Proper lubrication of a system requires attention to detail and careful selection of units that can get the job done for a specific application. It is important to lay the groundwork for a preliminary selection of an oil lube system that matches the machine’s requirements.
Lubrication supply arrangements can generally be grouped into three categories: 1) self-contained units for supplying lubrication to individual bearings; 2) circulating systems dedicated to a single piece of equipment such as a motor, a turbine or a compressor; and 3) centralized systems in manufacturing plants, paper mills and metal working.1 Following is a brief description of each system, including its pertinent guidelines.
Self-contained Units
A self-contained unit using either simple mechanical recirculation or bath immersion is often sufficient for lubricating individual bearings. If power losses are high, then the system must be augmented with cooling.
Capillary action provides adequate oil lift from a small reservoir to feed bearings in small machines, timer motors and electrical instruments. The height h to which oil can rise in a capillary tube or between two closely spaced plates is given by
h=2 cos
/(Rpg)
(Equation No. 1)
where is the oil surface tension, typically 30 dynes/cm (mN/m), p is the density (commonly about 0.85 gm/cm3) and g is 981 cm/s2 is the acceleration due to gravity. Because oils wet most surfaces readily, cosine of contact angle
is usually unity. For example, with a capillary tube of radius R = 0.012 cm, or for 0.012-cm spacing between two parallel plates, oil is expected to rise vertically upward to
h = 2 (30) (1)/[0.012(0.85)(981)] = 6 cm (2.4 in)
Wick lubrication with its capillary action is used in millions of fractional horsepower motors. Typically, capillary lifts are used for heights up to two inches. However in railway journal bearings, they have been used for heights up to five inches. Note that the thinner the tube radius, the higher is the lift.
For medium and large machines at low-to-medium speeds, one may use oil rings, disks, chains and rotating machine elements.2,3 In these applications, oil lift is accomplished by a combination of inertia and surface tension effects. Upper speed limits for common feed arrangements are shown in Figure 1.
Figure 1. Upper Limits for Journal Bearing Lubrication Methods1
Note: Regions on graph to the left of orange lines are
acceptable for that method of lubrication.
Regions on graph to right of orange lines are
better served by the lubrication methods named to the
right of the orange line.
Circulating Oil Systems
Larger volumes of oil for high-speed machinery are commonly supplied from an independent reservoir with its associated piping system, cooler and filters.
Figure 2. Circulating Oil System Arrangement2
Figure 2 illustrates a typical oil system arrangement with oil from a reservoir being pumped through a filter, cooler, and piping to the lubricated machine components before draining back to the reservoir. Useful information for determining reservoir capacity and pump requirements, filter type and oil dwell time for various applications is summarized in Table 1.
Table 1. Circulating Oil System Characteristics
Sizing the reservoir. The volume of the oil reservoir should take into consideration the total feed to all bearings, gears, controls and other machine elements multiplied by the oil dwell time. For instance, allowing a five-minute dwell time for separation of entrained air and contaminants, a 1,000 gpm oil feed to bearings for a turbine-generator would call for a 5,000-gallon reservoir (Table 1).
In sizing the reservoir, it is also advisable to add one minute of dwell time to accommodate thermal expansion, foaming and air venting. A longer dwell time is generally required when dealing with water separation and more extensive contaminants, for example in pulp and paper or steel mills. In applications where space and weight are restricted, such as in aircraft and automobile engines, the reservoir may be simply the machine sump and the oil dwell period reduced to 60 seconds or less.
Trends stress simplification and reduced cost. Oil reservoirs are shrinking; pumps and coolers are being located in or on the reservoir; auxiliaries and controls are being mounted directly on the reservoir cover plate. In many gas turbine-generator applications, the oil reservoir is part of the base of the unit itself with oil-return ducts fabricated as sections of structural members.
Sizing the piping. Pipe diameter must be large enough to avoid undue pressure drop in feed lines, to avoid back up in drain lines at the minimum oil temperature and to avoid cavitation in pump suction lines. As indicated in Figure 3, feed lines usually operate at 5 to 10 ft/s velocity, drain lines 0.5 to 1.0 ft/s, and pump suction lines 3 to 5 ft/s.
