Situation Prior to Failure
The engine currently installed in truck no. 526 is a Cummins K2000 series engine that had been in production for 349 hours prior to failure.
Observation
The diagnostic engineering department observed that the oil analysis results indicated copper wear was taking place (graphically displayed overleaf). A microscopic analysis also indicated copper wear particulate.
Figure 1. Main oil gear retaining bolt and gear
retaining bushing after becoming loose. It also
indicates the amount of axial movement permissible
on the drive shaft after the bolt loosened.
Figure 2. Amount of free movement (end float) the
main oil pump drive gear was permitted after the
bolt and retaining bushing became loose.
Diagnostic Recommendations
Given that the engine was in a run-in period, changing the oil and filters was recommended.
Based on the wear particle readings, engineering also recommended cutting open the elements and examining the residue filter for any abnormalities.
Maintenance Response
While the engine oil was being drained, Sishen and Cummins maintenance personnel noticed copper wear particles on the engine sump drain plugs. They cut open the oil filters and a visual inspection revealed copper wear particulate.
The maintenance personnel removed the engine sump and discovered that the main oil pump drive gear-retaining bolt had come loose.
The loosening of the bolt caused the gear-retaining bushing to move out of the housing, resulting in excessive wear on the main drive gear shaft inner bushing and thrust washers.
As a direct consequence of the drive gear retaining bolt becoming loose, excessive play between the drive shaft and the front housing caused excessive wear on the brass bushing located in the pump housing and the brass thrust washers on either side of the gear.
A new oil pump was fitted and the truck placed back into production.
Figure 3. 526 Engine, Copper Wear Readings
Repair Costs
Estimated budget savings in case of a failure occurrence
Based on a cost of $181,388 for an engine rebuild and a life expectancy of 25,000 hours.
The cost to Sishen Iron Ore Mine would be $181,388 to replace a K2000 series engine. The life expectancy of the engine is 25,000 hours.
$181,388 / 25,000 = $7.25 per hour (depreciation cost).
(Excluding unscheduled down time to replace engine of $512 X 16 hours = $8,192).
The cost to have haul truck no. 526 out of production is $512 per hour. An engine replacement takes 16 hours to perform. $512 X 16 hours = $8,192
Engine life of 349 hours X $7.27 = $2,537
The engine had been in service for 349 hours before failure. 349 X $7.27 = $2,537 (depreciation cost).
Estimated savings excluding unscheduled downtime: $181,634 (cost to replace engine) – $2,537 (depreciation cost) = $179,097
Total savings including unscheduled downtime estimated at: $179,129 + $8,206 = $187,335
$181,634 (cost to replace engine) – $2,537 (depreciation cost) = $179,097.
The maintenance personnel were able to schedule the truck for engine repairs, eliminating any unscheduled downtime.
Direct Cause of Failures
Based on a visual inspection of the gear oil pump and according to maintenance and OEM personnel, it is likely that the main oil pump drive-retaining bolt had come loose due to incorrect torqueing of the bolt.
Proactive Actions
Cummins personnel will ensure that all oil pump bolts be retorqued before installation.
Editor’s Note:
Currency figures used in this article are based on exchange rates at the time of publication.
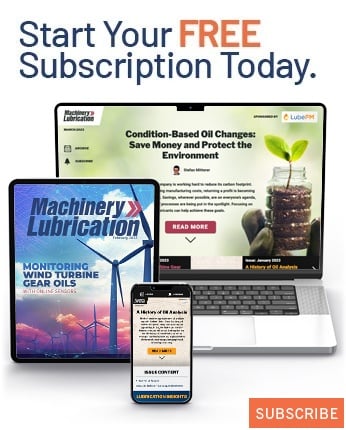