In my column in the November- December issue of the magazine, I presented a case study in which a ship loading gearbox suffered a catastrophic failure just two days after receiving the new replacement gearbox.
The focus on this particular case study was on the proper setting of alarms and limits specifically related to wear debris with an introduction to the value of combining oil sample data with vibration data results.
In this column, I’d like to present new data from the same conveyor gearbox, however, with a different focal point. It will show the importance of confirming OEM recommendations over what is known to be true.
Case Study
For the conveyor gearbox in question, previous oil analysis results, coupled with customized alarm levels for wear debris, indicated an imminent failure condition. This was verified with input from another PdM technology, vibration analysis, which indicated an abnormality on the input bearing.
It was noted in the previous article that an inspection was performed to determine the cause of failure. Among the various issues considered, analysts reviewed the role that the lubricant viscosity grade played in the failure.
It was reported at that time that the in-use viscosity grade conformed to the original equipment manufacturer’s (OEM) designated grade.
Figure 1 shows the iron wear trend prior to the failure, as well as the wear trend after the failure with the new gearbox in place. Initial thoughts on the increased wear were related to break-in wear. As samples were submitted, however, the wear rate was recognized to be far from normal.
Figure 1. Iron Wear
The viscosity grade once again became a suspect when the results of the failure analysis were reexamined in an effort to identify a cause of the apparent elevated wear rate. Despite earlier assurances that the viscosity was correct, the technicians were prompted to double-check and confirm the manufacturer’s recommendation against the current product.
With the closer examination, it was discovered that the operator’s manual for this gearbox indicated the correct viscosity grade at its typical ambient temperature to be an ISO 320.
The product selected, and at that point in use, was an ISO 680; a grade that is typically reserved for units with higher loads and lower speeds than commonly found in conveyor drive ap5plications like this one. Provided with this information, plant maintenance performed a drain, flush and refill with the correct grade of lubricant.
In the most recent sample for this gearbox, taken in December 2005, the iron value is considerably lower than in previous samples. Future routine monitoring will allow for proper implementation and use of customized alarm limits.
Lesson Learned
Recommended lubricants should always be confirmed if in question. Case in point: this gearbox suffered a level of wear that could have been avoided. It is safe to say that much useful life was lost from this unit due to this common error.
While operating conditions may occasionally warrant the use of a lubricant other than that recommended by the manufacturer, the OEM recommendations should be strongly considered as the starting point. Careful testing and documentation should be conducted prior to making a viscosity change in any piece of equipment.
Figure 2. Iron vs. Viscosity
This case is a prime example of the importance of proper viscosity selection. While it is widely understood that using a lubricant too low in viscosity will result in insufficient lubricant film, it is also important to understand that using a lubricant too high in viscosity can produce similar problems.
In this case there was an apparent loss of lubricant film due to the reduced oil flow through small passages, which were designed for a lower viscosity lubricant. See Figure 2 for a comparison of iron and viscosity for this specific gearbox.
Related Reading
Matt Spurlock. “Knowledge is Power.” Practicing Oil Analysis magazine, November-December 2005.
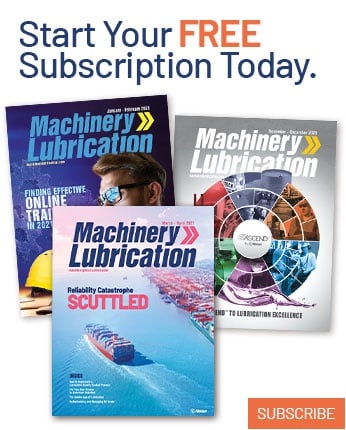