Figure 3. Oil Line Sizes for Circulating Oil Systems1
Minimum slope s for running with a drain-line half-full is given by the following equation with viscosity (cSt), taken at the minimum operating temperature:
s = 0.00125 Q v/d4
(Equation No. 2)
where diameter d (in.) can be taken from Figure 3.
Pressure requirement. Feed pressure estimation first requires determination as to whether the feedline flow is laminar or turbulent. For this purpose, dimensionless Reynolds number Re should be calculated using:
Re = DV/v
(Equation No. 3)
where D (in.) is the pipe diameter, V (in./s) is the fluid velocity, and V (in.2 /s) is the kinematic viscosity.
If the Reynolds number is above 2,300, flow is turbulent and the pressure drop in the feed line is given by
Pl = 0.069 Q2L/(Re0.2D5)
(Equation No. 4)
where Pl is pressure drop (psi), is oil density (lb/in.3), Q is oil flow in gpm, L is equivalent line length (ft), and D is inside pipe diameter (in.).
If the Reynolds number is below 2,300, flow pressure drop Pl (psi) is given by
Pl = Qpv /(132 D4)
(Equation No. 5)
Output pump pressure P (psi) requirement can be estimated using
P = (P2 - Po) + ph + Pf
(Equation No. 6)
where P2 is the delivery pressure, Po is the atmospheric pressure in the reservoir, h represents the change in the height from the source to the delivery point, and Pf represents the total pressure drop from flow through the feed line, filter, cooler and any related components.
Pumping power requirement. Pump horsepower needed to deliver a flow of Q (gpm) at pressure P is given by:
H = QP/(1714p)
(Equation No. 7)
Where H is the pumping power (hp), and p is the pumping efficiency, commonly in the range of 0.6 to 0.8.
Filter specification. A filter is commonly located just downstream of the feed pump to remove particulates from the warm oil leaving the reservoir. Two units are often used in parallel, which allows one to be serviced while the other continues to operate. Typical filter ratings are given in Table 1 in microns (1 micron = 1 µm = 1 x 10-6m = 0.00004 in.). A cooler commonly follows the filter to lower the oil temperature by 20°F to 40°F (10°C to 20°C) before passing the oil in the 115°F to 130°F (45°C to 55°C) range to bearings and other machine elements.
Example. Establish lubrication system requirements for bearings of a machine with a feed requirement of 200 gpm of ISO VG 32 light turbine oil at 115°F and 30 psig. Assume that the bearings are located 22 feet above the reservoir and that the pipe length is 40 feet. Determine the pumping power requirement.
For a five-minute dwell time, the lubricating oil charge is 5x200 gallons. Assuming an additional free space for one-minute of flow (200 gallons) above the static oil level, total reservoir size becomes 1,200 gallons. Selecting a three-inch inside diameter feed pipe from Figure 3 gives 9.1 ft/s (109 in./s) flow velocity V. Kinematic viscosity V of VG 32 oil at 115°F is 26 cSt (26/645.2=0.0403 in.2/s) and the Reynolds number becomes
Re = DV/v = 3 x 109/0.0403 = 8,100
Table 2. Equivalent Length of Pipe Fittings
Because Reynolds number is above 2,300, flow is turbulent and pressure drop Pl in the feed line is calculated from Equation No. 4. Pipe length is 40 feet. Equivalent length of three elbows and a tee fitting from Table 2 is 3 x 25 + 60 =135 pipe diameters = 34 feet. This gives the equivalent line length L of 40 + 34 = 74 feet.
