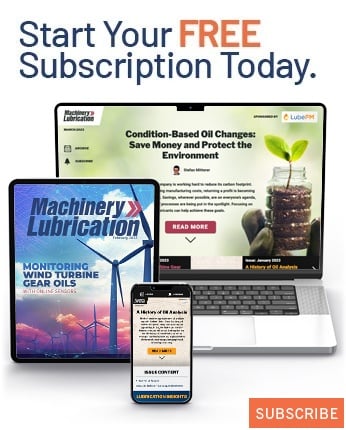