During the first week in August, Noria held public courses for Oil Analysis Level I and Machinery Lubrication Level I in Toronto. Typically, many out-of-towners join us for these seminars. In order to accommodate these weary travelers, the seminars are held in a hotel located near Toronto’s Pearson International Airport.
On August 2nd, as the first day of the seminar was concluding, we couldn’t help but notice the strange smell that filled the halls and corridors of the hotel. One look at the television or out the window and the cause of they mysterious smell was apparent.
An Air France A-340 jetliner had made a crash landing and was burning just beyond runway 24L. The aircraft had touched down, skidded off the runway, broke into three sections, and burst into flames that would eventually burn for hours.
Evacuation
There were no fatalities in this Airbus A-340 crash. Even though the plane was destroyed by fire after landing in a ravine 200 meters beyond the runway, all of the passengers and crew were evacuated to safety. Most of the 300 passengers were evacuated from the Air France jet in 52 seconds (the time it took for emergency vehicles to arrive), and the remaining passengers and crew were off the plane in less than two minutes.
This evacuation has been described as nothing short of a miracle, but a large part of the evacuation was due strictly to technology, precise training and the professionalism of the crew and emergency personnel.
It has been reported that the textbook evacuation time for an Airbus A-340 is less than two minutes. However, textbook theories are often far from reality, but in this case, the textbook proved accurate. So what does this have to do with oil analysis or machinery lubrication?
OEM Manuals
With most new purchases of production equipment, the product arrives at the facility with an original equipment manufacturer (OEM) operator’s manual. The manual is basically a textbook on how to get the most from the new production equipment.
Typically, this is a great reference for installation, setup, break-in, etc. But are the recommendations in these manuals accurate? Do the recommendations cover the broad possibilities of all installations? Absolutely not.
Best Practice
I recently had a conversation with a maintenance supervisor of a large steel mill. I had delivered a lubrication audit of one area of the mill and was discussing the benefits of such a program in other areas of the mill.
He asked me why it was necessary to audit all the individual assets in the mill, and why they could not simply apply the best practice delivered in the first lubrication audit to the rest of the mill. I answered that “best practice” is a broad term.
Best practice for a gearbox in a given application is not necessarily the same for an identical gearbox in another application.
For example, in the northern part of the United States, winter temperatures can drop well below freezing for extended periods of time. A gearbox sitting outside in this environment will require a different lubricant than the identical gearbox operating in a warmer environment.
The nameplate, however, indicates that the required viscosity for both gearboxes is an ISO VG 220 with EP additives. So what is considered best practice? Do we follow the textbook recommendations for both gearboxes or is this a case of buyer beware?
In this case, the generic viscosity requirement for these gearboxes may not be applicable in both cases. The OEM failed to recognize the broad environment its products could operate in, and made a less-than-precise recommendation.
When we blindly try to apply best- practice maintenance and lubrication tactics to a broad selection of like components, we lose the precision that makes one particular practice better than another. Each asset needs to be audited individually to identify the best practice for the asset.
Much like the way the crew of Air France flight 358 was prepared for several dissimilar precision evacuations, the way personnel maintain and lubricate identical equipment in dissimilar applications needs to be specific and precise as well.
The ability to optimize any product or process relies on a great deal of understanding and comprehension of what the ultimate objective is. Whether the intent is to extend the service life of a machine or component, or to evacuate 309 people from a burning Airbus A-340, all potential threats to reaching the goal need to be examined and evaluated.
When applying this approach to machinery lubrication, all factors (climate, duty cycle, operating environment, process contamination, etc.) must be considered. When individual considerations have been made for each of our plants assets, then the ability to apply specific best-practice maintenance is well within our reach.
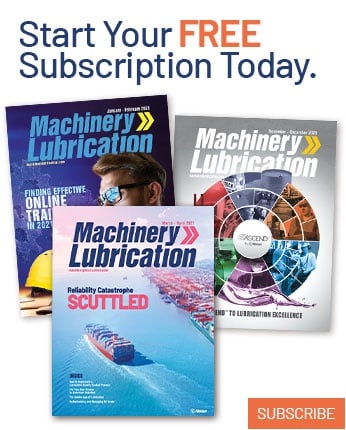