Pl = 0.069(0.037)(200)2(74)/[(8100)0.2 35] = 4.3 psi
To calculate the pump output pressure with this flow friction of 4.3 psi in the line, assume 10 psi cooler pressure drop + 10 psi filter drop for a total Pf =24.3 psi. Elevation pressure drop ph is encountered for the oil density of 0.0307 lb/in3 rising 12 x 22 feet = 264 inches. With the delivery pressure P2 =30 psi and reservoir pressure Po= 0 (psi, gauge), the pump output pressure from Equation No. 6 becomes:
P = (30-0) + 0.0307 (264) + 24.3 = 62.4 psi
Pump driving power needed to deliver Q = 200 gpm becomes from Equation No. 7:
H = QP/(1714p) = 200 x 62.4 /(1714 x 0.8) = 9.1 hp
where p= 0.8 is the assumed pump efficiency.
Drain line diameter d taken from Figure 2 is 10 inches. Minimum slope s for running with the drain line half-full can be calculated from Equation No. 2. Typically, a minimum slope of 1 in 40 toward the reservoir is common for VG 32 oil. A greater slope of 1 in 10 would be appropriate for more viscous oils in steel and paper mills. Running with the drain line half-full gives space for escape of foam and air entrained and pulled along by the draining oil.
Centralized Lubrication Systems
Limitations with self-contained lubrication or circulating systems for individual locations commonly lead to use of centralized distribution systems for production line equipment, steel and paper mills, and construction and mining machines.4 A central reservoir combined with a pumping or pressurized air system distributes metered oil flow, oil mist, or timed pulses of oil or grease.
Table 3. Oil Feed from Centralized System for
Moderate Operating Conditions
(Modified from Rieber, 1997)
Table 3 gives a guide for the quantity of oil normally fed to various machine elements. Lube system suppliers, machinery builders and lubricant suppliers should also be consulted for appropriate feed rates and lubricant specifications because requirements vary for individual installations and may double for speeds, loads and temperatures above those in conventional factory applications.
Lubricants are commonly distributed through a single pressurized line where flow-resistance fittings apportion lubricant to each delivery point. Dual feed lines are used for long distances, as in a transfer machine, with double-acting metering pistons being actuated by pressurized feed from one of the two lines. A reversing valve vents the first line back to the reservoir and supplies feed pressure to the second line. Lubricant is then delivered with the pistons moving in the opposite direction.
Oil mist orifice metering systems are used for supplying limited oil feed rates for demanding applications in petrochemical plants, and steel and paper mills.5,6 Dry mist involving oil particles up to approximately six to seven microns can be piped for distances up to 300 feet. At delivery points, the dry mist is converted to wet mist by agglomerating oil particles with classifier fittings to form larger drops, or wet sprays, which then run down adjacent surfaces. The air stream must be kept in the laminar regime below about 24 ft/s because turbulence will cause oil particles to impact the pipe wall and be removed from the air stream before reaching their delivery points.
References
- Khonsari, M.M. and Booser, E.R. Applied Tribology - Bearing Design and Lubrication. New York, N.Y.: John Wiley & Sons, 2001.
- Wilcock, D.F. and Booser, E.R. “Lubrication Techniques for Journal Bearings.” Machine Design, 1987.
- Elwell, R.C. “Ring- and Wick-oiled Starved Journal Bearings.” Tribology Data Handbook, (E.R. Booser, editor). Boca Raton, Fla.: CRC Press, 1997.
- Simpson, J.H. III. “Centralized Lubrication of Industrial Machines.” Tribology Data Handbook, Boca Raton, Fla: CRC Press, 1997.
- Bloch, H.P. and Shamin, A. Oil Mist Lubrication: Practical Applications. Lilburn, Ga.: Fairmont Press, 1998.
- Rieber, S.C. “Oil Mist Lubrication.” Tribology Data Handbook. Boca Raton, Fla.: CRC Press, 1997.
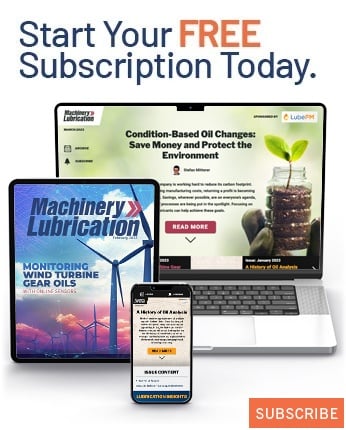